2025 Auteur: Howard Calhoun | [email protected]. Dernière modifié: 2025-01-24 13:16
L'utilisation de modèles d'investissement est une méthode assez populaire de production de fonderie. La méthode se distingue par la complexité du processus technologique et les coûts de main-d'œuvre élevés pour les processus préparatoires. Par conséquent, il est utilisé lorsqu'il est nécessaire d'observer avec précision les dimensions et d'assurer une haute qualité de la surface des pièces. C'est ainsi que sont coulés des aubes de turbine et des outils performants, des prothèses dentaires et des bijoux, ainsi que des sculptures de configuration complexe. L'essence de la coulée à la cire perdue est que le moule de coulée est monobloc, le modèle de matériaux à bas point de fusion n'est pas retiré pendant le moulage, mais est fondu. Cela garantit le respect scrupuleux des dimensions et du relief. Le métal est coulé dans la cavité restant du modèle. Une fois le refroidissement terminé, le moule est détruit et le produit est retiré. Lors de la coulée de grandes séries, le coût du produit est réduit.
Avantages de la méthode
Le principal avantage du moulage de précision est la précision du transfert du moule et la faible rugosité de surface. De plus, d'autres avantages sont disponibles:
- Production de pièces en alliage légèrement usinées disponibles.
- Réduit le besoin d'usinage supplémentaire.
- Les produits sont coulés qui, autrement, devraient être fabriqués en plusieurs parties et assemblés.
- Avec les grandes séries, une réduction de l'intensité de travail spécifique (par produit) et de son coût est obtenue.
- Possibilité de mécanisation et d'automatisation partielle des opérations préparatoires de la coulée elle-même.
Ces avantages font de cette méthode l'une des plus populaires et des plus utilisées dans la métallurgie d'aujourd'hui, en particulier en combinaison avec les méthodes modernes de coulée progressive.
Inconvénients du moulage de précision
Les avantages incontestables de la méthode, semble-t-il, auraient dû assurer sa domination parmi les autres méthodes. Cependant, malgré la popularité de la méthode de moulage de précision, des inconvénients ont empêché son adoption généralisée. Le principal inconvénient est la complexité du processus en plusieurs étapes. Cela nécessite un équipement technologique assez complexe et coûteux pour les étapes préparatoires. Pour les produits simples fabriqués en petites quantités, cette méthode a un coût plus élevé.
Pour l'application rentable du moulage de précision, les avantages et les inconvénients de la méthode sont comparés, la décision surson choix se fait sur la base d'une appréciation du rapport qualité/prix. Par conséquent, il est principalement utilisé pour les produits les plus critiques et les plus coûteux, difficiles à obtenir autrement, tels que les aubes de turbine, les sculptures, les outils à grande vitesse, etc. Un autre domaine d'application est celui des pièces moulées à grande échelle, en dont l'effet d'échelle permet d'obtenir une réduction significative des coûts.
Technologie
La technologie de moulage de précision est un processus de fabrication en plusieurs étapes qui demande relativement beaucoup de main-d'œuvre. Lors de la première étape, un modèle maître est réalisé, il deviendra la norme pour la fabrication de modèles de travail après avoir traversé toutes les étapes du produit final. Pour la production d'un modèle maître, des compositions de modèles spéciales et traditionnelles - gypse ou bois - sont utilisées. Le matériau du maître-modèle doit combiner résistance et facilité de traitement.
En outre, la technologie de moulage à la cire perdue permet la création d'un moule dans lequel tous les modèles de travail seront coulés. Les moules sont en gypse, caoutchouc, silicone, moins souvent en métal. Structurellement, il doit nécessairement être amovible et conçu pour une utilisation répétée. Le moule est rempli d'une composition de modèle, après durcissement, il est démonté et le modèle de travail suivant est retiré.
Lors de la production de pièces uniques ou de petites séries, les étapes de création d'une maquette et d'un moule sont ignorées, et une maquette (ou plusieurs) est réalisée en moulant le matériau manuellement.
La prochaine étape du processus de moulage de précision estfabrication autour du tracé (ou bloc de tracés) du moule de fonderie. Ces matrices sont structurellement déjà inséparables et jetables, ce qui permet de respecter scrupuleusement les dimensions et la rugosité du produit. Dans l'industrie moderne, deux types de moules sont utilisés - les moules traditionnels en sable-argile pour la coulée dans le sol et les moules en coquille - pour la production de pièces précises et coûteuses.
