2025 Auteur: Howard Calhoun | [email protected]. Dernière modifié: 2025-01-24 13:16
Un four à arc en acier (EAF) est un appareil qui chauffe le matériau par pliage électrique.
Les appareils industriels varient en taille, allant de petites unités, d'environ une tonne de puissance (utilisées dans les fonderies pour fabriquer des produits en fonte) à 400 unités par tonne, utilisées pour le recyclage de l'acier. Les fours à arc en acier, EAF, utilisés dans les laboratoires de recherche peuvent n'avoir qu'une capacité de quelques dizaines de grammes. La température des appareils industriels peut atteindre 1800 °C (3272 °F), tandis que les installations de laboratoire dépassent 3000 °C (5432 °F).
Les fours à arc en acier (EAF) diffèrent des fours à induction en ce que le matériau chargé est directement soumis à une flexion électrique et que le courant aux bornes traverse le matériau chargé.
Construction
Le four à acier à arc est utilisé pour la production d'acier et est composé d'une cuve réfractaire. Principalement divisé en trois sections:
- Shell, qui se compose de parois latérales et d'un fond en acierbols.
- Palette en matériau réfractaire.
- Toit. Il peut être avec une doublure résistante à la chaleur ou refroidi à l'eau. Et il est également réalisé sous la forme d'une boule ou d'un tronc de cône (section conique). Le toit supporte également un delta réfractaire en son centre par lequel pénètrent une ou plusieurs électrodes en graphite.
Articles individuels
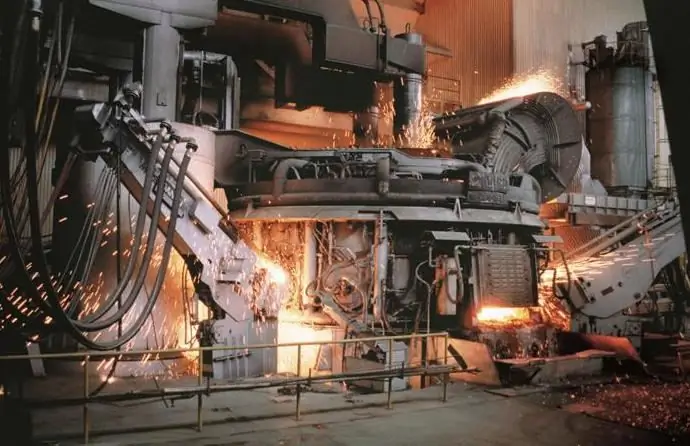
Le foyer peut avoir une forme hémisphérique et est nécessaire dans un four excentrique pour tarauder le fond. Dans les ateliers modernes, le four à arc en acier - EAF 5 - est souvent surélevé au-dessus du rez-de-chaussée afin que les poches et les pots à scories puissent être facilement manoeuvrés sous chaque extrémité. Le support des électrodes et le système électrique sont séparés de la structure, ainsi que la plate-forme inclinée sur laquelle repose l'instrument.
Outil unique
Un four à arc de fusion d'acier EAF 3 typique est alimenté par une source triphasée et possède donc trois électrodes. Ils ont une section ronde et, en règle générale, des segments avec des connexions filetées, de sorte qu'à mesure qu'ils s'usent, de nouveaux éléments peuvent être ajoutés.
L'arc se forme entre le matériau chargé et l'électrode. La charge est chauffée à la fois par le courant qui la traverse et par l'énergie rayonnée dégagée par l'onde. La température atteint environ 3 000 °C (5 000 °F), ce qui fait que les sections inférieures des électrodes brillent comme des lampes à incandescence lorsque le four à arc fonctionne.
