2025 Auteur: Howard Calhoun | [email protected]. Dernière modifié: 2025-01-24 13:16
En raison de sa légèreté, de sa ductilité et de sa résistance à la corrosion, l'aluminium est devenu un matériau indispensable dans de nombreuses industries. L'aluminium aviation est un groupe d'alliages caractérisés par une résistance accrue avec l'inclusion de magnésium, de silicium, de cuivre et de manganèse. Une résistance supplémentaire est donnée à l'alliage à l'aide de ce qu'on appelle. "effet de vieillissement" - une méthode spéciale de durcissement sous l'influence d'un environnement atmosphérique agressif pendant une longue période. L'alliage a été inventé au début du 20ème siècle, appelé duralumin, maintenant également connu sous le nom de "avial".
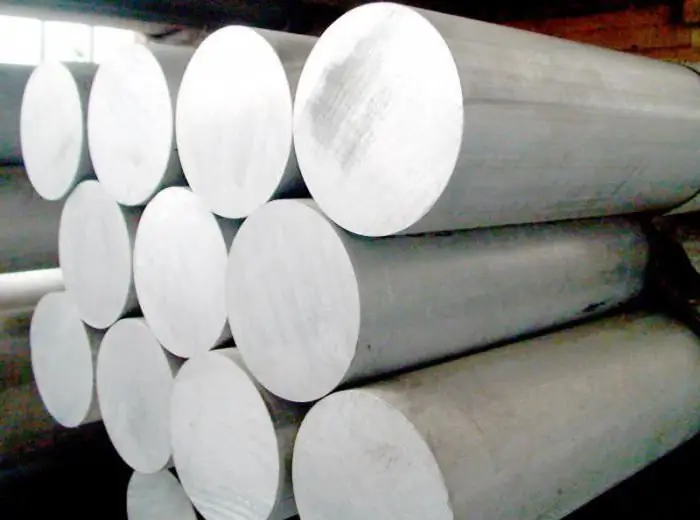
Définition. Excursion historique
Le début de l'histoire des alliages d'aluminium pour l'aviation est considéré comme 1909. L'ingénieur métallurgiste allemand Alfred Wilm a établi expérimentalement que si un alliage d'aluminium avec une légère addition de cuivre, de manganèse et de magnésium après trempe à une température de 500 ° C et refroidissement rapide est maintenu à une température de 20-25 degrés pendant 4-5 jours, il devient progressivement plus dur et plus résistant sans perdre de ductilité. La procédure s'appelait "vieillissement" ou "maturation". Au cours d'un tel durcissement, les atomes de cuivre remplissentnombreuses petites zones aux joints de grains. Le diamètre de l'atome de cuivre est plus petit que celui de l'aluminium, par conséquent, une contrainte de compression apparaît, à la suite de quoi la résistance du matériau augmente.
Pour la première fois, l'alliage a été maîtrisé dans les usines allemandes Dürener Metallwerken et a reçu la marque Dural, d'où le nom "duralumin". Par la suite, les métallurgistes américains R. Archer et V. Jafris ont amélioré la composition en modifiant le pourcentage, principalement de magnésium. Le nouvel alliage a été nommé 2024, qui est encore largement utilisé dans diverses modifications, et toute la famille d'alliages s'appelle Avial. Cet alliage a reçu le nom d'"aluminium aéronautique" presque immédiatement après sa découverte, car il a complètement remplacé le bois et le métal dans les structures d'avions.
