2025 Auteur: Howard Calhoun | [email protected]. Dernière modifié: 2025-01-24 13:16
Le métal est la base de toute civilisation moderne. En un an, l'humanité moderne extrait et traite à elle seule une telle quantité de fer qu'avant que le monde entier ne le récupère pendant au moins deux siècles. Et ce besoin est pleinement justifié, puisque la construction à elle seule consomme une quantité incroyable d'acier. Sans surprise, la coulée de métal dans de telles conditions est constamment améliorée.
Un peu d'histoire
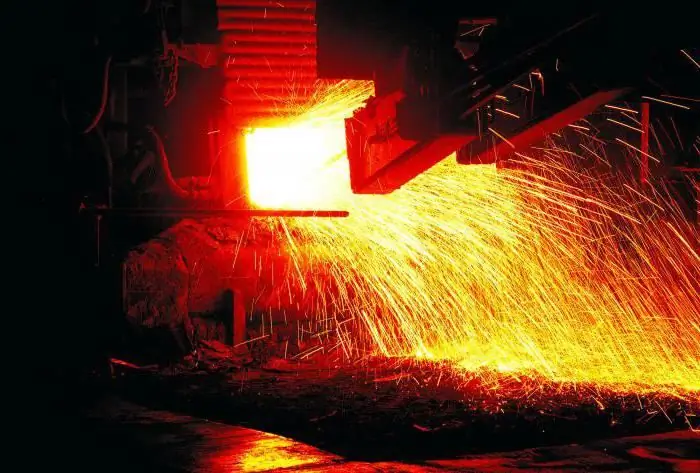
La caractéristique la plus importante du fer à prendre, solidifiant, la forme "proposée" à lui, une personne remarquée dans les temps anciens. Aujourd'hui, presque tous les scientifiques supposent que la première connaissance de l'homme avec le métal a eu lieu grâce aux météorites. Le fer météoritique était fusible et facile à traiter, de sorte que les bases de la fonte ont été étudiées par certaines civilisations naissantes il y a longtemps.
Dans notre pays, la fonte des métaux est une activité respectée et honorable depuis des siècles, les gens ont toujours traité ce métier avec beaucoup de respect. Le "Tsar Cannon" et le "Tsar Bell" sont largement connus, qui sont des chefs-d'œuvre du talent de coulée des maîtres russes, même si l'un d'eux n'a jamais sonné et que le second n'a pas tiré. Les fondeurs de l'Oural sous le règne de Pierre le Granda acquis une renommée particulière en tant que fournisseur d'armes fiables pour l'armée. Cependant, ils portent à juste titre ce titre même maintenant. Avant d'aborder les principaux types de coulée de métal, il est nécessaire de dire quelques mots sur les caractéristiques requises des matières premières.
Quel devrait être le métal pour la coulée
La propriété la plus importante du métal à utiliser pour la coulée est sa fluidité. L'alliage sous forme fondue doit s'écouler le plus facilement possible d'un creuset à l'autre, tout en remplissant ses moindres recoins. Plus la fluidité est élevée, plus les parois peuvent être minces dans le produit fini. Avec du métal qui s'étale mal, c'est beaucoup plus difficile. Dans des conditions normales, il parvient à saisir bien plus tôt qu'il ne comble toutes les lacunes du formulaire. C'est la difficulté à laquelle sont confrontés les industriels lors de la coulée d'alliages métalliques.
C'est sans surprise que la fonte est devenue le matériau de prédilection de la fonderie. En effet, cet alliage a une excellente fluidité, ce qui le rend relativement facile à travailler. L'acier est loin d'être aussi fluide, et donc, pour remplir complètement le moule (pour qu'il n'y ait pas de cavités et de vides), il faut recourir à une variété d'astuces.
