2025 Auteur: Howard Calhoun | [email protected]. Dernière modifié: 2025-06-01 07:13
La fonte est un alliage fer-carbone dur, résistant à la corrosion, mais cassant, avec une teneur en carbone C allant de 2,14 à 6,67 %. Malgré la présence de défauts caractéristiques, il présente une variété de types, de propriétés et d'applications. La fonte ductile est largement utilisée.
Histoire
Ce matériau est connu depuis le IVe siècle av. e. Ses racines chinoises remontent au VIe siècle. avant JC e. En Europe, la première mention de la production industrielle de l'alliage remonte au 14ème, et en Russie - au 16ème siècle. Mais la technologie de production de fonte ductile a été brevetée en Russie au XIXe siècle. Plus tard développé par A. D. Annosov.
Étant donné que l'utilisation des fontes grises est limitée en raison de leurs faibles propriétés mécaniques et que les aciers sont chers et ont une dureté et une durabilité faibles, la question s'est posée de créer un métal dur fiable, durable, tout en ayant une résistance accrue et une certaine plasticité.
Le forgeage de la fonte n'est pas possible, mais en raison de ses caractéristiques ductiles, elle se prête à certains types de traitement sous pression (par exemple, l'emboutissage).
Production
La voie principale -fonte dans les hauts fourneaux.
Matière première pour le traitement des hauts fourneaux:
- Lot - minerai de fer contenant du métal sous forme d'oxydes de fer.
- Carburant - coke et gaz naturel.
- Oxygène - injecté par des lances spéciales.
- Les fondants sont des formations chimiques à base de manganèse et (ou) de silicium.
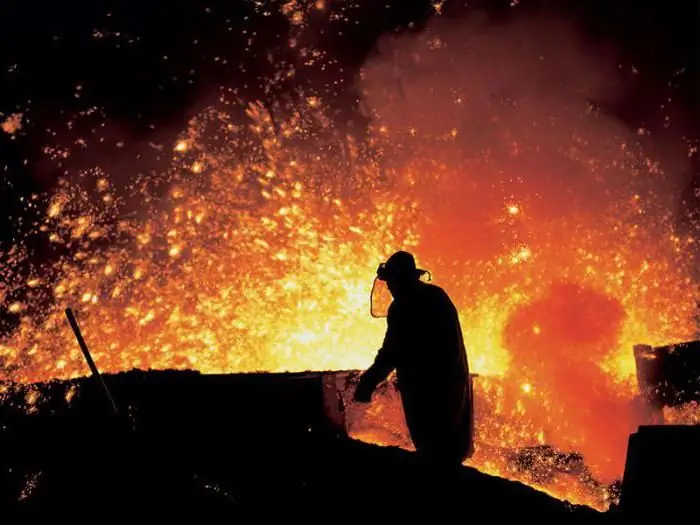
Etapes du haut-fourneau:
- Récupération du fer pur par réactions chimiques du minerai de fer avec de l'oxygène fourni par des lances.
- Combustion de coke et formation d'oxydes de carbone.
- Carburation du fer pur dans les réactions avec le CO et le CO2.
- Saturation de Fe3C avec du manganèse et du silicium, selon les propriétés de sortie requises.
- Égoutter le métal fini dans des moules à travers des trous de coulée en fonte; évacuation des scories par les trous de coulée des scories.
À la fin du cycle de travail, les hauts-fourneaux reçoivent des gaz de fonte, de laitier et de haut-fourneau.
Produits métalliques pour hauts fourneaux
Selon la vitesse de refroidissement, la microstructure, la saturation en carbone et les additifs, il est possible d'obtenir plusieurs types de fonte:
- Acheté (blanc): carbone lié, cémentite primaire. Ils sont utilisés comme matières premières pour la fusion d'autres alliages fer-carbone, le traitement. Jusqu'à 80 % de tous les alliages de haut fourneau produits.
- Fonderie (gris): carbone sous forme de graphite totalement ou partiellement libre, à savoir ses plaques. Utilisé pour la production de pièces de carrosserie à faible responsabilité. Jusqu'à 19 % des pièces coulées de haut fourneau produites.
- Spécial: riche en ferroalliages. 1-2 % du type de production considéré.
La fonte ductile est obtenue par traitement thermique de la fonte.