Les éléments sont automatiquement levés et abaissés par un système de positionnement qui peut utiliser n'importe quel appareil électriquetreuil, palans ou vérins hydrauliques. La régulation maintient un courant approximativement constant. Quelle est la consommation électrique d'un four à arc ? Il est maintenu constant pendant la fusion de la charge, même si les déchets peuvent se déplacer sous les électrodes lors de la fusion. Les manchons de mât qui maintiennent l'élément peuvent soit porter des barres omnibus lourdes (qui peuvent être des tubes de cuivre creux refroidis à l'eau fournissant du courant aux pinces) ou des "manchons chauds" où tout le dessus porte la charge, augmentant l'efficacité.
Ce dernier type peut être en acier cuivré ou en aluminium. De gros câbles refroidis à l'eau relient les jeux de barres ou les supports à un transformateur situé à côté du four. Un outil similaire est installé dans le stockage et refroidi avec de l'eau.
Tap et autres opérations
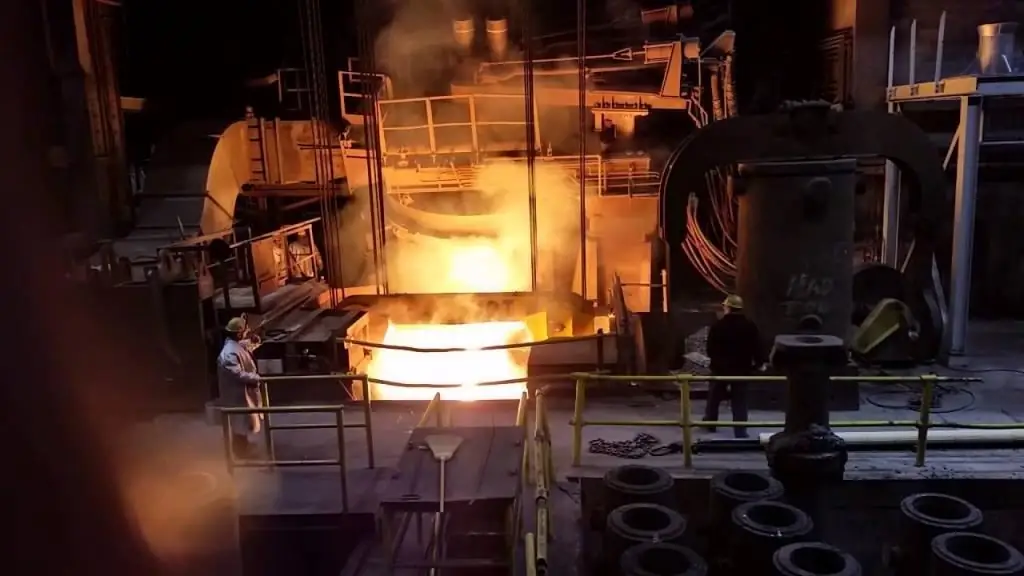
Le four à arc en acier EAF 50 est construit sur une plate-forme inclinée afin que l'acier liquide puisse être versé dans un autre conteneur pour le transport. L'opération d'inclinaison pour transférer l'acier fondu est appelée taraudage. Initialement, toutes les voûtes sidérurgiques du four à arc avaient une goulotte d'évacuation recouverte de réfractaire, qui était emportée lorsqu'elle était inclinée.
Mais souvent, les équipements modernes sont équipés d'une vanne de sortie de fond excentrique (EBT) pour réduire l'incorporation d'azote et de laitier dans l'acier liquide. Ces fours ont une ouverture qui traverse verticalement le foyer et la coque et est décentrée dans un "bec" étroit en forme d'œuf. C'est remplisable réfractaire.
Les plantes modernes peuvent avoir deux coquilles avec un jeu d'électrodes qui passent entre elles. La première partie chauffe la ferraille, tandis que l'autre est utilisée pour la fonte. D'autres fours à courant continu ont une disposition similaire mais ont des électrodes pour chaque gaine et un ensemble d'électronique.