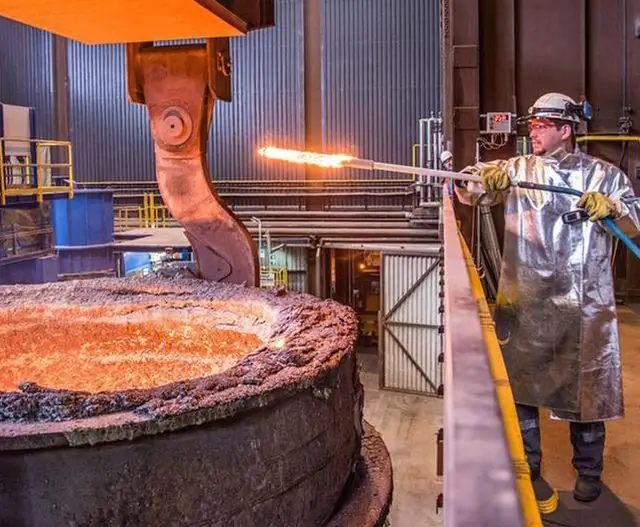
Dans le cas le plus simple, lorsque la coulée de métal à domicile est requise, les matières premières sont fondues et versées dans l'eau en petites portions: c'est ainsi, notamment, que vous pouvez fabriquer des plombs pour la pêche. Mais cette méthode est relativement largement utilisée même dans l'industrie de l'armement ! Du haut d'une tour spéciale, ressemblant à une tour de refroidissement en contour, fondumétal. La hauteur de la structure est telle qu'une goutte parfaitement formée, déjà refroidie, atteint le sol. C'est ainsi que la grenaille est produite à l'échelle industrielle.
Méthode de coulée de terre
La méthode la plus simple et la plus ancienne consiste à couler du métal dans le sol. Mais sa «simplicité» est un concept relativement conditionnel, car ce travail nécessite une préparation extrêmement minutieuse. Qu'est-ce que cela signifie ?
Tout d'abord, un modèle grandeur nature et le plus détaillé du futur casting est réalisé dans l'atelier de modélisme. De plus, sa taille doit être un peu plus grande que le produit à obtenir, car le métal se déposera une fois refroidi. En règle générale, le modèle est rendu détachable, à partir de deux moitiés.
Une fois cela fait, le sable de moulage spécial est préparé. Si le futur produit doit avoir des cavités internes et des vides, il sera également nécessaire de préparer les tiges, ainsi qu'un composé de moulage supplémentaire. Ils doivent remplir temporairement les zones «vides» de la pièce finie. Si vous êtes intéressé par la coulée de métaux à la maison, assurez-vous de garder ce fait à l'esprit, car sinon un flacon déjà rempli peut simplement être déchiré par la pression, et les conséquences peuvent être les plus tristes.
De quoi sont faits les sables à mouler ?
La base est constituée de différentes qualités de sables et d'argiles, ainsi que de liants. Leur rôle peut être joué par les huiles naturelles et synthétiques, l'huile siccative, la résine, la colophane et même le goudron.
Vient ensuite le temps des mouleurs, dont la tâche est de fabriquer des moules. Si vous expliquezplus facile, cela se fait comme ceci: une boîte en bois est prise, une moitié du moule y est placée (il est également détachable), et les espaces entre les parois du modèle et le moule sont bouchés avec une composition de moulage.
La même chose est faite avec la seconde moitié et fixez les deux parties avec des épingles. Il est important de noter que deux cônes spéciaux sont insérés dans la partie du formulaire qui sera en haut lors du coulage. L'un d'eux est utilisé pour verser le métal en fusion, le second pour évacuer les gaz en expansion.
Fin de la phase préparatoire
Et maintenant, il est peut-être temps de passer à la partie la plus cruciale de l'opération. Les flacons sont très soigneusement séparés, en essayant d'empêcher la violation de l'intégrité du sable. Après cela, deux empreintes claires et détaillées de la future partie restent dans le sol. Après cela, ils sont recouverts d'une peinture spéciale. Ceci est fait pour que le métal en fusion n'entre pas en contact direct avec le sol de sable. La technologie de coulée de métal ne devrait pas le permettre, sinon la qualité du produit fini pourrait se détériorer considérablement.
Si cela est nécessaire, en même temps, un passage de porte supplémentaire est coupé, ce qui est nécessaire pour verser la masse fondue. Les flacons sont à nouveau pliés et connectés aussi solidement que possible. Une fois que le sable est légèrement sec, vous pouvez commencer à couler.