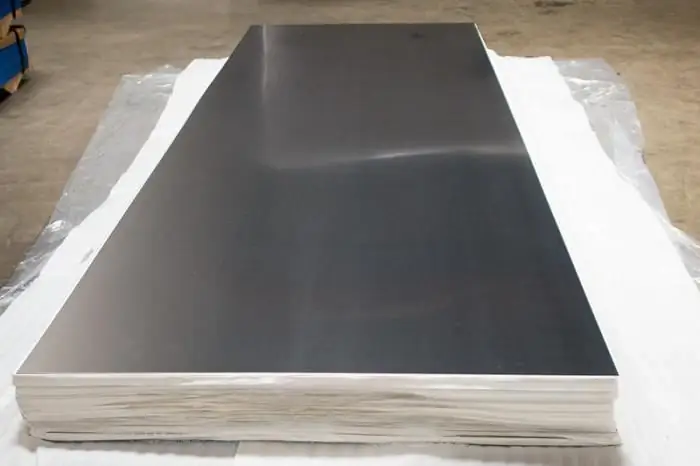
Principaux types et caractéristiques
Il existe trois groupes principaux:
- Familles aluminium-manganèse (Al-Mn) et aluminium-magnésium (Al-Mg). La principale caractéristique est une résistance élevée à la corrosion, à peine inférieure à l'aluminium pur. De tels alliages se prêtent bien au brasage et au soudage, mais sont mal coupés. Non durci par traitement thermique.
- Alliages résistants à la corrosion du système aluminium-magnésium-silicium (Al-Mg-Si). Ils sont durcis par traitement thermique, à savoir un durcissement à une température de 520°C, suivi d'un refroidissement rapide à l'eau et d'un vieillissement naturel d'environ 10 jours. Une caractéristique distinctive de ce groupe de matériaux est leur haute résistance à la corrosion pendant le fonctionnement dans des conditions normales et sous contrainte.
- Alliages structuraux aluminium-cuivre-magnésium (Al-Cu-Mg). Leur base est l'aluminium allié au cuivre, au manganèse et au magnésium. En modifiant les proportions des éléments d'alliage, on obtient de l'aluminium de qualité aéronautique dont les caractéristiques peuvent différer.
Les matériaux du dernier groupe ont de bonnes propriétés mécaniques, mais sont plus sensibles à la corrosion que les première et deuxième familles d'alliages. Le degré de sensibilité à la corrosion dépend du type de traitement de surface, qui doit encore être protégé par une peinture ou une anodisation. La résistance à la corrosion est partiellement augmentée par l'introduction de manganèse dans la composition de l'alliage.
En plus des trois principaux types d'alliages, il existe également des alliages de forgeage, des alliages de construction résistants à la chaleur et à haute résistance, ainsi que d'autres alliages qui possèdent les propriétés nécessaires à une application particulière.
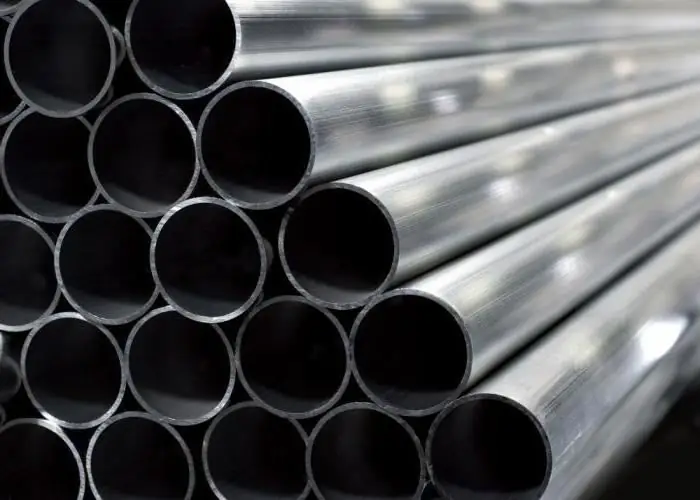
Marquage des alliages aéronautiques
Dans les normes internationales, le premier chiffre du marquage aluminium aviation indique les principaux éléments d'alliage de l'alliage:
- 1000 - aluminium pur.
- 2000 - duralumins, alliages alliés au cuivre. Dans une certaine période - l'alliage aérospatial le plus courant. De plus en plus remplacés par les alliages de la série 7000 en raison de leur forte sensibilité à la fissuration par corrosion sous contrainte.