Éléments oxygène
Les fours à courant alternatif ont généralement un motif de points chauds et froids le long du périmètre du foyer, situés entre les électrodes. Dans les modèles modernes, des brûleurs oxy-combustible sont installés dans la paroi latérale. Ils sont utilisés pour fournir de l'énergie chimique aux zones négatives, ce qui rend le chauffage de l'acier plus uniforme. Une puissance supplémentaire est fournie en fournissant de l'oxygène et du carbone au four. Historiquement, cela se faisait avec des lances (tubes creux en acier doux) dans la porte de scories, maintenant cela se fait principalement avec des unités d'injection murales qui combinent des brûleurs oxy-combustible et des systèmes d'alimentation en air dans un seul récipient.
Un four en acier moderne de taille moyenne a un transformateur évalué à environ 60 000 000 ampères volts (60 MVA), avec une tension secondaire de 400 à 900 et un courant supérieur à 44 000. Dans un atelier moderne, un tel le four devrait produire 80 tonnes d'acier liquide en 50 minutes environ, du chargement de la ferraille à froid au taraudage.
En comparaison, les fours à oxygène de base peuvent avoir une capacité de 150 à 300 tonnes par lot ou "chauffer" et générer de la chaleur pendant 30 à 40 minutes. Il existe d'énormes différences dans les détails de la conception et du fonctionnement du four,en fonction du produit final et des conditions locales, ainsi que des recherches en cours pour améliorer l'efficacité de l'usine.
Le plus gros rebut uniquement (en termes de poids de prise et de puissance du transformateur) est un appareil à courant continu exporté du Japon avec un poids de prise de 420 tonnes métriques et alimenté par huit transformateurs de 32 MVA pour une puissance totale de 256 MBA.
Il faut environ 400 kilowattheures pour produire une tonne d'acier dans un four à arc électrique, soit environ 440 kWh par métrique. L'énergie minimale théorique requise pour fondre la ferraille est de 300 kWh (point de fusion 1520 °C / 2768 °F). Par conséquent, un EAF de 300 tonnes d'une puissance de 300 MVA nécessitera environ 132 MWh d'énergie et le temps de mise en marche est d'environ 37 minutes.
La production d'acier à l'arc électrique n'est économiquement viable que s'il y a suffisamment d'électricité avec un réseau bien développé. Dans de nombreux endroits, les usines fonctionnent pendant les heures creuses lorsque les services publics ont une capacité de production excédentaire et que le prix au mètre est plus bas.
Opération
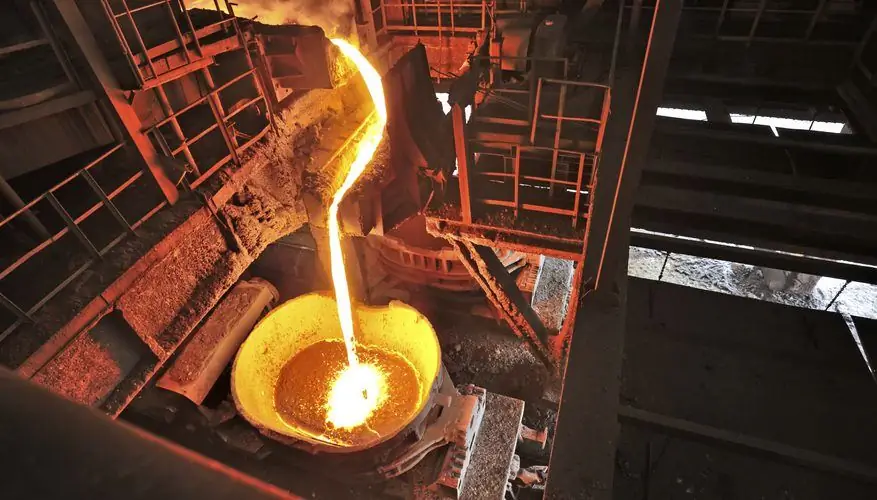
Le four à arc verse de l'acier dans une petite machine à poche. La ferraille est livrée dans un renfoncement situé à côté de la fonderie. La ferraille se présente sous deux formes principales: la ferraille (produits blancs, voitures et autres articles fabriqués à partir de matériaux similaires)acier léger) et de la fonte lourde (grandes dalles et poutres), ainsi que du fer à réduction directe (DRI) ou de la fonte brute pour l'équilibre chimique. Des fours séparés fondent presque 100 % de DRI.
