2025 Auteur: Howard Calhoun | [email protected]. Dernière modifié: 2025-01-24 13:16
Le minerai de fer est obtenu de la manière habituelle: extraction à ciel ouvert ou souterraine et transport ultérieur pour la préparation initiale, où le matériau est concassé, lavé et traité.
Le minerai est versé dans un haut fourneau et soufflé avec de l'air chaud et de la chaleur, ce qui le transforme en fer fondu. Il est ensuite retiré du bas du four dans des moules appelés gueuses, où il est refroidi pour produire de la fonte brute. Il est transformé en fer forgé ou transformé en acier de plusieurs manières.
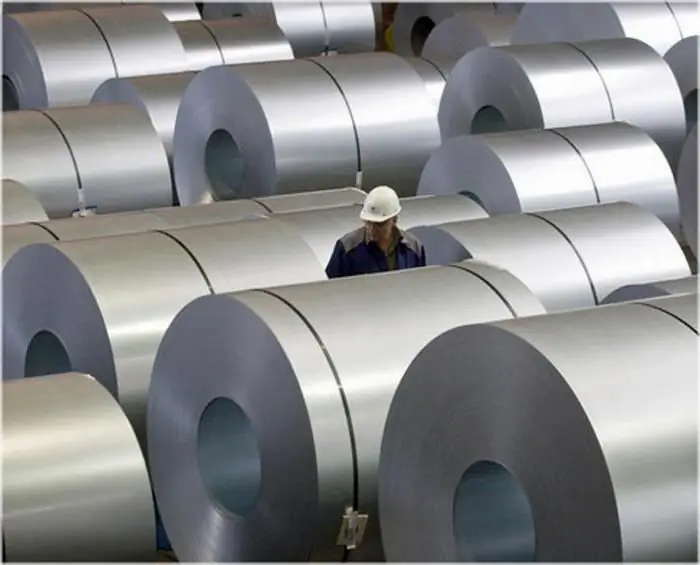
Qu'est-ce que l'acier ?
Au commencement était le fer. C'est l'un des métaux les plus communs de la croûte terrestre. On le trouve presque partout, en combinaison avec de nombreux autres éléments, sous forme de minerai. En Europe, le travail du fer remonte à 1700 av. J.-C.
En 1786, les scientifiques français Berthollet, Monge et Vandermonde ont déterminé avec précision que la différence entre le fer, la fonte et l'acier est due à une teneur en carbone différente. Néanmoins, l'acier, fabriqué à partir de fer, est rapidement devenu le métal le plus important de la révolution industrielle. Au début du XXe siècle, la production mondiale d'acier était de 28millions de tonnes - c'est six fois plus qu'en 1880. Au début de la Première Guerre mondiale, sa production était de 85 millions de tonnes. Depuis plusieurs décennies, il a pratiquement remplacé le fer.
La teneur en carbone affecte les caractéristiques du métal. Il existe deux principaux types d'acier: allié et non allié. L'alliage d'acier fait référence aux éléments chimiques autres que le carbone ajouté au fer. Ainsi, un alliage de 17 % de chrome et de 8 % de nickel est utilisé pour créer de l'acier inoxydable.
Actuellement, il existe plus de 3000 marques cataloguées (compositions chimiques), sans compter celles créées pour répondre aux besoins individuels. Tous contribuent à faire de l'acier le matériau le plus adapté aux défis du futur.