- 3000 - élément d'alliage - manganèse.
- 4000 - élément d'alliage - silicium. Les alliages sont également connus sous le nom de silumins.
- 5000 - élément d'alliage - magnésium.
- 6000 sont les alliages les plus ductiles. Les éléments d'alliage sont le magnésium et le silicium. Peut être durci à la chaleur pour augmenter la résistance, mais celale paramètre est inférieur aux séries 2000 et 7000.
- 7000 - alliages durcis thermiquement, l'aluminium aéronautique le plus durable. Les principaux éléments d'alliage sont le zinc et le magnésium.
Le deuxième chiffre du marquage est le numéro de série de la modification de l'alliage d'aluminium après celui d'origine - le chiffre "0". Les deux derniers chiffres sont le numéro de l'alliage lui-même, des informations sur sa pureté par les impuretés. Si l'alliage est expérimenté, un cinquième "X" est ajouté au marquage.
Aujourd'hui, les nuances d'aluminium aéronautique les plus courantes: 1100, 2014, 2017, 3003, 2024, 2219, 2025, 5052, 5056. Les caractéristiques distinctives de ces alliages sont: légèreté, ductilité, bonne résistance, résistance au frottement, la corrosion et les charges élevées. Dans l'industrie aéronautique, les alliages les plus utilisés sont l'aluminium aéronautique 6061 et 7075.
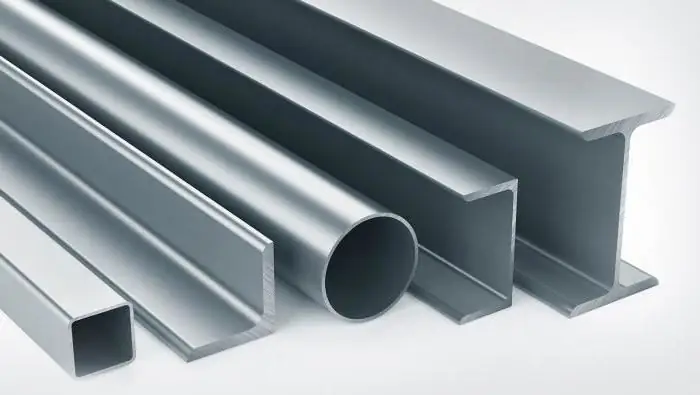
Composition
Les principaux éléments d'alliage de l'aluminium aéronautique sont: le cuivre, le magnésium, le silicium, le manganèse, le zinc. Le pourcentage de ces éléments en poids dans l'alliage est déterminé par des caractéristiques telles que la résistance, la flexibilité, la résistance aux contraintes mécaniques, etc. La base de l'alliage est l'aluminium, les principaux éléments d'alliage sont le cuivre (2,2-5,2% en poids), magnésium (0. 2-2.7%) et manganèse (0.2-1%).
Une famille d'alliages d'aviation d'aluminium avec du silicium (4-13% en poids) avec une faible teneur en autres éléments d'alliage - cuivre, manganèse, magnésium, zinc, titane, béryllium. Utilisé pour réaliser des pièces complexes, également appelées silumin ou alliage d'aluminium coulé. famille des alliages aluminium-magnésium(1-13 % de masse) avec d'autres éléments ont une ductilité et une résistance à la corrosion élevées.