Étape suivante
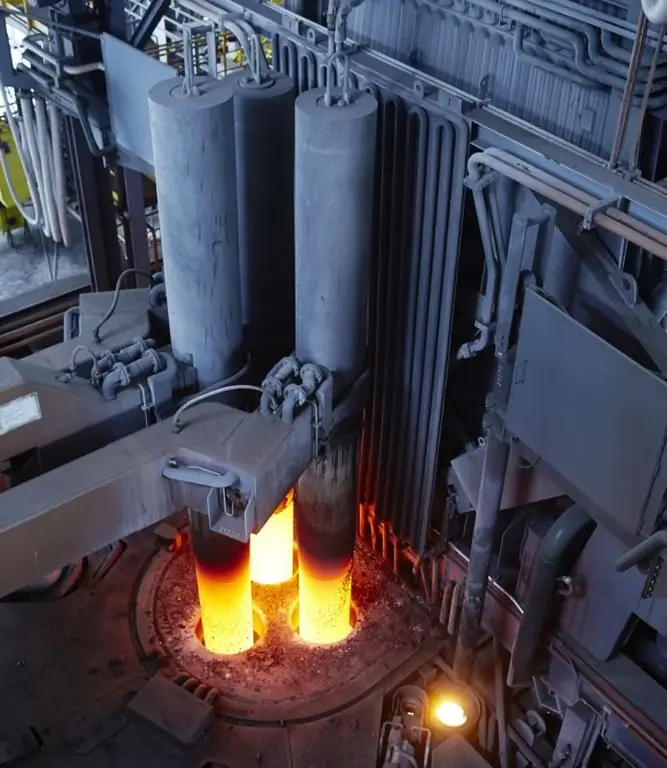
La ferraille est chargée dans de grands seaux, appelés paniers, avec des portes à clapet pour la base. Il faut veiller à ce que la ferraille soit bien dans le panier pour assurer le bon fonctionnement du four. Une forte fonte est déposée sur le dessus avec une légère couche de lambeau protecteur, au-dessus de laquelle se trouve une autre partie. Tous doivent être présents dans le four après le chargement. À ce moment, le panier peut se déplacer dans le préchauffeur de ferraille, qui utilise les gaz de dégagement chauds de la fonderie pour récupérer de l'énergie, améliorant ainsi l'efficacité.
Débordement
Ensuite, le navire est amené à la fonderie, le toit du four est ouvert et le matériau y est chargé. Le transfert est l'une des opérations les plus dangereuses pour les opérateurs. Beaucoup d'énergie potentielle est libérée par des tonnes de métal qui tombe. Toute matière liquide dans le four est souvent poussée vers le haut et vers l'extérieur par des déchets solides et de la graisse. La poussière sur le métal s'enflamme si le four est chaud, provoquant l'éruption d'une boule de feu.
Dans certains appareils à double coque, la ferraille est chargée dans la seconde pendant que la première fond, et est préchauffée par les gaz d'échappement de la partie active. Les autres opérations sont: le chargement continu et le travail en température sur un tapis roulant, qui décharge ensuite le métal dans le four lui-même. D'autres appareils peuvent démarrersubstance chaude provenant d'autres opérations.