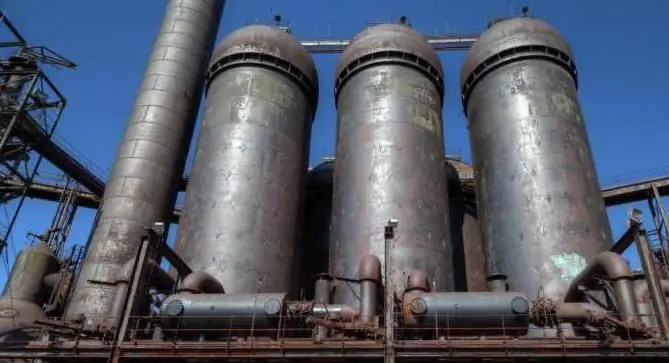
Théorie des structures fer-carbone
Le carbone avec du ferum peut former plusieurs types d'alliages différents selon le type de réseau cristallin, qui est affiché sur l'option de microstructure.
- Pénétration d'une solution solide dans le fer α - ferrite.
- Pénétration de la solution solide dans le fer γ - austénite.
- Formation chimique Fe3C (état lié) - cémentite. Le primaire est formé par refroidissement rapide à partir d'un liquide fondu. Secondaire - diminution de la température plus lente, à partir de l'austénite. Tertiaire - refroidissement progressif, à partir de ferrite.
- Mélange mécanique de grains de ferrite et de cémentite - perlite.
- Mélange mécanique de grains de perlite ou d'austénite et de cémentite - ledeburite.
Les fontes ont une microstructure particulière. Le graphite peut être sous une forme liée et former les structures ci-dessus, ou il peut être à l'état libre sous la forme de diverses inclusions. Les propriétés sont affectées à la fois par les grains principaux et par ces formations. Les fractions de graphite dans le métal sont des plaques, des flocons ou des billes.
La forme lamellaire est caractéristique des alliages fonte grise-carbone. Cela les rend fragiles et peu fiables.
Les inclusions lamellaires ont des fontes malléables, qui ont un effet positif sur leurs performances mécaniques.
La structure sphérique du graphite est encore plusaméliore la qualité du métal, affectant l'augmentation de la dureté, la fiabilité, l'exposition à des charges importantes. La fonte à haute résistance présente ces caractéristiques. La fonte malléable détermine ses propriétés par des bases ferritiques ou perlitiques avec la présence d'inclusions de graphite lamellaire.
Production de fonte ductile ferritique
Il est produit à partir d'un alliage à faible teneur en carbone hypoeutectoïde de porc blanc par recuit de lingots ayant une teneur en carbone de 2,4 à 2,8 % et la présence d'additifs correspondants (Mn, Si, S, P). L'épaisseur des parois des pièces recuites ne doit pas dépasser 5 cm. Pour les pièces coulées d'épaisseur importante, le graphite a la forme de plaques et les propriétés souhaitées ne sont pas atteintes.
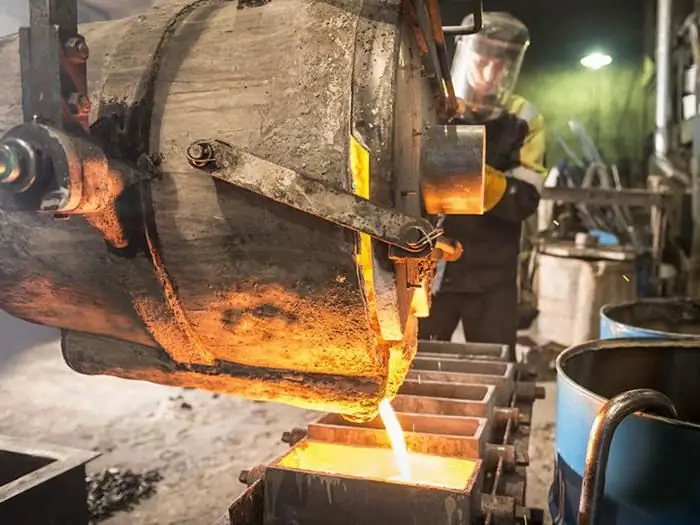
Pour obtenir de la fonte ductile à base ferritique, le métal est placé dans des boîtes spéciales et saupoudré de sable. Des récipients hermétiquement fermés sont placés dans des fours de chauffage. Effectuez la séquence d'actions suivante pendant le recuit:
- Les structures sont chauffées dans des fours à une température de 1 000 ˚C et laissées au repos à chaleur constante pendant une durée de 10 à 24 heures. En conséquence, la cémentite primaire et la ledeburite se désintègrent.