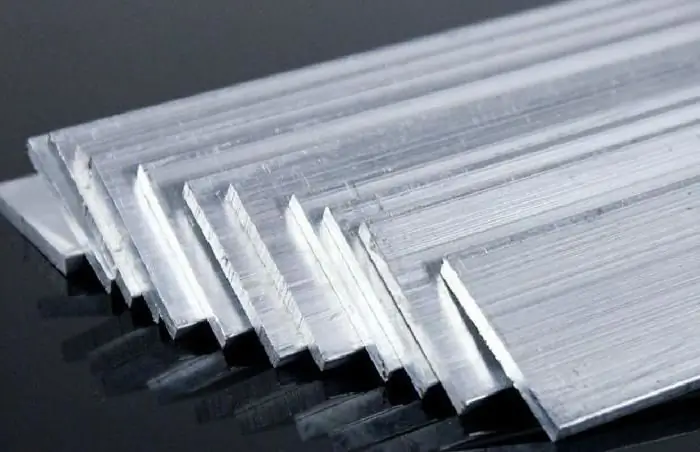
Le rôle du cuivre dans l'aluminium aéronautique
La présence de cuivre dans la composition de l'alliage aéronautique contribue à son durcissement, mais a en même temps un effet néfaste sur sa résistance à la corrosion. En tombant aux joints de grains pendant le processus de trempe, le cuivre rend l'alliage sensible aux piqûres, à la corrosion sous contrainte et à la corrosion intergranulaire. Les zones riches en cuivre sont plus galvaniquement cathodiques que la matrice en aluminium environnante et sont donc plus vulnérables à la corrosion galvanique. Une augmentation de la teneur en cuivre dans la masse de l'alliage jusqu'à 12% augmente les propriétés de résistance en raison du renforcement de la dispersion au cours du vieillissement. Avec une teneur en cuivre supérieure à 12 %, l'alliage devient cassant.
Domaines d'application
Les alliages d'aluminium sont les métaux les plus recherchés à la vente. Le poids léger de l'aluminium de qualité aéronautique et sa résistance font de cet alliage un bon choix pour de nombreuses industries, des avions aux articles ménagers (téléphones portables, écouteurs, lampes de poche). Les alliages d'aluminium sont utilisés dans la construction navale, l'automobile, la construction, le transport ferroviaire et l'industrie nucléaire.
Les alliages à teneur modérée en cuivre sont largement demandés (2014, 2024 etc.). Les profilés fabriqués à partir de ces alliages ont une résistance élevée à la corrosion, une bonne usinabilité et une soudabilité par points. Ils sont utilisés pour fabriquer des structures critiques pour les avions, les véhicules lourds, les équipements militaires.
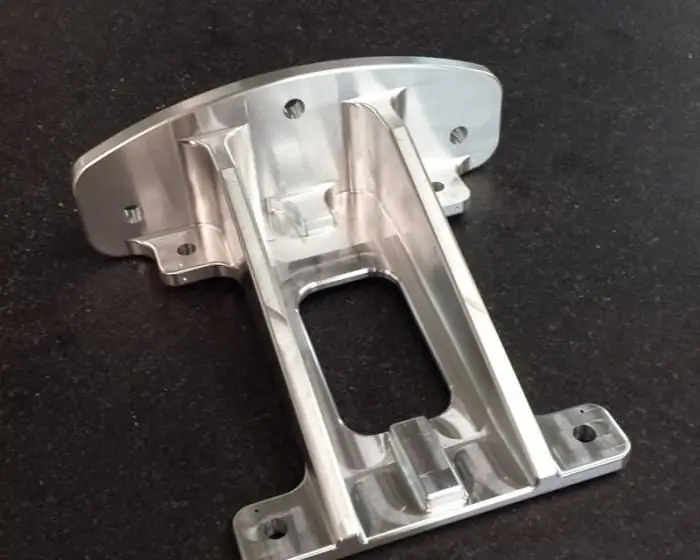
Caractéristiques de connexion en aluminium de qualité aéronautique
Le soudage des alliages aéronautiques est effectué exclusivement dans un environnement protecteur de gaz inertes. Les gaz préférés sont: l'hélium, l'argon ou un mélange de ceux-ci. L'hélium a une conductivité thermique plus élevée. Cela détermine des indicateurs de température plus favorables de l'environnement de soudage, ce qui permet de connecter assez confortablement des éléments structurels à paroi épaisse. L'utilisation d'un mélange de gaz protecteurs contribue à une élimination plus complète des gaz. Dans ce cas, la probabilité de formation de pores dans la soudure est considérablement réduite.