Tension
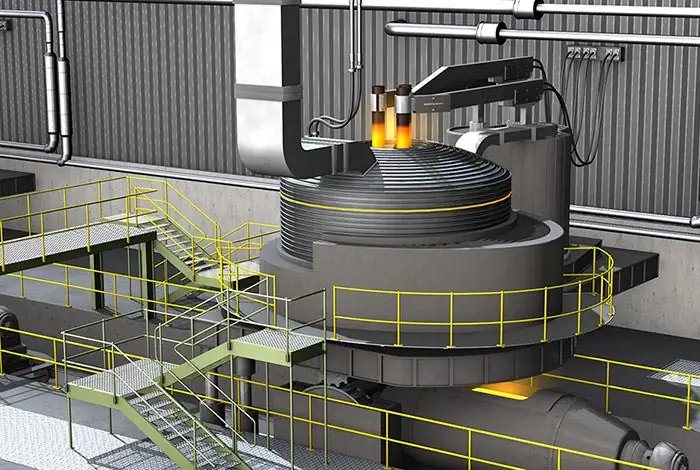
Après le chargement, le toit se penche en arrière sur le four et la fusion commence. Les électrodes sont abaissées sur la ferraille, un arc est créé, puis elles sont réglées de manière à se répandre dans la couche de miettes au sommet de l'appareil. Des basses tensions sont sélectionnées pour cette opération afin de protéger le toit et les murs de la chaleur excessive et des dommages causés par les arcs.
Une fois que les électrodes ont atteint la fonte lourde à la base du four et que les ondes sont protégées par le pied de biche, la tension peut être augmentée et les électrodes légèrement relevées, allongeant et augmentant la puissance de la fonte. Cela permet au bain de fusion de se former plus rapidement, ce qui réduit le temps de dérivation.
L'oxygène est insufflé dans la ferraille, brûlant ou coupant l'acier, et une chaleur chimique supplémentaire est fournie par des brûleurs muraux. Les deux processus accélèrent la fusion de la substance. Des buses supersoniques permettent aux jets d'oxygène de pénétrer dans le laitier moussant et d'atteindre le bain liquide.
Oxydation des impuretés
Une partie importante de la fabrication de l'acier est la formation de scories qui flottent à la surface de l'acier en fusion. Il est généralement composé d'oxydes métalliques et agit également comme un lieu de collecte des impuretés oxydées, comme une couverture thermique (arrêtant une perte de chaleur excessive) et contribue également à réduire l'érosion du revêtement réfractaire.
Pour un four à réfractaires basiques produisant de l'acier au carbone, les formateurs de laitier courants sont l'oxyde de calcium (CaO sous forme dechaux) et magnésium (MgO sous forme de dolomie et de magnésite.). Ces substances sont soit chargées de ferraille, soit soufflées dans le four lors de la fusion.
Un autre composant important est l'oxyde de fer, formé lorsque l'acier est brûlé avec de l'oxygène introduit. Plus tard, lorsqu'il est chauffé, du carbone (sous forme de charbon) est injecté dans cette couche, réagissant avec l'oxyde de fer pour former du métal et du monoxyde de carbone. Il en résulte un moussage du laitier, ce qui se traduit par une plus grande efficacité thermique. Le revêtement évite d'endommager le toit et les parois latérales du four à cause de la chaleur rayonnante.