- Le métal est refroidi à 720 ˚С avec le four.
- À une température de 720 ˚С, ils se conservent longtemps: de 15 à 30 heures. Cette température assure la décomposition de la cémentite secondaire.
- Au stade final, ils sont à nouveau refroidis avec le poêle de travail à 500 ˚С, puis retirés à l'air.
Ce recuit technologique est appelé graphitisation.
Après le travail effectué, la microstructure du matériau estferrite à grains de graphite lamellaire. Ce type est appelé "coeur noir" car la cassure est noire.
Production de fonte ductile perlitique
Il s'agit d'une sorte d'alliage fer-carbone, qui provient également du blanc hypoeutectoïde, mais dont la teneur en carbone est augmentée: 3-3,6 %. Pour obtenir des pièces moulées à base de perlite, elles sont placées dans des caisses et saupoudrées de minerai de fer en poudre broyé ou de calamine. La procédure de recuit elle-même est simplifiée.
- La température du métal est portée à 1 000 ˚C, maintenue pendant 60 à 100 heures.
- Designs refroidissent avec le four.
En raison de la langueur sous l'influence de la chaleur, une diffusion se produit dans l'environnement métallique: le graphite libéré lors de la désintégration de la cémentite quitte partiellement la couche superficielle des pièces recuites, se déposant à la surface du minerai ou de la calamine. Une couche supérieure plus douce, plus ductile et ductile de fonte ductile "à cœur blanc" avec un centre dur est obtenue.
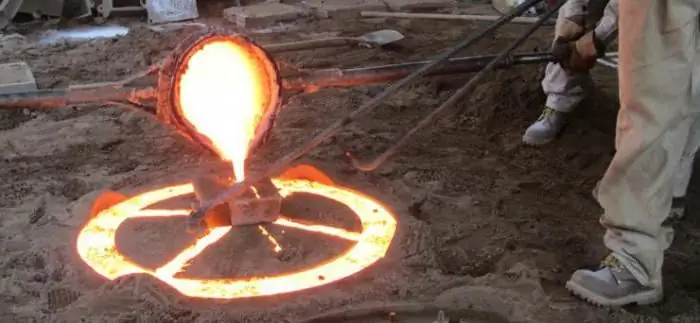
Un tel recuit est dit incomplet. Il assure la désintégration de la cémentite et de la ledeburite en perlite lamellaire avec le graphite correspondant. Si une fonte ductile perlitique granulaire avec une résistance aux chocs et une ductilité plus élevées est requise, un chauffage supplémentaire du matériau jusqu'à 720 ˚С est appliqué. Il en résulte la formation de grains de perlite avec des inclusions de graphite feuilleté.
Propriétés, marquages et applications de la fonte ductile ferritique
Une longue "languissante" du métal dans le four entraîne la décomposition complète de la cémentite et de la ledeburite en ferrite. Grâce àastuces technologiques, un alliage à haute teneur en carbone est obtenu - une structure ferritique caractéristique de l'acier à faible teneur en carbone. Cependant, le carbone lui-même ne disparaît nulle part - il passe d'un état lié au fer à un état libre. L'effet de la température change la forme des inclusions de graphite en flocons.
La structure ferritique provoque une diminution de la dureté, une augmentation des valeurs de résistance, la présence de caractéristiques telles que la résistance aux chocs et la ductilité.
Marquage des fontes ductiles de classe ferritique: KCh30-6, KCh33-8, KCh35-10, KCh37-12, où:
KCh - désignation variétale - malléable;
30, 33, 35, 37: σv, 300, 330, 350, 370 N/mm2 - charge maximale qu'il peut supporter sans s'effondrer;
6, 8, 10, 12 - allongement relatif, δ, % - indice de ductilité (plus la valeur est élevée, plus le métal peut être traité par pression).
Dureté - environ 100-160 HB.