Commencer à diffuser
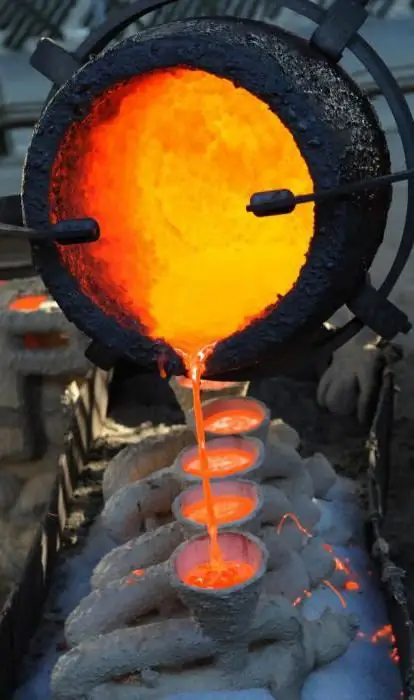
Premièrement, dans les coupoles, c'est-à-dire les fours spéciaux, les ébauches en fonte sont fondues. S'il est nécessaire de couler de l'acier, les matières premières sont fondues dans des hauts fourneaux, des foyers ouverts, des onduleurs et d'autres fours. Apporterl'état de fusion des métaux non ferreux, utilisez des appareils de fusion spécialisés.
Tout, vous pouvez commencer à caster. S'il n'y a qu'un seul formulaire, la masse fondue y est versée avec une louche, individuellement. Dans d'autres cas, en règle générale, un convoyeur est organisé: soit une bande avec des flans passe sous la poche, soit la poche se déplace sur les rangées de flacons. Tout dépend uniquement de l'organisation de la production. Lorsque le moment est venu et que le métal refroidit, il est retiré du moule. En principe, cette méthode est idéale dans les cas où la coulée de métal est requise à domicile (pour une forge, par exemple). Rien de plus parfait dans de telles conditions ne sera de toute façon réalisé.
Les machines de sablage ou de meulage éliminent le tartre et le sable de moulage adhérent du produit fini. Soit dit en passant, cette méthode a été activement utilisée dans la production de chars pendant la Grande Guerre patriotique. C'est ainsi que les tours moulées ont été produites, et la simplicité et la fabricabilité de ce processus ont permis de produire un grand nombre de véhicules militaires dont le front avait tant besoin. Quels autres types de moulage de métal existent ?
Coupe sous pression
Mais maintenant, ils utilisent des méthodes beaucoup plus avancées et technologiquement avancées pour la production de produits moulés. Par exemple, la coulée de métal dans un moule de refroidissement. En principe, cette méthode ressemble à bien des égards à celle décrite ci-dessus, car dans ce cas, des moules de coulée sont également utilisés. Seulement en même temps, ils sont en métal, ce qui simplifie grandement le processus de production à grande échelle.
Ainsi, les cônes et les tiges sont insérés en deux moitiés (pour couler le métal et former des vides), etpuis fixez-les fermement l'un à l'autre. Tout, vous pouvez vous mettre au travail. La particularité de cette méthode est qu'ici le métal fondu se solidifie extrêmement rapidement, il y a la possibilité d'un refroidissement forcé des moules, et donc le processus de libération est beaucoup plus rapide. Avec un seul moule, vous pouvez obtenir des centaines, voire des milliers de moulages, sans passer beaucoup de temps sur la préparation individuelle des moules et des sables.
Quelques inconvénients de la méthode
L'inconvénient de cette méthode de coulée est le fait que seuls les types de métaux caractérisés par une fluidité accrue sous forme fondue lui conviennent. Par exemple, seule la coulée sous pression convient à l'acier (à ce sujet ci-dessous), car ce matériau n'a pas du tout une bonne fluidité. Sous l'action de l'air comprimé, même les nuances d'acier les plus « ductiles » prennent beaucoup mieux la forme requise. La mauvaise chose est qu'un moule de refroidissement ordinaire ne peut tout simplement pas résister à des conditions de production aussi extrêmes et s'effondrera. Par conséquent, vous devez utiliser une méthode de production spéciale, dont nous parlerons ci-dessous.