Combustion des impuretés
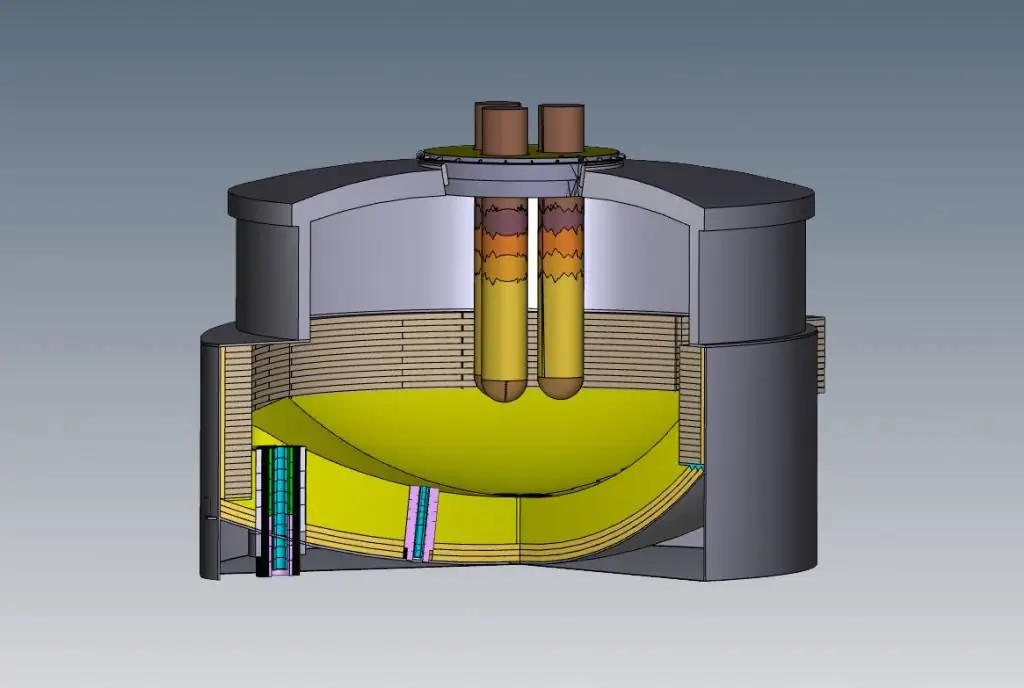
Une fois que la ferraille est complètement fondue et qu'un bassin plat est atteint, un autre seau peut être chargé dans le four. Après la fusion complète de la deuxième charge, des opérations d'affinage sont effectuées pour vérifier et corriger la composition chimique de l'acier et surchauffer la masse fondue au-dessus de son point de congélation en vue de la coulée. Plus de formateurs de scories sont introduits et beaucoup d'oxygène pénètre dans le bain, brûlant des impuretés telles que le silicium, le soufre, le phosphore, l'aluminium, le manganèse et le calcium, et éliminant leurs oxydes dans les scories.
L'élimination du carbone se produit après que ces éléments ont brûlé en premier, car ils sont plus similaires à l'oxygène. Les métaux qui ont une affinité inférieure à celle du fer, comme le nickel et le cuivre, ne peuvent pas être éliminés par oxydation et ne doivent être contrôlés que par la chimie. Il s'agit, par exemple, de l'introduction de la fonte et de la fonte par réduction directe mentionnée plus haut.
Laitier mousseuxpersiste partout et déborde souvent du four pour déborder de la porte dans la fosse prévue. La mesure de la température et la sélection chimique sont effectuées à l'aide de lances automatiques. L'oxygène et le carbone peuvent être mesurés mécaniquement avec des sondes spéciales immergées dans l'acier.
Avantages de production
À l'aide d'un système de contrôle pour les fours à arc de fusion d'acier, il est possible de produire de l'acier à partir de 100 % de matière première - de la ferraille. Cela réduit considérablement l'énergie nécessaire pour produire la substance, par rapport à la production primaire à partir de minerais.
Un autre avantage est la flexibilité: alors que les hauts fourneaux ne peuvent pas varier de manière significative et peuvent fonctionner pendant des années, celui-ci peut être démarré et arrêté rapidement. Cela permet à l'aciérie de varier sa production en fonction de la demande.
Le four à acier à arc typique est la source d'acier pour les mini-usines, qui peuvent produire des barres ou des bandes. Les mini-fonderies peuvent être situées relativement près des marchés de l'acier et les besoins en transport sont moindres que pour une usine intégrée, qui est généralement située près du rivage pour l'accès maritime.