Une fois le moule terminé, le modèle en est fondu en chauffant ou en soufflant avec de la vapeur surchauffée. Les formes de coque sont en outre renforcées en chauffant jusqu'à 1000 ˚С.
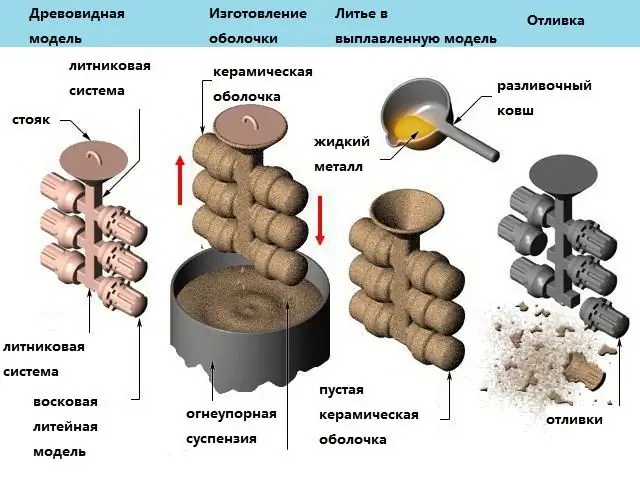
L'étape finale du processus comprend la coulée proprement dite du produit, son refroidissement dans des conditions naturelles ou par une méthode spéciale dans un thermostat, la destruction du moule et le nettoyage du produit. La méthode permet d'obtenir des moulages de haute qualité pesant de plusieurs grammes à des dizaines de kilogrammes.
Les gammes de modèles
Le matériau pour la production de la mise en page doit avoir certaines propriétés. Il devrait avoir des propriétés comme:
- Plasticité en phase solide. Il est nécessaire de répéter avec précision la forme du futur produit et de la corriger si nécessaire.
- Force. Le modèle doit résister sans déformation au processus de formation d'une forme autour de lui.
- Fusible. Le rendu d'un modèle ne devrait pas nécessiter beaucoup de temps et d'énergie.
- Fluidité fondue. La composition doit pénétrer facilement dans tous les recoins et détails du relief, en répétant exactement les contours du futur détail.
- Économie. Particulièrement important pour la production en grande série.
Pour les compositions modèles, un mélange de stéarine et de paraffine est généralement utilisé. Ces matériaux se complètent avec succès, compensant le point de fusion insuffisant de la paraffine et la viscosité excessive de la stéarine.
Les compositions à base de cire de lignite ne sont pas moins populaires dans l'industrie. Ses principales propriétés sont la résistance à l'humidité, la résistance et la capacité de former des revêtements très lisses, ce qui est particulièrement précieux pour la modélisation de produits.
Des composés constitués d'un mélange de cire de lignite, de paraffine et de stéarine sont également utilisés.
Fabrication de moules
Pour la production de produits uniques, une mise en page est préparée en découpant un morceau de matériau de modèle manuellement ou selon des modèles. Des modèles en forme de corps de révolution sont également réalisés sur des tours. Récemment, la méthode d'impression 3D de modèles s'est de plus en plus répandue. Il convient à la fois aux mises en page simples et aux petites séries.
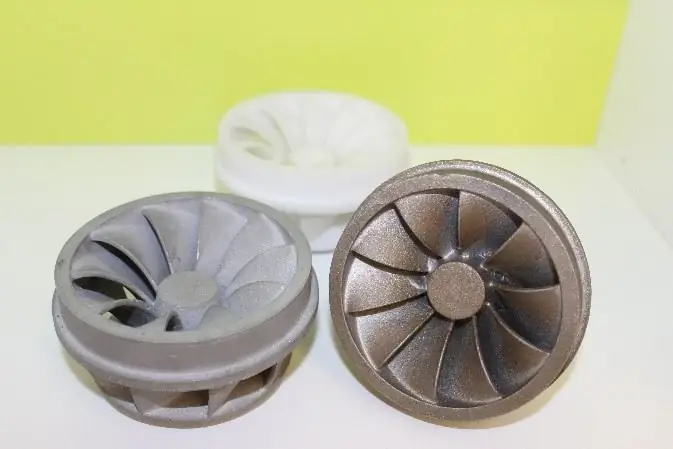
Le coût d'une imprimante 3D industrielle moderne est encore élevé, mais en raison de la facilité de reconfiguration d'un produit à l'autre, elle peut devenir un outil de modélisme efficace en cas de commandes hétérogènes en petites séries.