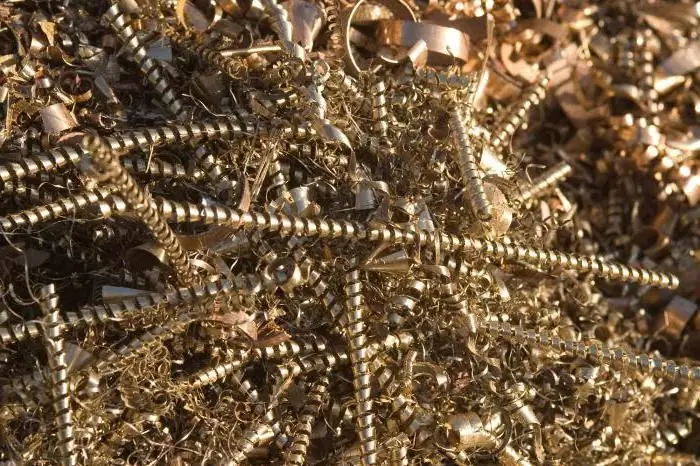
Matières premières sidérurgiques: primaires et secondaires
La fusion de ce métal à l'aide de nombreux composants est la méthode d'extraction la plus courante. Les matériaux de charge peuvent être à la fois primaires et secondaires. En règle générale, la composition principale de la charge est de 55% de fonte brute et de 45% de la ferraille restante. Les ferroalliages, la fonte convertie et les métaux commercialement purs sont utilisés comme élément principal de l'alliage, en règle générale, tous les types de métaux ferreux sont classés comme secondaires.
Le minerai de fer est la matière première la plus importante et la plus fondamentale de l'industrie sidérurgique. Il faut environ 1,5 tonne de ce matériau pour produire une tonne de fonte brute. Environ 450 tonnes de coke sont utilisées pour produire une tonne de fonte brute. De nombreuses forgesmême du charbon de bois est utilisé.
L'eau est une matière première importante pour l'industrie sidérurgique. Il est principalement utilisé pour la trempe du coke, le refroidissement des hauts fourneaux, la production de vapeur de porte de four à charbon, le fonctionnement des équipements hydrauliques et l'évacuation des eaux usées. Il faut environ 4 tonnes d'air pour produire une tonne d'acier. Le flux est utilisé dans le haut fourneau pour extraire les contaminants du minerai de la fonderie. Le calcaire et la dolomie se combinent avec les impuretés extraites pour former des scories.
Hauts-fourneaux et sidérurgies revêtus de réfractaires. Ils sont utilisés pour le parement des fours destinés à la fusion du minerai de fer. Le dioxyde de silicium ou le sable est utilisé pour le moulage. Les métaux non ferreux sont utilisés pour produire de l'acier de différentes nuances: aluminium, chrome, cob alt, cuivre, plomb, manganèse, molybdène, nickel, étain, tungstène, zinc, vanadium, etc. Parmi tous ces ferroalliages, le manganèse est largement utilisé dans la sidérurgie..
Les déchets de fer provenant des structures d'usine démantelées, des machines, des vieux véhicules, etc. sont recyclés et largement utilisés dans l'industrie.
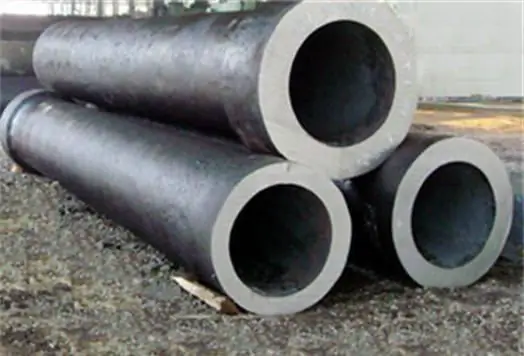
Fer pour acier
La fusion de l'acier avec de la fonte est beaucoup plus courante qu'avec d'autres matériaux. La fonte est un terme qui fait généralement référence à la fonte grise, mais elle est également identifiée à un grand groupe de ferroalliages. Le carbone représente environ 2,1 à 4 % en poids, tandis que le silicium représente généralement 1 à 3 % en poids dans l'alliage.
La fonte du fer et de l'acier a lieu à une températurepoint de fusion entre 1150 et 1200 degrés, soit environ 300 degrés inférieur au point de fusion du fer pur. La fonte présente également une bonne fluidité, une excellente usinabilité, une résistance à la déformation, à l'oxydation et à la coulée.