Arc Steel Furnace Device
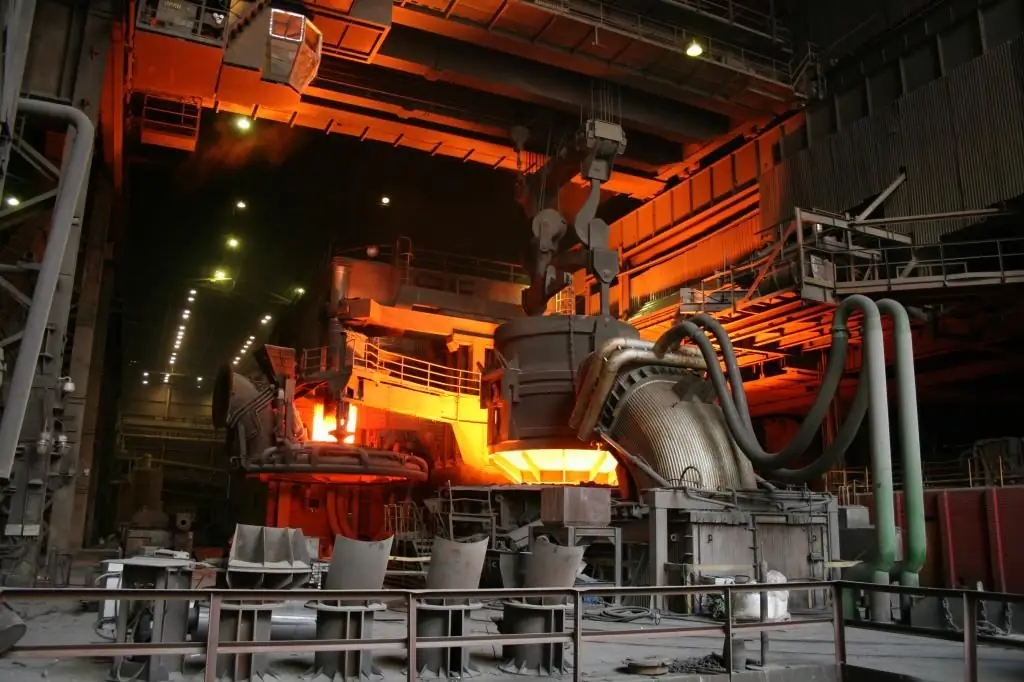
La section schématique est une électrode qui est soulevée et abaissée par un entraînement à crémaillère et pignon. La surface est revêtue de briques réfractaires et d'un revêtement de fond. La porte permet d'accéder à l'intérieurparties de l'appareil. Le corps du four repose sur des culbuteurs afin de pouvoir l'incliner pour le tapotement.
Conseillé:
Qu'est-ce que la puissance réactive ? Compensation de puissance réactive. Calcul de la puissance réactive
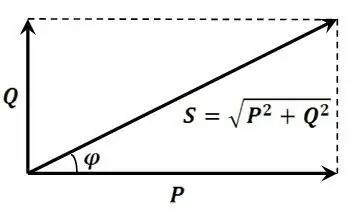
Dans les conditions réelles de production, la puissance réactive de nature inductive prévaut. Les entreprises installent non pas un compteur électrique, mais deux, dont l'un est actif. Et pour les dépenses excessives d'énergie «chassées» en vain par les lignes électriques, les autorités compétentes sont condamnées à une amende impitoyable
Capteurs de contrôle de flamme - caractéristiques, dispositif et principe de fonctionnement
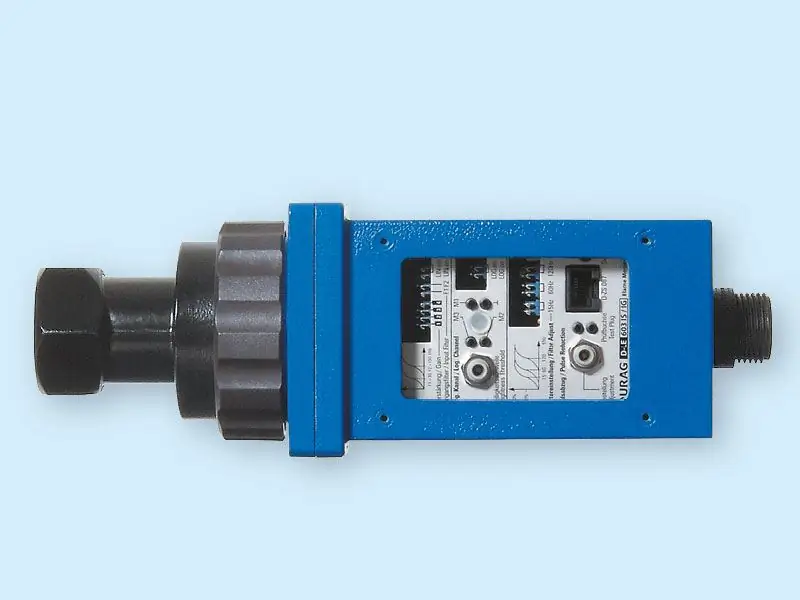
Aujourd'hui, les gens utilisent activement le feu à leurs propres fins. Cependant, il est très dangereux et, par conséquent, lorsque vous travaillez avec, il est nécessaire de mettre la sécurité en premier lieu. A l'échelle industrielle, ce rôle est joué par un capteur de contrôle de flamme