Afin de réaliser un grand nombre de tracés identiques, une matrice est en plâtre, caoutchouc, silicone ou métal. Les mises en page de travail sont produites, à leur tour, par moulage dans une matrice. De par sa conception, le moule doit être pliable pour assurer la possibilité de fabriquer un nombre donné de modèles. Le matériau sélectionné doit également offrir une telle opportunité, par conséquent, des exigences telles que la résistance, la densité, la faible rugosité et l'inertie chimique par rapport à la disposition lui sont imposées. La substance du moule doit également avoir une adhérence minimale à la maquette pour garantir que les maquettes finies peuvent être facilement retirées et que les dimensions peuvent être respectées. Une propriété importante du moule est sa solidité et sa résistance à l'usure, en particulier pour les grandes séries.
Fabriquer des modèles et des blocs
Une méthode largement utilisée pour fabriquer des modèles d'investissement consiste à les couler sous basse pression dans des moules. L'injection du mélange liquide s'effectue à la fois manuellement, à l'aide de seringues à piston, et de surpresseurs mécaniques, hydrauliques ou pneumatiques. Dans le cas de l'utilisation de cire de lignite, il est nécessaire de chauffer les canalisations d'alimentation en composition du fait de sa viscosité élevée. Les modèles en polystyrène expansé sont fabriqués par extrusion sur des machines de moulage automatisées.
Pour augmenter l'efficacité économique et réduire l'intensité de la main-d'œuvre dans le cas de la production en série de petites pièces moulées, leurs dispositions sont combinées en blocs. Les systèmes de porte sont formés au-dessus des blocs en attachant des dispositions individuelles aux carottes à l'aide d'un fer à souder à la main. Dans le cas de pièces uniques ou de petites séries, les modèles sont fabriqués à la main.
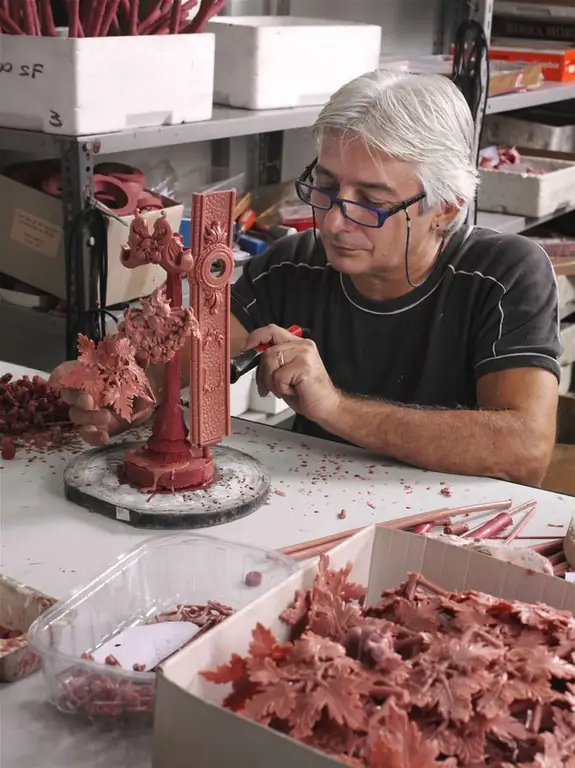
Lors de la formation de systèmes de porte, il est nécessaire d'assurer un écoulement non turbulent de la masse fondue, un remplissage uniforme de tous les éléments de la matrice. Lorsque vous remplissez un formulaire à partir de PGS, vous devez également surveiller le remplissage uniforme de tousouvertures entre les carottes et prévenir les dommages.
Fabriquer un moule
Dans la méthode de moulage à la cire perdue à l'étude, il existe deux principaux types de moules:
- Mélanges sable-argile (SGM).
- Coquille.
Les moules de coulée en cire fluée sont principalement utilisés dans la production de petites séries de produits qui ne nécessitent pas une très grande précision. Le processus de leur fabrication est assez laborieux et nécessite des compétences élevées et souvent uniques des modeleurs et des mouleurs. La mécanisation partielle ne se prête qu'à certaines opérations, comme la préparation et le remplissage du sable de moulage, son bourrage.
Les moules coquilles, quant à eux, sont utilisés pour produire des pièces qui nécessitent une précision de fabrication particulière. Le processus de leur fabrication est plus complexe et long, mais il se prête mieux à la mécanisation.