L'acier est également un alliage de fer à teneur variable en carbone. La teneur en carbone de l'acier est de 0,2 à 2,1 % en masse et c'est le matériau d'alliage le plus économique pour le fer. La fonte de l'acier à partir de fonte est utile à diverses fins d'ingénierie et de structure.
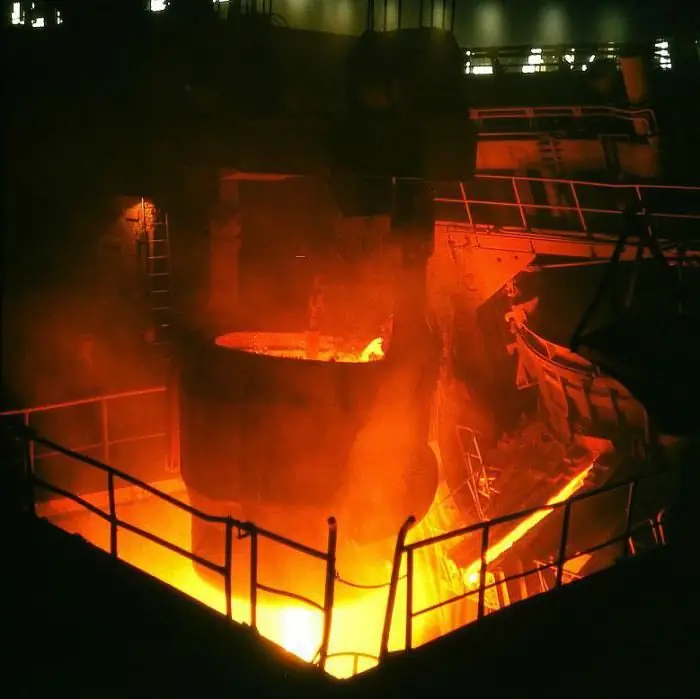
Minerai de fer pour l'acier
Le processus de fabrication de l'acier commence par le traitement du minerai de fer. La roche contenant du minerai de fer est concassée. Le minerai est extrait à l'aide de rouleaux magnétiques. Le minerai de fer à grains fins est transformé en morceaux à grains grossiers pour être utilisé dans un haut fourneau. Le charbon est raffiné dans un four à coke pour produire une forme presque pure de carbone. Le mélange de minerai de fer et de charbon est ensuite chauffé pour produire du fer fondu, ou de la fonte brute, à partir de laquelle l'acier est fabriqué.
Dans le four principal à oxygène, le minerai de fer en fusion est la principale matière première et est mélangé à diverses quantités de ferraille et d'alliages pour produire diverses nuances d'acier. Dans un four à arc électrique, la ferraille d'acier recyclée est fondue directement en acier neuf. Environ 12 % de l'acier est fabriqué à partir de matériaux recyclés.
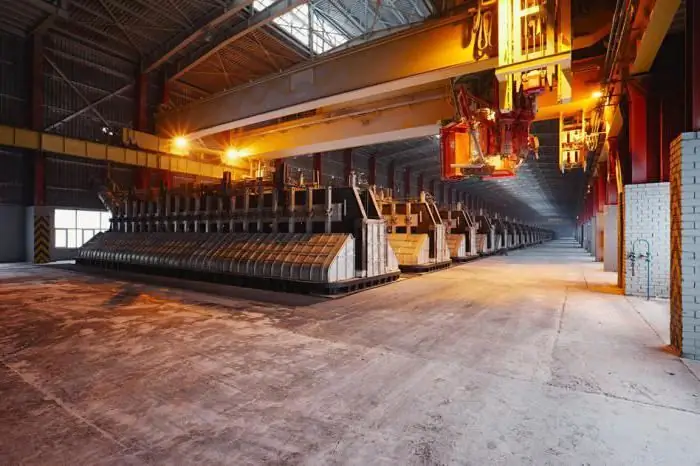
Technologie de fusion
La fusion est un processus par lequel un métal est obtenu soit sous la forme d'un élément,soit sous forme de simple composé à partir de son minerai par chauffage au-dessus de son point de fusion, généralement en présence d'agents oxydants tels que l'air ou d'agents réducteurs tels que le coke.