Applications aéronautiques
Les alliages d'aluminium pour l'aviation ont été créés à l'origine spécialement pour la construction d'équipements aéronautiques. Les corps d'avions, les pièces de moteur, les châssis, les réservoirs de carburant, les fixations, etc. en sont fabriqués. Des pièces en aluminium d'aviation sont utilisées à l'intérieur de la cabine.
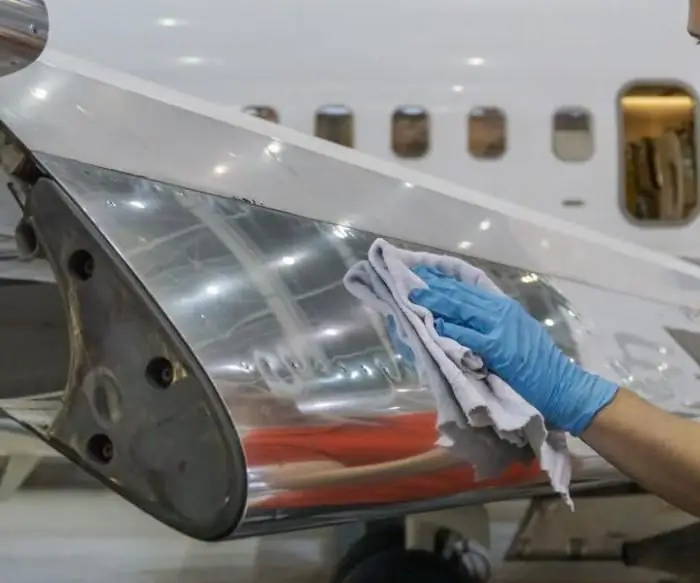
Les alliages d'aluminium de la série 2xxx sont utilisés pour la production de pièces exposées à des températures élevées. Les pièces des unités légèrement chargées, des systèmes de carburant, hydrauliques et d'huile sont en alliages 3xxx, 5xxx et 6xxx. L'alliage 7075 a reçu l'application la plus large dans l'industrie aéronautique. Les éléments en sont fabriqués pour fonctionner sous une charge importante, à basses températures avec une résistance élevée à la corrosion. La base de l'alliage est l'aluminium et les principaux éléments d'alliage sont le magnésium, le zinc et le cuivre. Les profils de puissance des structures d'avions, les éléments de peau en sont fabriqués.