Coupe au sol
Il s'agit de la première méthode de traitement des métaux maîtrisée par l'humanité. Il a été maîtrisé par nos ancêtres simultanément avec le début de l'utilisation de produits métalliques comme armes, outils ou ustensiles, c'est-à-dire il y a environ 5 000 ans. Le métal en fusion est versé dans une matrice préparée à partir d'un mélange de sable et d'argile. Les premiers lieux de traitement des métaux sont apparus là où des gisements de métaux sous forme de pépites et de placers se trouvaient à proximité. Un exemple typique est l'usine de Kasli dans l'Oural, mondialement connue pour son moulage de dentelle de fer.
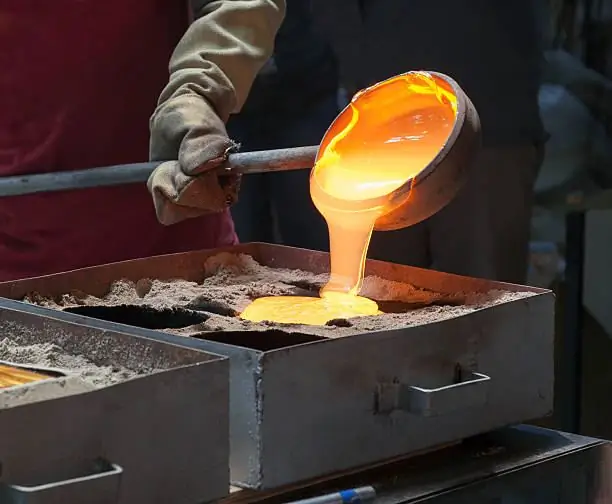
La méthode de moulage de précision est utilisée pour la fabrication de produits métalliques - à la fois ferreux etcoloré. Et seulement pour les métaux qui présentent une tendance accrue à réagir en phase liquide (comme le titane), il est nécessaire de fabriquer des matrices à partir d'autres compositions.
Le processus de production de moulage dans PGS comprend les phases suivantes:
- modélisme;
- préparation du flacon;
- remplissage et compactage du mélange dans le ballon;
- fonderie de métal;
- retirer et nettoyer le moulage.
Formulaire d'ASG - à usage unique. Pour obtenir le produit fini, il faudra le casser. Dans le même temps, la majeure partie du mélange est disponible pour être réutilisée.
Des compositions à prédominance de sables de quartz de différentes granulométries et d'argiles plastiques, dont la teneur varie de 3 à 45 %, sont utilisées comme matériaux pour l'ASG. Ainsi, par exemple, les moulages d'art sont produits à l'aide d'un mélange contenant 10 à 20 % d'argile. Pour les moulages particulièrement volumineux, la teneur en argile est ajustée à 25 %.
Deux sous-types sont utilisés:
- Mélanges de parement. Ils sont situés sur la surface intérieure du moule et interagissent avec le métal en fusion. Ils doivent être résistants à la chaleur, capables de ne pas être détruits par les différences de température et les contraintes qui en résultent. Ces mélanges ont un grain fin pour transmettre avec soin les détails de la surface. La capacité du mélange à laisser passer le gaz est également très importante.
- Mélanges de remplissage. Ils sont utilisés pour le remblai entre la couche de parement et les parois du ballon. Ils doivent supporter le poids du métal coulé, conserver la forme du produit et contribuer à l'élimination rapide et complète des gaz. Produit à partir de qualités de sable moins chères,réutilisable.
Si les gaz de coulée ne s'échappent pas à travers les masses de sable de moulage, mais à travers le système de gating, des défauts se produisent dans la coulée, conduisant au mariage.
La technologie traditionnelle de coulée dans le sol est illustrée en détail dans le film "Andrei Rublev" d'A. Tarkovsky. Dans la nouvelle "La Cloche", le jeune homme Boriska, fils d'un maître décédé, dirige un artel de fonderie et fond une cloche d'église.
Coquillage
La méthode de moulage à la cire perdue dans des moules carapaces se caractérise par le meilleur transfert des dimensions du produit et une faible rugosité de surface. Le modèle est fabriqué à partir de composés fusibles, tels que la cire de charbon brun. Les fonderies utilisent également largement la composition de paraffine-stéarine dans des proportions égales. Dans le cas de moulages de grandes tailles, des sels sont inclus dans le matériau du modèle pour protéger le modèle de la déformation. En plongeant dans la solution, le modèle est recouvert de 6 à 10 couches avec une suspension à haute température.