Ce matériau, en termes de performances, occupe une position intermédiaire entre l'acier et l'alliage fer-carbone gris. La fonte ductile à base ferritique est inférieure à la perlitique en termes de résistance à l'usure, à la corrosion et à la fatigue, mais supérieure en termes d'endurance mécanique, de ductilité et de caractéristiques de coulée. En raison de son faible prix, il est très utilisé dans l'industrie pour la fabrication de pièces fonctionnant sous de faibles et moyennes charges: engrenages, carters, trains arrière, plomberie.
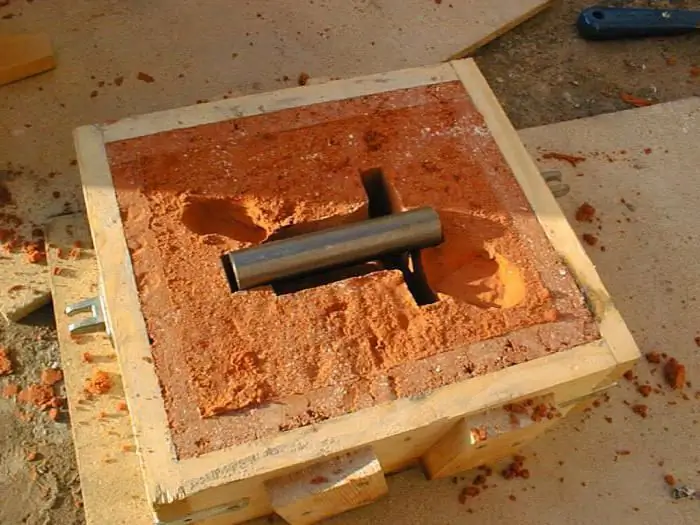
Propriétés, marquages et applications de la fonte ductile perlitique
En raison d'un recuit incomplet, les cémentites primaires et secondaires et la ledeburite ont le temps de se dissoudre complètement dans l'austénite qui, à une température de 720 ˚С, se transforme en perlite. Ce dernier est un mélange mécanique de grains de ferrite et de cémentite tertiaire. En fait, une partie du carbone reste sous une forme liée, détermine la structure et une partie est «libérée» dans du graphite feuilleté. Dans ce cas, la perlite peut être lamellaire ou granuleuse. Ainsi se forme la fonte ductile perlitique. Ses propriétés sont dues à sa structure saturée, plus dure et moins malléable.
Ceux-ci, par rapport aux ferritiques, ont des propriétés anti-corrosion et anti-usure plus élevées, leur résistance est beaucoup plus élevée, mais des caractéristiques de coulée et une ductilité inférieures. La souplesse aux contraintes mécaniques est augmentée superficiellement, tout en maintenant la dureté et la viscosité du noyau du produit.
Marquage de la classe perlitique en fonte malléable: KCh45-7, KCh50-5, KCh56-4, KCh60-3, KCh65-3, KCh70-2, KCh80-1, 5.
Le premier chiffre est la désignation de la force: 450, 500, 560, 600, 650, 700 et 800 N/mm2 respectivement.
Deuxième - la désignation de la plasticité: allongement δ,% - 7, 5, 4, 3, 3, 2 et 1, 5.
La fonte malléable perlitique a été utilisée en mécanique et en instrumentation pour les ouvrages soumis à de fortes charges statiques et dynamiques: arbres à cames, vilebrequins, pièces d'embrayage, pistons, bielles.
Traitement thermique
Le matériau obtenu à la suite d'un traitement thermique, à savoir le recuit, peut être reêtre soumis aux influences de la température. Leur objectif principal est d'augmenter encore la résistance, la résistance à l'usure, la résistance à la corrosion et au vieillissement.
- Le durcissement est utilisé pour les structures nécessitant une dureté et une ténacité élevées; produites par chauffage jusqu'à 900 ˚С, les pièces sont refroidies à une vitesse moyenne d'environ 100 ˚С/sec à l'aide d'huile de machine. Il est suivi d'un revenu élevé avec chauffage jusqu'à 650˚С et refroidissement à l'air.
- La normalisation est utilisée pour les pièces simples de taille moyenne par chauffage dans un four à 900 ˚С, maintien à cette température pendant une durée de 1 à 1,5 heures puis refroidissement à l'air. Fournit la perlite granulaire de troostite, sa dureté et sa fiabilité en frottement et en usure. Il est utilisé pour obtenir des fontes malléables antifriction à base perlitique.