Conseillé:
Ruban auto-adhésif aluminium : propriétés, types, caractéristiques
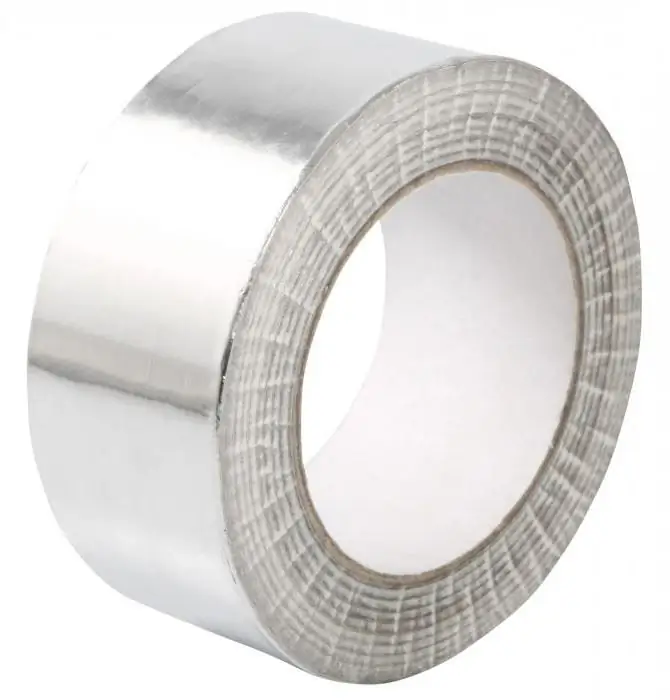
Le ruban auto-adhésif en aluminium est un matériau universel à des fins techniques, qui est utilisé à la fois dans la vie quotidienne et dans la construction
Pilotes de l'aviation civile : formation, caractéristiques du métier et responsabilités
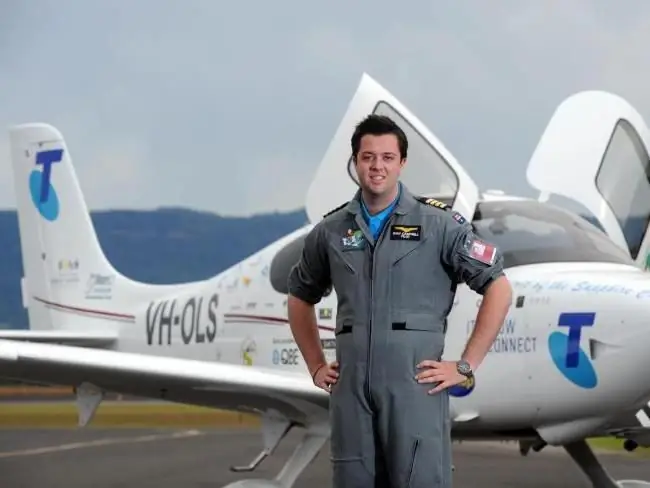
Les pilotes de l'aviation civile sont des spécialistes qui se sont entièrement consacrés à la vie dans le ciel. Ce sont des gens intrépides qui ont défié le destin et traversé de nombreuses épreuves. Par conséquent, toute personne qui rêve d'un tel métier doit être bien consciente que son chemin de vie deviendra tout aussi difficile et épineux
Corrosion de l'aluminium et de ses alliages. Méthodes de lutte et de protection de l'aluminium contre la corrosion