Dans la technologie sidérurgique, le métal qui est combiné avec de l'oxygène, tel que l'oxyde de fer, est chauffé à une température élevée, et l'oxyde est formé en combinaison avec du carbone dans le combustible, qui est libéré sous forme de monoxyde de carbone ou de carbone dioxyde. D'autres impuretés, appelées collectivement veines, sont éliminées en ajoutant un flux avec lequel elles se combinent pour former des scories.
La sidérurgie moderne utilise un four à réverbère. Le minerai concentré et le flux (généralement du calcaire) sont chargés par le haut, tandis que la matte fondue (composé de cuivre, de fer, de soufre et de laitier) est tirée par le bas. Un deuxième traitement thermique dans un four convertisseur est nécessaire pour éliminer le fer de la finition mate.
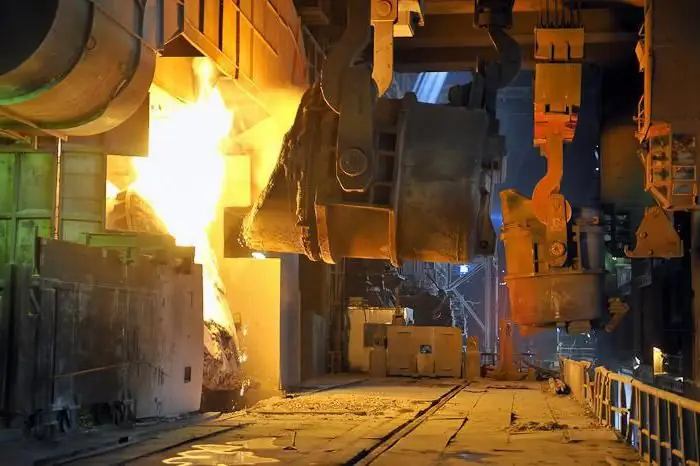
Méthode oxygène-convecteur
Le procédé BOF est le premier procédé de fabrication d'acier au monde. La production mondiale d'acier de conversion en 2003 s'élevait à 964,8 millions de tonnes, soit 63,3 % de la production totale. La production de convertisseurs est une source de pollution de l'environnement. Les principaux problèmes en sont la réduction des émissions, des rejets et la réduction des déchets. Leur essence réside dans l'utilisation de ressources énergétiques et matérielles secondaires.
La chaleur exothermique est générée par les réactions d'oxydation lors de la purge.
Le processus principal de fabrication de l'acier en utilisant notre propreactions:
- Le fer en fusion (parfois appelé métal chaud) d'un haut fourneau est versé dans un grand récipient doublé de réfractaire appelé louche.
- Le métal dans la poche est envoyé directement vers l'étape principale de production d'acier ou de prétraitement.
- De l'oxygène de haute pureté à une pression de 700 à 1000 kilopascals est injecté à une vitesse supersonique sur la surface du bain de fer à travers une lance refroidie à l'eau qui est suspendue dans un récipient et maintenue à quelques pieds au-dessus du bain.
La décision de prétraitement dépend de la qualité de la fonte et de la qualité d'acier finale souhaitée. Les tout premiers convertisseurs à fond amovible démontables et réparables sont encore en usage. Les lances utilisées pour souffler ont été modifiées. Pour éviter le coincement de la lance pendant le soufflage, des colliers à fentes avec une longue pointe en cuivre effilée ont été utilisés. Les pointes de la pointe, après combustion, brûlent le CO formé lors du soufflage en CO2 et fournissent un complément de chaleur. Des fléchettes, des billes réfractaires et des détecteurs de scories sont utilisés pour éliminer les scories.