- Le recuit est répété dans la fabrication de l'antifriction: chauffage - jusqu'à 900 ˚С, maintien à long terme à cette chaleur, refroidissement avec le four. La structure ferritique ou ferrito-perlitique de la fonte ductile antifriction est fournie.
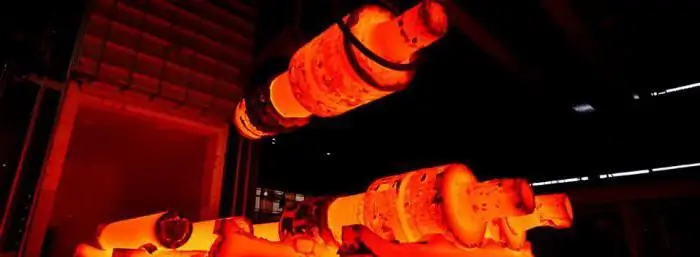
Le chauffage des produits en fonte peut être effectué localement ou en combinaison. Pour une utilisation locale, des courants haute fréquence ou une flamme d'acétylène (durcissement). Pour complexes - fours de chauffage. Avec un chauffage local, seule la couche supérieure est durcie, tandis que sa dureté et sa résistance augmentent, mais la plasticité et la viscosité du noyau restent.
Il est important de souligner ici que le forgeage de la fonte est impossible non seulement en raison d'une mécanique insuffisantecaractéristiques, mais aussi en raison de sa grande sensibilité à une forte chute de température, ce qui est inévitable lors de la trempe avec refroidissement à l'eau.
Fontes ductiles antifriction
Cette variété s'applique à la fois aux matériaux malléables et alliés, ils sont gris (ASF), malléables (ASC) et à haute résistance (ACS). La fonte ductile est utilisée pour la production d'ACHK, qui est recuit ou normalisé. Les processus sont effectués afin d'augmenter ses propriétés mécaniques et de former une nouvelle caractéristique - la résistance à l'usure lors du frottement avec d'autres pièces.
Marqué: AChK-1, AChK-2. Il est utilisé pour la production de vilebrequins, engrenages, roulements.
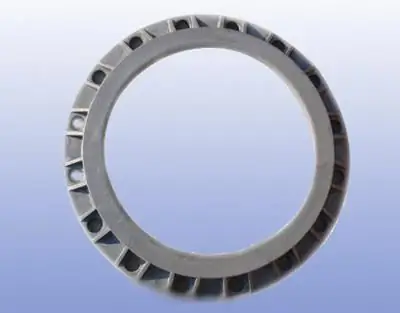
Influence des additifs sur les propriétés
En plus de la base fer-carbone et du graphite, ils contiennent également d'autres composants qui déterminent également les propriétés de la fonte: manganèse, silicium, phosphore, soufre et certains éléments d'alliage.
Mangan augmente la fluidité du métal liquide, la résistance à la corrosion et la résistance à l'usure. Il aide à augmenter la dureté et la résistance, à lier le carbone au fer dans la formule chimique Fe3C, la formation de perlite granulaire.
Le silicium a également un effet positif sur la fluidité de l'alliage liquide, favorise la décomposition de la cémentite et la libération d'inclusions de graphite.
Le soufre est un composant négatif mais inévitable. Il réduit les propriétés mécaniques et chimiques, stimule la formation de fissures. Cependant, le rapport rationnel de sa teneur avec d'autres éléments (par exemple, avec du manganèse) permetprocessus microstructuraux corrects. Ainsi, au rapport Mn-S de 0,8-1,2, la perlite est préservée à tout moment des influences de la température. Lorsque le rapport est augmenté à 3, il devient possible d'obtenir n'importe quelle structure nécessaire, en fonction des paramètres spécifiés.
Le phosphore améliore la fluidité, affecte la résistance, réduit la résistance aux chocs et la ductilité, affecte la durée de la graphitisation.
Le chrome et le molybdène entravent la formation de flocons de graphite, dans certains contenus, ils contribuent à la formation de perlite granulaire.
Le tungstène améliore la résistance à l'usure dans les zones à haute température.