Batteries de four à coke : appareil, principe de fonctionnement, finalité. Technologie de production de coke
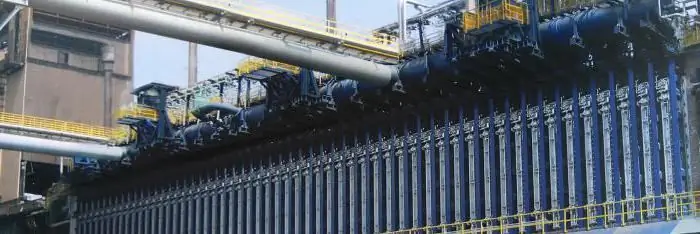
Les batteries de four à coke sont une installation industrielle complexe et importante. Nous parlerons de son travail et de son appareil dans l'article
Four à induction creuset : principe de fonctionnement, schéma et avis
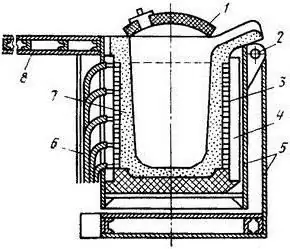
Le chauffage par induction peut être utilisé pour travailler avec n'importe quel matériau : métal, laitier, gaz, etc. Le principal avantage de son utilisation est le transfert de chaleur sans contact. De plus, le chauffage par induction vous permet d'atteindre presque n'importe quelle vitesse de chauffage - tout dépend de la puissance du générateur qui alimente le four
Laser à fibre Ytterbium : dispositif, principe de fonctionnement, puissance, production, application
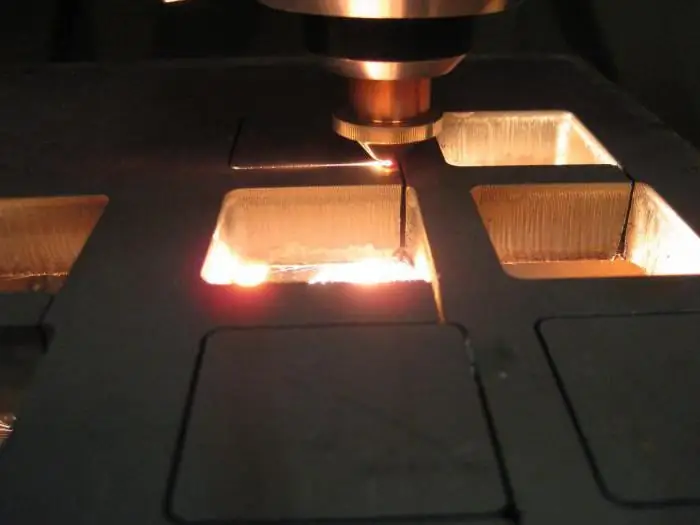
Les lasers à fibre sont compacts et robustes, pointent avec précision et dissipent facilement l'énergie thermique. Ils se présentent sous de nombreuses formes et, ayant beaucoup en commun avec d'autres types de générateurs quantiques optiques, ont leurs propres avantages uniques