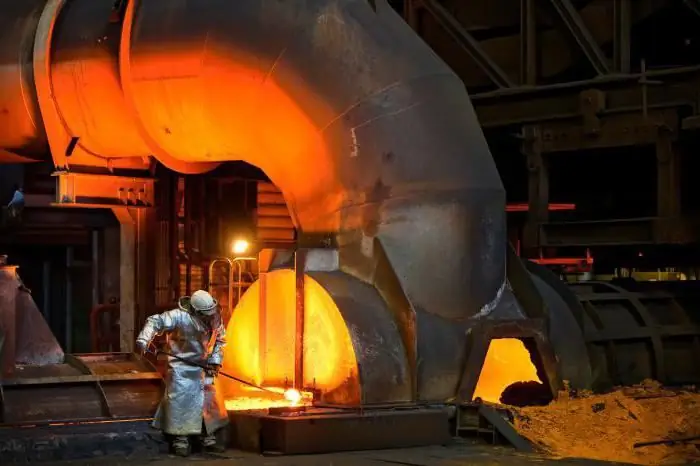
Méthode oxygène-convecteur: avantages et inconvénients
Ne nécessite pas le coût d'un équipement de purification de gaz, car la formation de poussière, c'est-à-dire l'évaporation du fer, est réduite de 3 fois. En raison de la diminution du rendement en fer, une augmentation du rendement en acier liquide de 1,5 à 2,5% est observée. L'avantage est que l'intensité de soufflage dans cette méthode augmente, ce qui donnela possibilité d'augmenter les performances du convertisseur de 18%. La qualité de l'acier est meilleure car la température dans la zone de purge est plus basse, ce qui entraîne moins de formation d'azote.
Les lacunes de cette méthode de fusion de l'acier ont entraîné une diminution de la demande de consommation, car le niveau de consommation d'oxygène augmente de 7 % en raison de la forte consommation de carburant. Il y a une augmentation de la teneur en hydrogène dans le métal recyclé, c'est pourquoi il faut un certain temps après la fin du processus pour effectuer une purge à l'oxygène. Parmi toutes les méthodes, le convertisseur d'oxygène a la formation de laitier la plus élevée, la raison en est l'incapacité de surveiller le processus d'oxydation à l'intérieur de l'équipement.
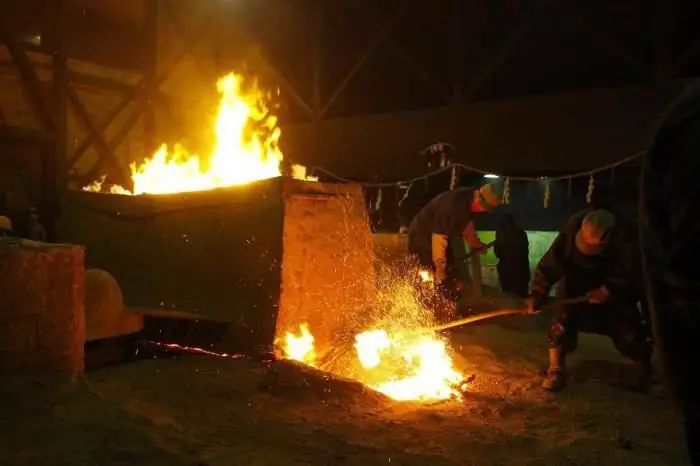
Méthode à foyer ouvert
Le procédé à foyer ouvert pendant la majeure partie du 20e siècle a été la partie principale du traitement de tout l'acier fabriqué dans le monde. William Siemens, dans les années 1860, a cherché un moyen d'élever la température dans un four métallurgique, ressuscitant une ancienne proposition d'utiliser la chaleur résiduelle générée par le four. Il a chauffé la brique à haute température, puis a utilisé le même chemin pour introduire de l'air dans le four. L'air préchauffé a augmenté la température de la flamme de manière significative.