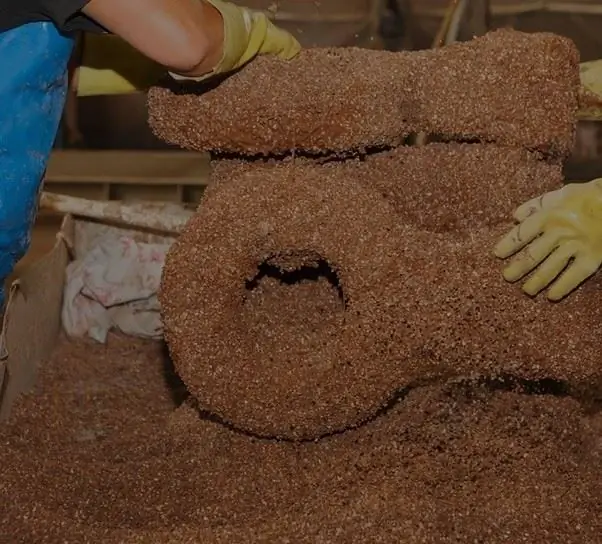
Les silicates hydrolysés agissent comme liant, l'électrocorindon ou les cristaux de quartz sont pris comme saupoudrage résistant à la chaleur. Les matériaux de moulage en coquille se caractérisent par une résistance élevée, une faible hygroscopicité et une excellente perméabilité aux gaz.
La mise en page est séchée dans une atmosphère d'ammoniac gazeux. A l'étape suivante, le moule est chauffé à 120 ˚C pour retirer le modèle en paraffine. Les restes du mélange sont éliminés avec de la vapeur surchauffée sous haute pression. Ensuite, le moule est calciné à des températures allant jusqu'à 1000 ˚С, ce qui conduit à sa fixation finale et à l'élimination des substances,qui peuvent être libérés sous forme de gaz pendant le processus de coulée.
La coquille est placée dans une sorte de flacon recouvert de grenaille d'acier. Cela aide à maintenir la configuration lors du remplissage du moule avec de la matière fondue et améliore en même temps les conditions de refroidissement de la pièce moulée. La masse fondue est coulée dans des moules chauffés à 1000 ˚С. Après avoir refroidi le produit selon un programme spécial dans un thermostat, le moule est détruit, le moulage est retiré et nettoyé.
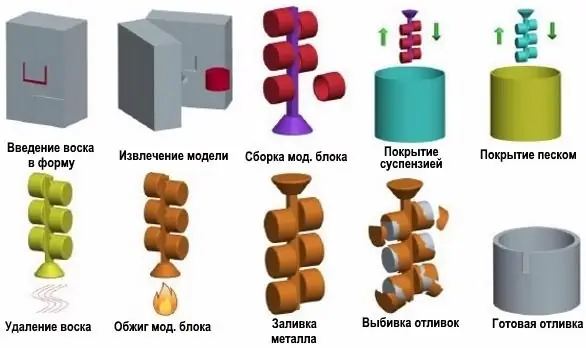
Le principal avantage de cette méthode de coulée est une grande précision dimensionnelle et une faible rugosité de surface.
Avantages supplémentaires de la méthode:
- Pièces coulées à partir d'alliages difficiles à usiner.
- Créer des objets qui autrement auraient dû être lancés au coup par coup, puis remontés.
Les inconvénients de cette méthode de moulage de précision sont une faible utilisation du métal et une intensité de travail accrue.
Moulage de précision
Moulage de précision - c'est le nom donné à la fois à la technologie et au produit final lui-même. La grande précision de la coulée est assurée par le fait que lors de la préparation du moule, il n'est pas nécessaire d'en extraire le modèle du produit. Lors de l'utilisation de la méthode traditionnelle, la production d'une matrice de coulée est un processus en plusieurs étapes complexe et très long. Cela est particulièrement vrai dans le cas de pièces coulées de configuration complexe, avec des évidements, des dépressions et des cavités internes.
Par exemple, lors de la coulée d'un vase en fonte ou en cuivre avec une courbure de surface variable, vous devez utiliser beaucoup d'astuces. Oui, d'abordla moitié inférieure du flacon est bourrée, puis le modèle est retiré, retourné et la moitié supérieure est enfoncée. Le modèle doit être réalisé en composite, les anses du vase sont constituées de deux éléments, elles sont tirées à travers la cavité du modèle en deux étapes - d'abord l'élément inférieur, puis le supérieur. Tous ces nombreux tournages et entraînements ne peuvent avoir un effet positif sur l'intégrité de la surface du moule et, en définitive, sur la précision du maintien des dimensions de la pièce moulée et la qualité de sa surface. De plus, il reste le problème de faire correspondre avec précision les parties des flacons et de les attacher solidement les unes aux autres.