L'aluminium, le nickel, le cuivre contribuent à la graphitisation.
En ajustant la quantité d'éléments chimiques qui composent l'alliage fer-carbone, ainsi que leur rapport, il est possible d'influencer les propriétés finales de la fonte.
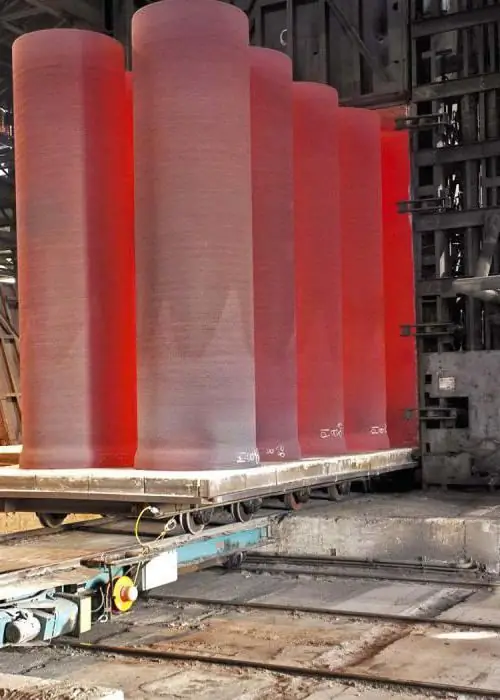
Avantages et inconvénients
La fonte ductile est un matériau largement utilisé en ingénierie. Ses principaux avantages:
- haute dureté, résistance à l'usure, solidité et fluidité;
- caractéristiques normales de ténacité et de ductilité;
- manufacturabilité en formage, contrairement aux fontes grises;
- diverses options pour corriger les propriétés d'une pièce spécifique par des méthodes de traitement thermique et chimico-thermique;
- faible coût.
Les inconvénients incluent les caractéristiques individuelles:
- fragilité;
- présence d'inclusions de graphite;
- mauvaise performance de coupe;
- poids considérable des castings.
Malgré les lacunes existantes, la fonte ductile occupe une place de choix dans la métallurgie et l'ingénierie. Des pièces aussi importantes que les vilebrequins, les pièces de plaquettes de frein, les engrenages, les pistons, les bielles en sont fabriquées. Ayant une variété insignifiante de nuances, la fonte ductile occupe une niche individuelle dans l'industrie. Son utilisation est typique pour les charges dans lesquelles l'utilisation d'autres matériaux est peu probable.