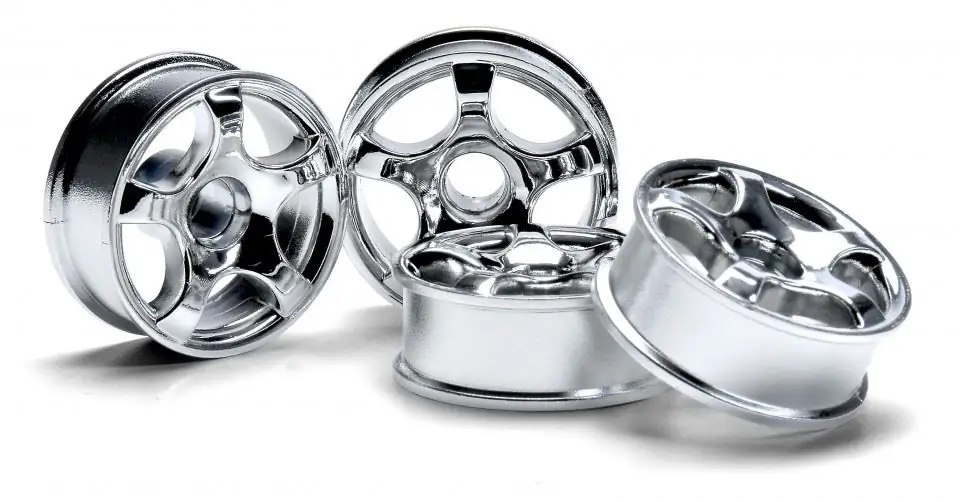
L'aluminium, contrairement au fer et à l'acier, est assez résistant à la corrosion. Ce métal est protégé de la rouille par un film d'oxyde dense formé à sa surface. Cependant, en cas de destruction de ce dernier, l'activité chimique de l'aluminium augmente fortement
Essence aviation : caractéristiques
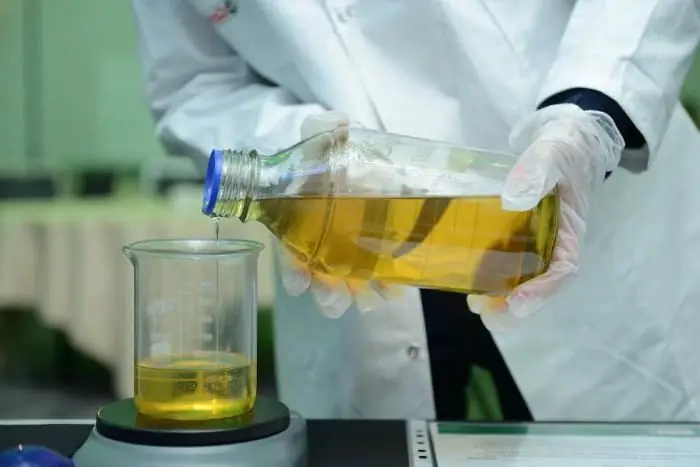
Quelle est la différence entre l'essence aviation et l'essence automobile ? Marques d'essence utilisées dans l'aviation. Spécifications, production de carburant pour avions
Novossibirsk Aviation Plant im. V.P. Chkalova - aperçu, caractéristiques et histoire
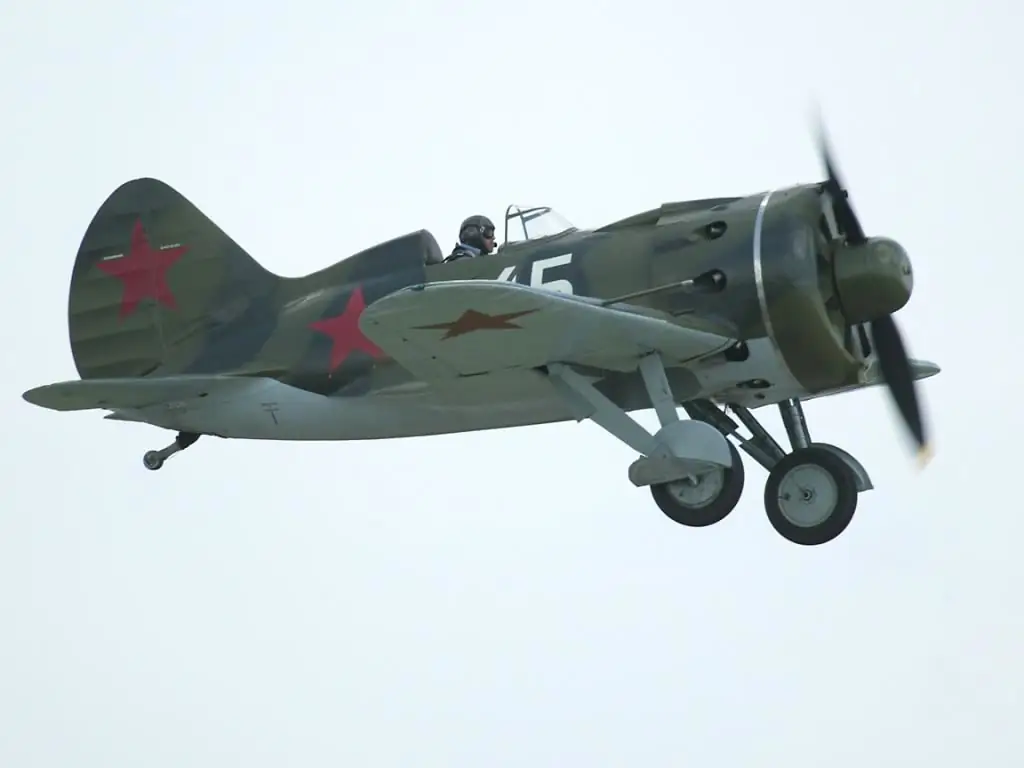
V.P. Chkalova est la fierté de l'industrie aéronautique de la Fédération de Russie. Les avions de l'usine ont montré au monde entier que la Russie est un pays qui développe avec succès la production la plus complexe d'équipements aéronautiques