La production de moulage de précision est dépourvue de ces défauts, elle ne nécessite pas de modélisateurs aussi qualifiés et réduit considérablement l'intensité de main-d'œuvre des opérations de préfabrication. Ceci est particulièrement prononcé avec de grandes séries de pièces moulées.
La méthode permet d'atteindre la classe de précision 2-5 selon GOST 26645-85. Cela permet de couler des produits de haute précision tels que des aubes de turbine, des outils de coupe, y compris des fraises et des perceuses hautes performances, des supports critiques à forte charge, de petites pièces de véhicules à forte charge, des machines-outils et d'autres mécanismes complexes.
La précision dimensionnelle élevée et la classe de surface élevée minimisent le besoin d'usinage supplémentaire de la pièce moulée, ce qui permet d'économiser du métal et de réduire les coûts de production.
Équipement
L'équipement de moulage de précision requis est varié et complexe. Les entreprises les combinent en un complexe unique et bien coordonné,organisé comme un site, un atelier ou une production séparée.
La composition du complexe dépend de l'échelle de production, de la taille, de la configuration et de la circulation des pièces moulées.
Ainsi, dans la production de prothèses dentaires et de bijoux, l'équipement comprendra:
- table modèle;
- four à moufle avec thermostat;
- un ensemble de scalpels et de spatules pour corriger la forme du modèle;
- formant la planche;
- flacon;
- réservoirs pour le stockage et la préparation du sable de moulage;
- ensemble d'outils de pilonnage de sable;
- creuset pour fondre le métal;
- forceps;
- marteau pour casser le moule.
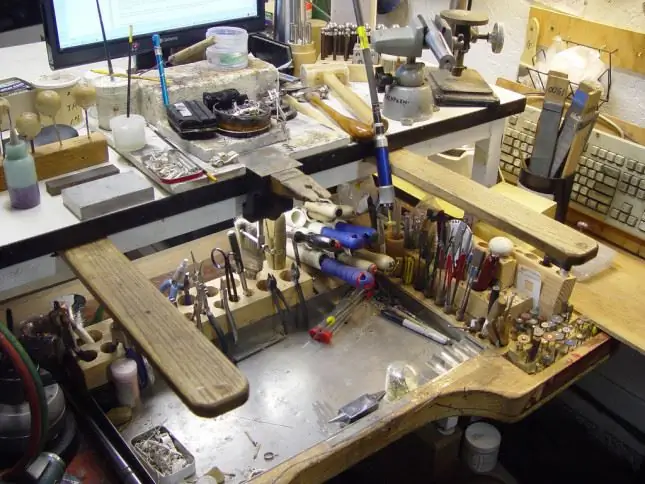
Ce complexe de production peut facilement tenir sur une table et dans une armoire. S'il est prévu de produire en masse, par exemple, des pièces moulées en aluminium - des pièces d'un appareil, un équipement sera alors nécessaire pour:
- façonner et couler des moules en céramique;
- formulaires de séchage;
- faire fondre le matériau du modèle et appliquer une couche résistante à la chaleur;
- nettoyage des moulages du matériau de moulage.
Et enfin, l'équipement proprement dit du complexe de fonderie, conçu pour obtenir une fonte et la couler dans un moule. Il peut s'agir d'un équipement de coulée:
- sous basse pression;
- centrifuge;
- de la manière habituelle de la gravité.
Les machines de moulage par injection et de coulée centrifuge sont des machines hautement mécanisées et automatiséescomplexe de production, isolé de l'ambiance de la boutique. Ils minimisent le travail manuel et l'exposition humaine à des conditions nocives. Les chambres scellées dans lesquelles se trouvent les complexes permettent une capture et une purification complètes des gaz d'échappement, ce qui augmente considérablement le respect de l'environnement de l'entreprise.
La fonte à la cire perdue a un potentiel de développement assez élevé, surtout lorsqu'elle est associée à des techniques avancées de fabrication de moules et de coulage.