Moulage par injection
Comment s'effectue le moulage sous pression - sous pression - des métaux ? Nous avons déjà examiné certains aspects ci-dessus, mais il est encore nécessaire de divulguer ce problème plus en détail. Tout est assez simple. Tout d'abord, un moule de coulée composé de nuances d'acier de qualité est nécessaire, qui peut être une forme interne complexe en plusieurs étapes. Deuxièmement, nous avons besoin d'un équipement de pompage capable de délivrer de sept à sept cents MP.
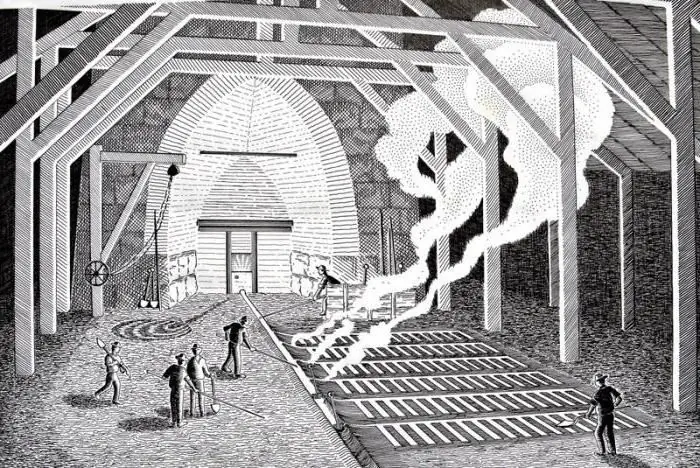
Avantage principalcette méthode de fusion est une productivité élevée. Quoi d'autre fournit le moulage par injection? Dans ce cas, beaucoup moins de métal est utilisé et la qualité de surface du produit fini est très bonne. Cette dernière circonstance implique le rejet d'une procédure de nettoyage et de meulage complexe et plutôt ennuyeuse. Quels matériaux sont les meilleurs matériaux pour cette méthode de production afin de produire des produits finis et des pièces ?
Les alliages les plus couramment utilisés sont à base d'aluminium, de zinc, de cuivre et d'étain-plomb (fonderie de métaux non ferreux). Leur température de fusion est relativement basse, et par conséquent une très haute fabricabilité de l'ensemble du procédé est obtenue. De plus, cette matière première présente un sédiment relativement faible lors du refroidissement. Cela signifie qu'il est possible de produire des pièces avec de très petites tolérances, ce qui est extrêmement important dans la production de la technologie moderne.
La complexité de cette méthode est que lorsque les produits finis sont séparés des moules, ils peuvent être endommagés. De plus, ce procédé ne convient que pour la fabrication de pièces avec une épaisseur de paroi relativement faible. Le fait est qu'une épaisse couche de métal durcira de manière extrêmement inégale, ce qui prédéterminera la formation de coquilles et de cavités.
Variétés d'installations pour la coulée sous pression
Toutes les machines utilisées dans cette méthode de coulée de produits métalliques sont divisées en deux grands groupes: avec une chambre de coulée chaude et froide. La variété "chaude" ne peut le plus souvent être utilisée que pour les alliages à base de zinc. Dans ce cas, la chambre de coulée elle-même est immergée dans le métal chaud. Sous pressionde l'air ou un piston spécial, il s'écoule dans la cavité de coulée.
En règle générale, une forte force d'injection n'est pas nécessaire, une pression allant jusqu'à 35-70 MPa suffit. Ainsi, dans ce cas, les moules pour la coulée de métal peuvent être beaucoup plus simples et moins chers, ce qui a l'effet le plus favorable sur le coût final du produit. Dans les moules de coulée à froid, le métal en fusion doit être « entraîné » profondément dans la chambre de coulée sous une pression particulièrement élevée. Dans le même temps, elle peut atteindre 700 MPa.
Où sont utilisées les pièces moulées par injection ?