Conseillé:
Machine électroérosive : domaine d'application et principe de fonctionnement
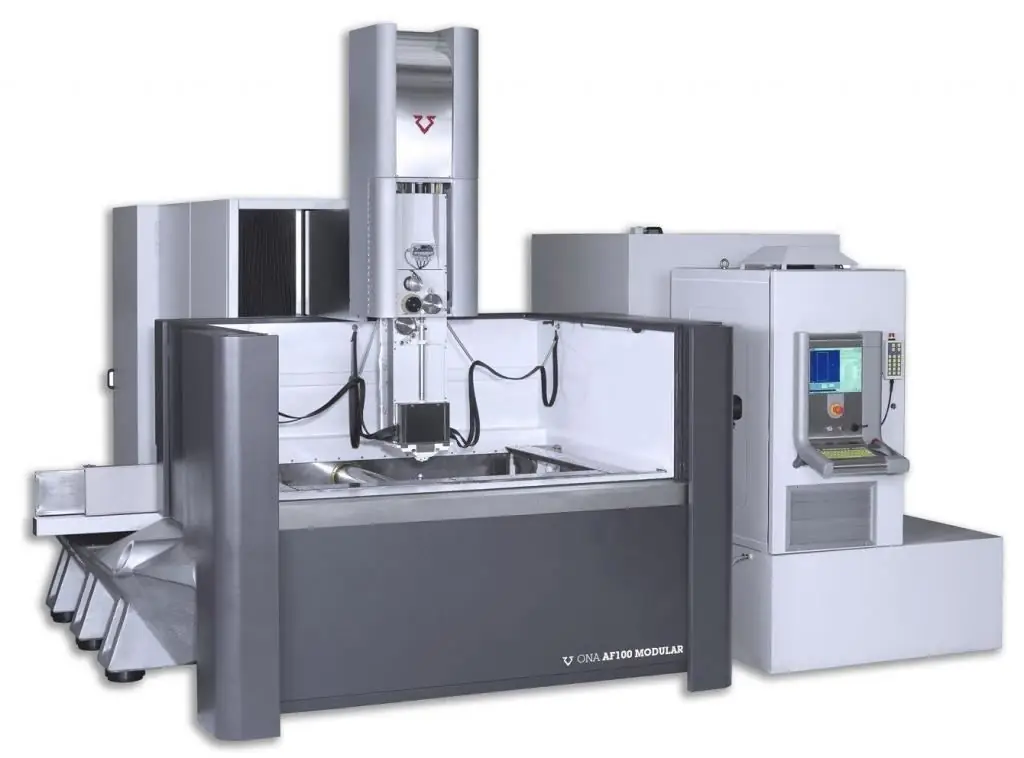
Si auparavant la machine EDM était une rareté, aujourd'hui un tel équipement n'est plus une surprise. L'électroérosion est comprise comme la destruction des forces interatomiques d'interaction dans les métaux sous l'influence d'une charge électrique. La machine électroérosive doit son apparition aux développements des scientifiques soviétiques B. R. Lazarenko et N. I. Lazarenko. Un tel équipement est universel. Il vous permet de traiter et de façonner n'importe quelle qualité de métaux et d'alliages
Désignation des éléments d'alliage en acier : classification, propriétés, marquage, application
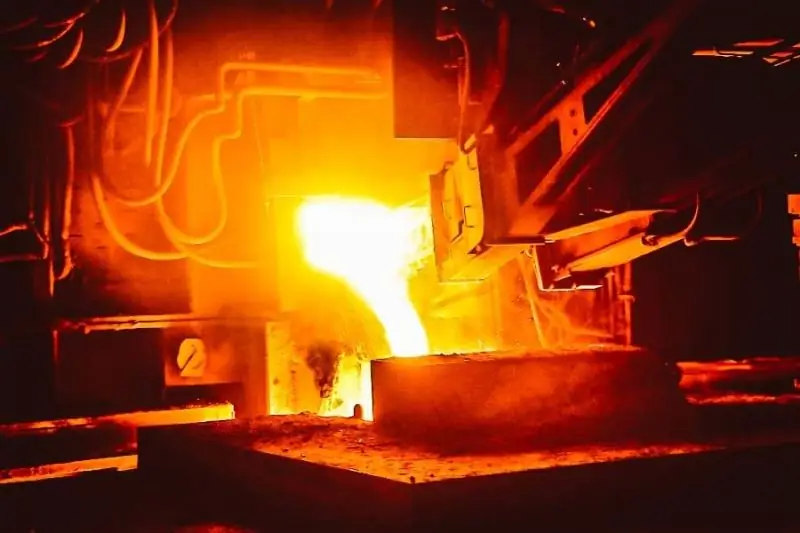
Aujourd'hui, une variété d'aciers sont utilisés dans de nombreuses industries. Une variété de qualité, de propriétés mécaniques et physiques est obtenue en alliant le métal. La désignation des éléments d'alliage dans l'acier permet de déterminer quels composants ont été introduits dans la composition, ainsi que leur teneur quantitative