Conseillé:
Bois traité thermiquement : principales caractéristiques, technologie de production, avantages et inconvénients

Presque chacun d'entre nous est tombé sur un concept tel que le bois traité thermiquement. Cependant, peu ont réfléchi à ce que cela signifie vraiment. Pendant ce temps, ce matériau peut être considéré comme innovant. En raison de la température élevée - de +150 °C à +250 °C - le matériau est solide et durable
Gravure sur plexiglas : avantages et inconvénients, technologie, équipement
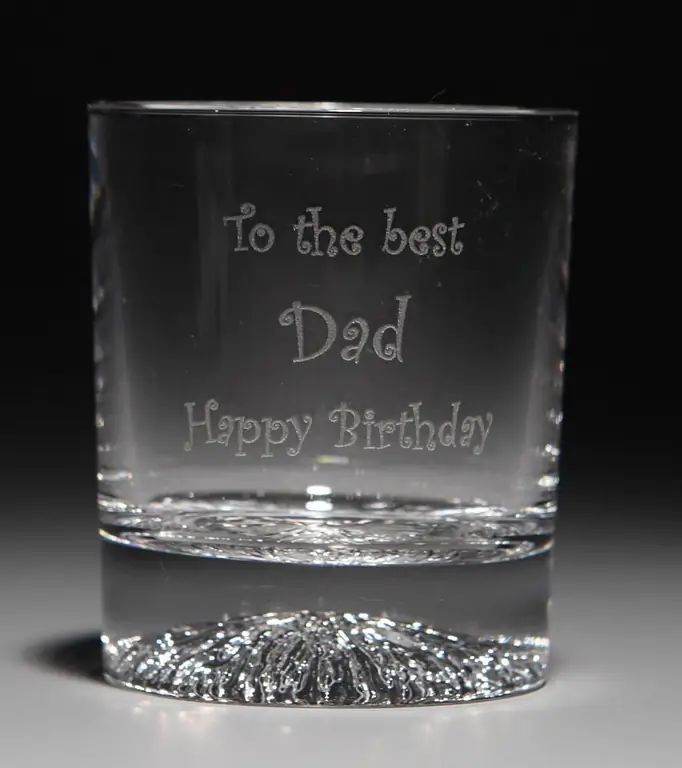
La gravure sur plexiglas est considérée comme un métier de peintre. Une figurine souvenir, des vitraux ou une table en verre, décorés de dessins exquis, incarnent un goût artistique délicat. Les technologies de décapage et de sablage appartiennent au passé. Aujourd'hui, à l'aide d'une machine laser, chacun peut créer un motif très détaillé
La typographie c'est La technologie d'impression typographique, les stades modernes de développement, l'équipement nécessaire, les avantages et les inconvénients de ce type d'impre
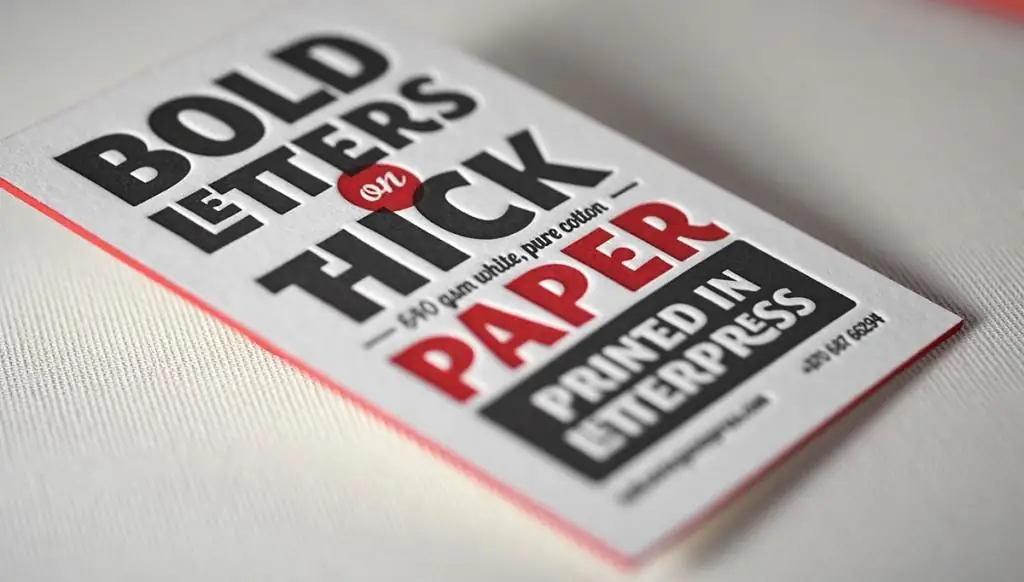
La typographie est l'une des méthodes typiques d'application d'informations à l'aide d'une matrice en relief. Les éléments qui dépassent sont recouverts de peinture sous forme de pâte, puis pressés contre le papier. Ainsi, divers périodiques de masse, ouvrages de référence, livres et journaux sont reproduits