Ils sont partout. Dans les téléphones, les ordinateurs, les appareils photo et les machines à laver, partout il y a des détails obtenus à l'aide de cette méthode particulière. Il est particulièrement largement utilisé par le génie mécanique, y compris ceux directement liés à l'industrie aéronautique et même spatiale. La masse des pièces moulées peut varier de quelques grammes à 50 kilogrammes (et même plus). Peut-on utiliser un autre "traitement" des métaux par coulée ? Oui, et il y a bien d'autres façons.
Fonte à la cire perdue
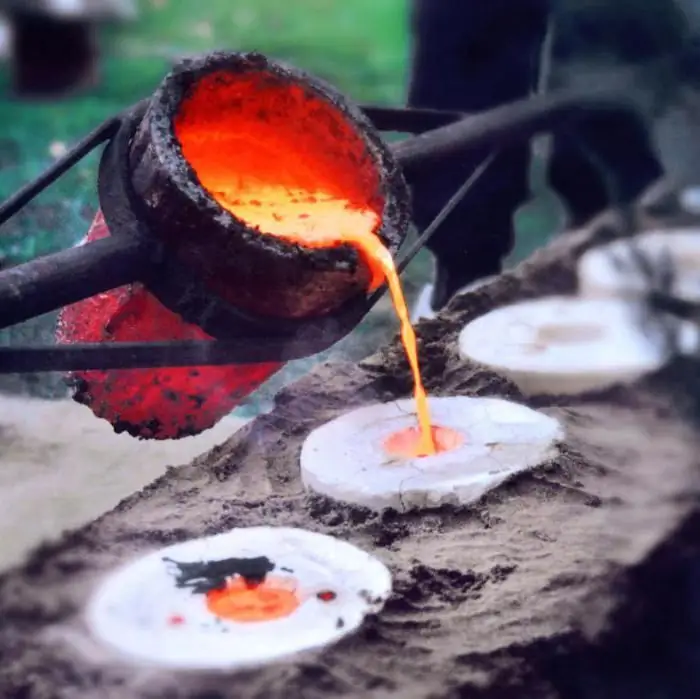
Comme dans le tout premier cas que nous avons envisagé, depuis l'Antiquité, l'humanité connaît la méthode consistant à verser du métal en fusion dans un modèle pré-préparé en paraffine ou en cire. Il est simplement placé dans le ballon et les espaces sont remplis de sable de moulage. La fonte dissout la cire et remplit idéalement tout le volume de la pièce primaire. Cette méthode est bonne car le modèle n'a pas besoin d'être sorti du flacon. De plus, il est possible d'obtenir des pièces d'une qualité tout simplement parfaite, ce procédé de fonderieles métaux sont relativement faciles à automatiser.
Coquillage
Si la coulée est relativement simple et qu'une résistance « spatiale » du produit fini n'est pas requise, la méthode de coulée dans des moules en coquille peut être utilisée. Ils sont fabriqués depuis des temps immémoriaux, et le sable de quartz fin et la résine sont utilisés comme base. Aujourd'hui, bien sûr, divers composés synthétiques sont utilisés comme ces derniers.
Ensuite, des modèles métalliques pliables sont pris, composés de deux moitiés, et placés sur une surface chauffée à environ 300 degrés Celsius. Ensuite, le mélange de moulage (à partir de sable et de résine sèche) est versé au même endroit afin qu'il recouvre complètement la surface des modèles métalliques. Sous l'effet de la chaleur, la résine fond et un "flacon" assez solide apparaît dans l'épaisseur du sable.
Dès que tout se refroidit un peu, les lingots de métal peuvent être retirés et le sable peut être envoyé au four pour être « torréfié ». Après cela, des formes suffisamment solides sont obtenues: en reliant leurs deux moitiés, du métal en fusion peut y être versé. Quelles autres méthodes de coulée de métal existe-t-il ?
coulée centrifuge
Dans ce cas, la fonte est versée dans une forme spéciale, qui tourne à très grande vitesse dans une projection horizontale ou verticale. Grâce à l'action de puissantes forces centrifuges appliquées de manière égale, le métal s'écoule uniformément dans tous les interstices du moule, obtenant ainsi une haute qualité du produit fini. Cette méthode de coulée est idéale pour la production de différents types de tuyaux. Il permet de former une épaisseur beaucoup plus uniformemurs, ce qui est extrêmement difficile à réaliser avec des méthodes "statiques".