Types de fonte, classification, composition, propriétés, marquage et application
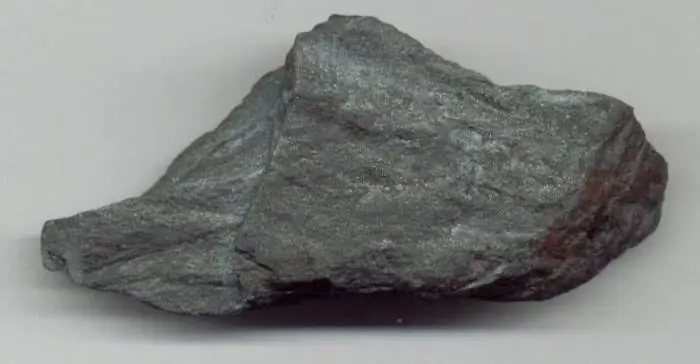
Les types de fonte qui existent aujourd'hui permettent à une personne de créer de nombreux produits. Par conséquent, nous parlerons de ce matériau plus en détail dans cet article
Marquage du bronze : caractéristiques, propriétés et portée
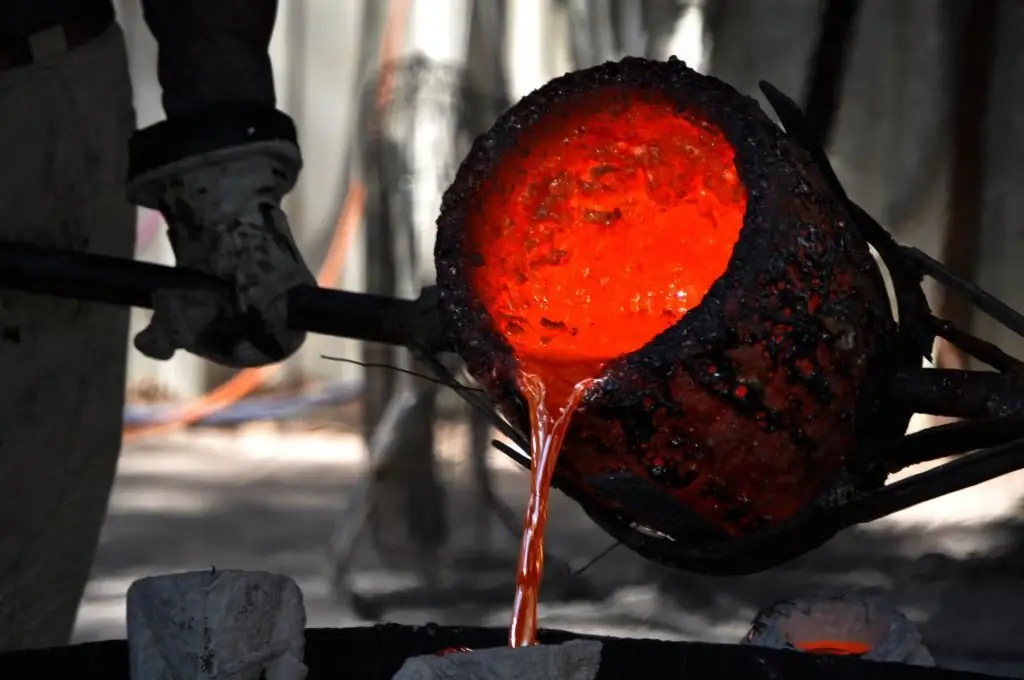
En raison de ses caractéristiques décoratives et de nombreuses autres propriétés, le bronze est devenu populaire. Il est très difficile, même pour les connaisseurs, de nommer toutes les impuretés et additifs présents dans les alliages de bronze. Cet article se concentrera sur le bronze et son marquage
Fonte blanche : propriétés, applications, structure et caractéristiques
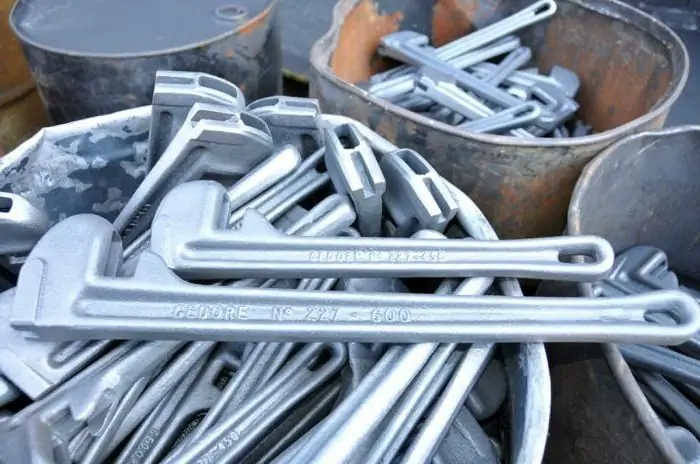
Initialement, la technologie de la fonte a été maîtrisée pour la première fois en Chine au 10ème siècle, après quoi elle s'est répandue dans d'autres pays du monde. Un représentant éminent d'un tel alliage est la fonte blanche, qui est utilisée dans la construction mécanique pour la fabrication de pièces, dans l'industrie et dans la vie quotidienne