Traitement par ultrasons : technologie, avantages et inconvénients
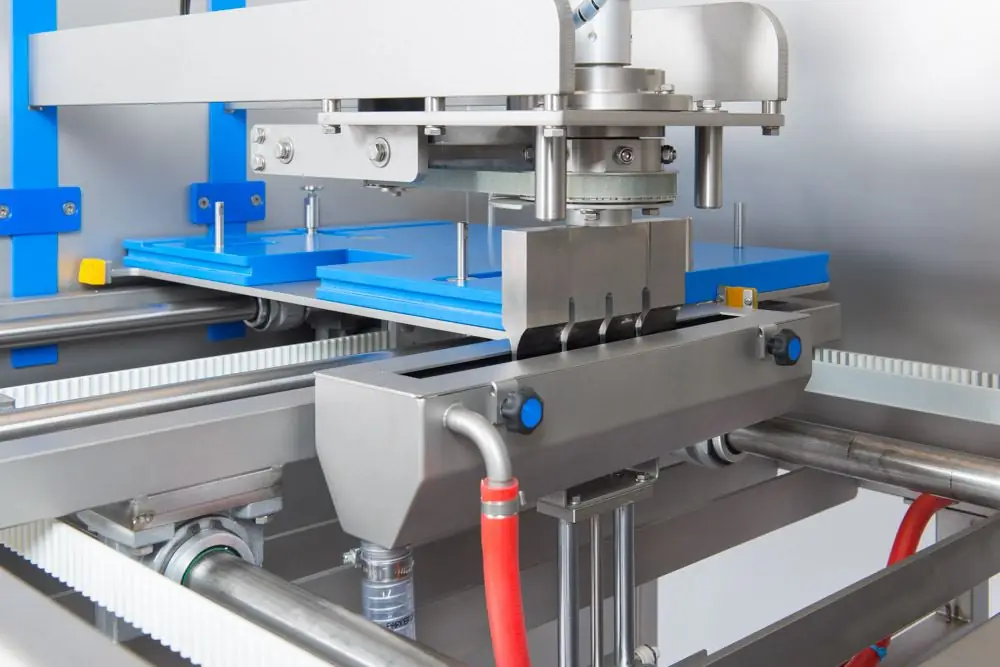
L'industrie métallurgique à ce stade de développement est capable de résoudre les tâches complexes de coupe et de perçage de pièces de différents degrés de dureté. Cela est devenu possible grâce au développement de manières fondamentalement nouvelles d'influencer le matériau, y compris un large groupe de méthodes électromécaniques. L'une des technologies les plus efficaces de ce type est le traitement par ultrasons (UZO), basé sur les principes du rayonnement électroacoustique
Avantages et inconvénients du polyester : description du matériau, avantages de l'application, avis
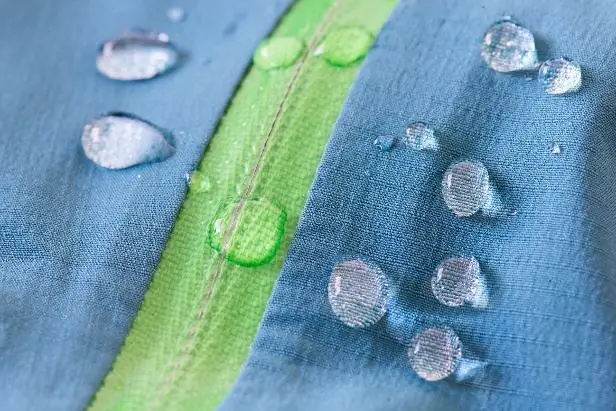
Le polyester peut être trouvé dans la composition de presque tous les articles présents dans la garde-robe de chaque personne. Non seulement des vêtements en sont fabriqués, mais aussi des chaussures, des couvertures, des sous-vêtements thermiques, des tapis. Quelles sont les caractéristiques de chaque type de produit en polyester. Les avantages et les inconvénients de ces produits sont discutés dans notre article