coulée sous laitier électrique
Existe-t-il des manières de couler des métaux qui peuvent à juste titre être qualifiées de modernes ? Coulée sous laitier électrolytique. Dans ce cas, le métal liquide est d'abord obtenu en agissant sur la matière première préalablement préparée avec de puissantes décharges d'arc électrique. La méthode sans arc peut également être utilisée lorsque le fer est fondu à partir de la chaleur accumulée par le laitier. Mais le dernier est affecté par de puissantes décharges.
Après cela, le métal liquide, qui n'est jamais entré en contact avec l'air pendant tout le processus, pénètre dans la chambre de cristallisation, qui "en combinaison" est également un moule de coulée. Cette méthode est utilisée pour des pièces moulées relativement simples et massives, pour la fabrication desquelles de nombreuses conditions n'ont pas besoin d'être respectées.
Remplissage sous vide
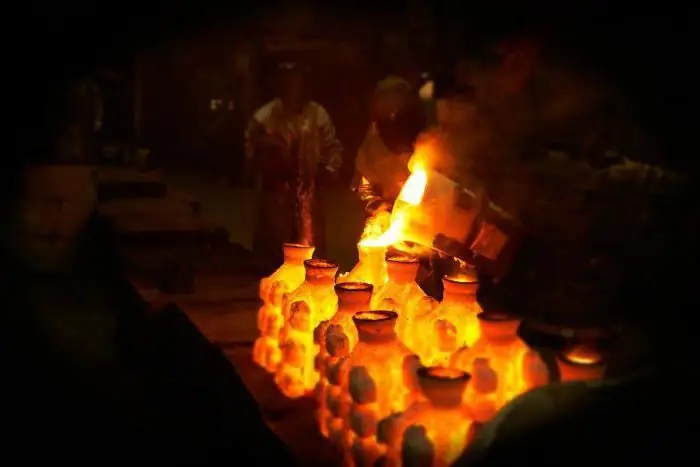
S'applique uniquement aux matériaux "haut de gamme" tels que l'or, le titane, l'acier inoxydable. Dans ce cas, le métal est fondu sous vide, puis rapidement (dans les mêmes conditions) est distribué dans des moules. Le procédé est bon en ce que lorsqu'il est utilisé, la formation de cavités d'air et de cavités dans le produit est pratiquement exclue, car la quantité de gaz qui y est présente est minime. Il est important de se rappeler que le poids des pièces moulées dans ce cas ne peut pas dépasser cent ou deux kilogrammes.
Est-il possible d'obtenir des pièces plus grandes ?
Oui, une telle technologie existe. Mais il ne peut être utilisé que dans les cas où cent tonnes d'acier sont traitées en même temps.et plus. Tout d'abord, le métal est fondu sous vide, puis il n'est pas versé dans des moules, mais dans des poches de moulage spéciales, qui sont également protégées de l'air entrant dans leur cavité.
Après cela, la fonte finie peut être distribuée dans des moules, à partir desquels l'air a également été préalablement pompé avec une pompe. L'acier obtenu à la suite d'un tel processus technologique est assez coûteux. Il est utilisé pour le forgeage, ainsi que certains types du même moulage, lorsqu'il est nécessaire d'obtenir des ébauches et des pièces de la plus haute qualité.
Coulée sur des modèles gazéifiés (brûlés)
En termes de qualité et de simplicité de coulée, cette méthode est l'une des plus rentables et est donc de plus en plus utilisée dans l'industrie moderne. Une telle coulée de métal, dont la production augmente d'année en année, est particulièrement populaire en RPC et aux États-Unis, car les bases industrielles de ces deux pays se distinguent par le plus grand besoin d'acier de haute qualité. L'avantage de cette méthode est qu'elle permet la production de pièces moulées sans aucune restriction de poids et de taille.
À bien des égards, cette méthode est similaire à celles décrites ci-dessus: par exemple, dans ce cas, le modèle principal n'est pas utilisé à partir de cire ou de pâte à modeler, mais à partir de la mousse désormais répandue. Ce matériau ayant ses propres spécificités, le mélange sable-liant est tassé dans le ballon sous une pression d'environ 50 kPa. Le plus souvent, cette méthode est pratiquée dans les cas où il est nécessaire de fabriquer des pièces pesant de 100 grammes à deux tonnes.
Cependant, nous avons déjà dit que certaines restrictions strictes surdétails de taille non. Ainsi, en utilisant cette méthode de coulée, même des composants pour moteurs de navires peuvent être produits, qui n'ont jamais été de taille "modeste". Pour chaque tonne de matières premières métalliques, la quantité suivante de matériaux supplémentaires est consommée:
- Sable quartz fin - 50 kg.
- Revêtement antiadhésif spécial - 25 kg.
- Mousse de polystyrène granulé - 6 kg.
- Film polyéthylène dense - 10 pi² m.
Tout le sable de moulage est du sable de quartz pur sans aucun additif ni additif supplémentaire. Il peut être réutilisable à environ 95-97 %, ce qui améliore considérablement l'économie et réduit le coût du processus.
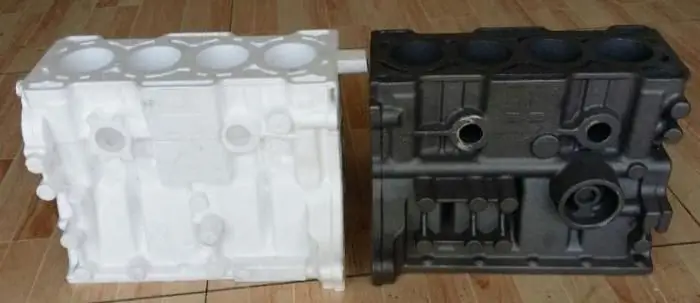
Ainsi, la coulée des métaux (la physique du processus a été partiellement prise en compte par nous) est un phénomène "à multiples facettes", car il existe aujourd'hui de nombreuses nouvelles méthodes. Dans le même temps, l'industrie moderne applique des méthodes utilisées il y a plusieurs milliers d'années, les adaptant quelque peu aux réalités actuelles.
Conseillé:
Métaux ferreux : gisements, stockage. Métallurgie des métaux ferreux
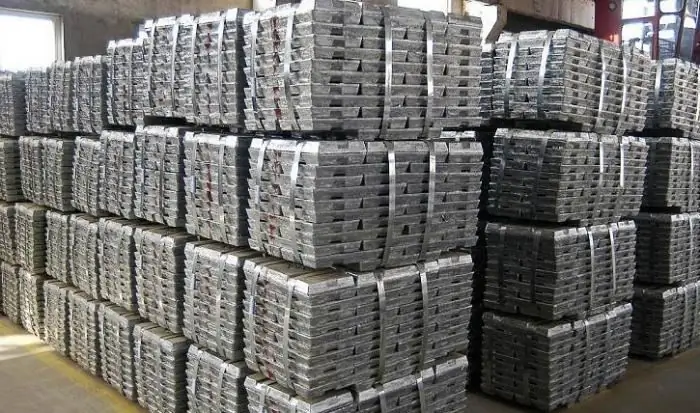
Les métaux sont des matériaux qui ne perdent jamais leur pertinence. Ils sont largement utilisés dans les ménages et l'industrie
Métaux non ferreux : caractéristiques et domaines d'utilisation. Traitement des métaux non ferreux
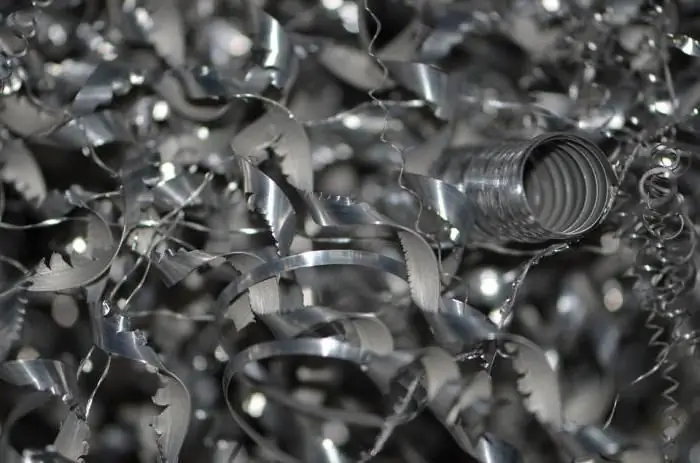
Les métaux non ferreux et leurs alliages sont largement utilisés dans l'industrie. Ils sont utilisés pour fabriquer des machines, des outils de travail, des matériaux de construction et des matériaux. Ils sont même utilisés dans l'art, par exemple, pour la construction de monuments et de sculptures. Que sont les métaux non ferreux ? Quelles fonctionnalités ont-ils ? Découvrons-le
Cotations des métaux précieux à la Sberbank. Métaux précieux (Sberbank): prix
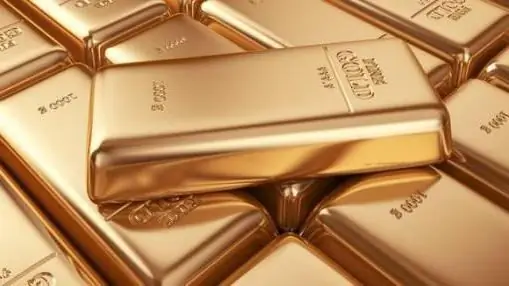
L'un des investissements les plus rentables est l'achat de métaux précieux tels que l'or, l'argent, le platine, le palladium. C'est le cas depuis de nombreuses années et le reste aujourd'hui. En période de crise économique, cette option est encore plus pertinente
Le traitement thermique de l'acier est un processus important dans la production de métaux
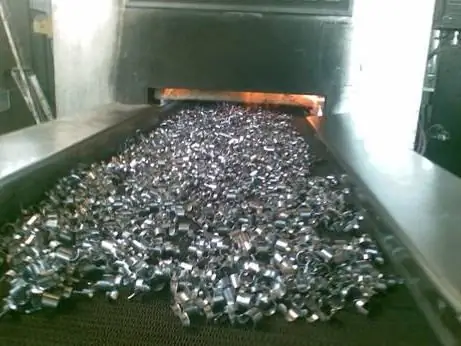
Le traitement thermique de l'acier confère à tout produit en acier les propriétés souhaitées. Ce processus est une étape importante dans la production d'alliage de fer
Coupe des métaux au plasma. Équipement de travail des métaux
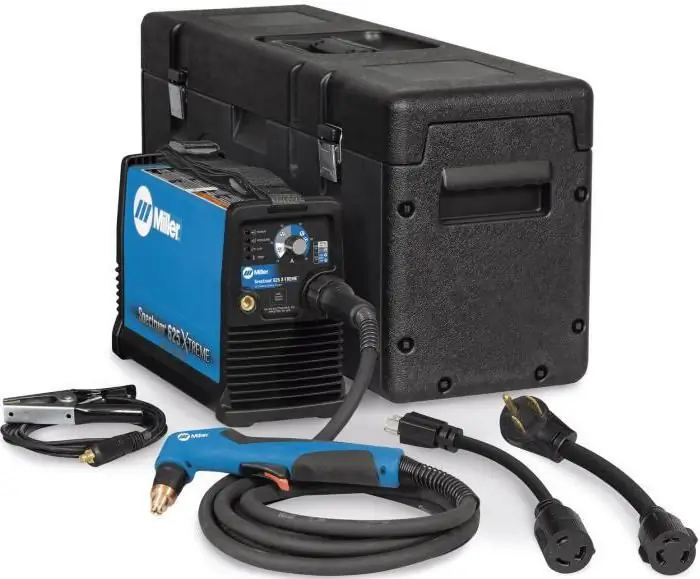
Lors de l'achat d'un découpeur plasma, vous devez toujours privilégier la qualité. Méfiez-vous de la tentation d'acheter un appareil bon marché de mauvaise qualité, car son usure rapide à long terme entraînera des coûts beaucoup plus élevés