Le gaz naturel ou les huiles lourdes atomisées sont utilisés comme carburant; l'air et le carburant sont chauffés avant la combustion. Le four est chargé de fonte liquide et de ferraille d'acier ainsi que de minerai de fer, de calcaire, de dolomie et de fondants.
Le poêle lui-même est fait dematériaux hautement réfractaires tels que les briques de foyer en magnésite. Les fours à foyer ouvert pèsent jusqu'à 600 tonnes et sont généralement installés en groupes, de sorte que l'équipement auxiliaire massif nécessaire pour charger les fours et traiter l'acier liquide peut être utilisé efficacement.
Bien que le procédé à foyer ouvert ait été presque entièrement remplacé dans la plupart des pays industrialisés par le procédé de base à l'oxygène et le four à arc électrique, il représente environ 1/6 de tout l'acier produit dans le monde.
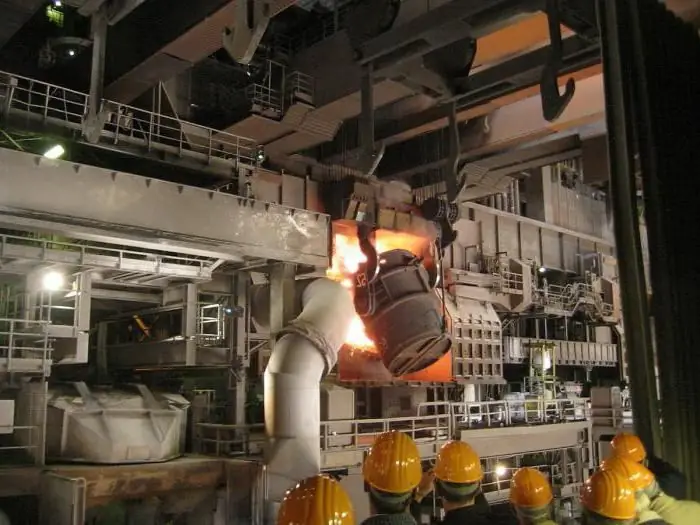
Avantages et inconvénients de cette méthode
Les avantages incluent la facilité d'utilisation et la facilité de production de l'acier allié avec divers additifs qui confèrent au matériau diverses propriétés spécialisées. Les additifs et alliages nécessaires sont ajoutés immédiatement avant la fin de la fusion.
Les inconvénients incluent une efficacité réduite par rapport à la méthode du convertisseur d'oxygène. En outre, la qualité de l'acier est inférieure à celle des autres méthodes de fusion des métaux.
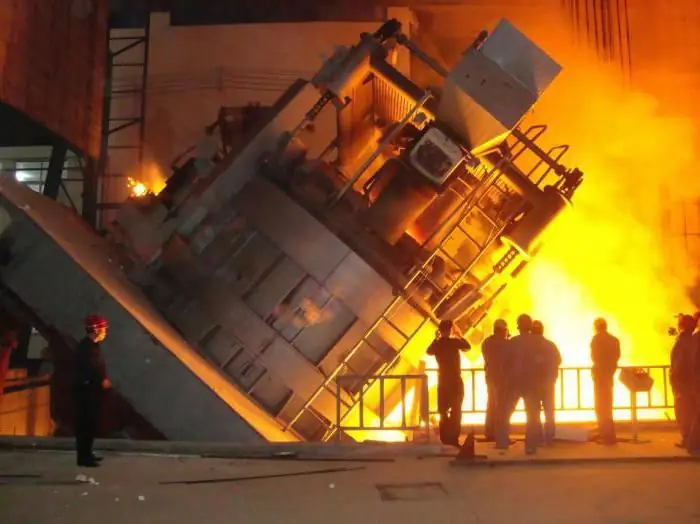
Méthode de fabrication de l'acier électrique
La méthode moderne de fusion de l'acier en utilisant nos propres réserves est un four qui chauffe un matériau chargé avec un arc électrique. Les fours à arc industriels varient en taille depuis de petites unités d'une capacité d'environ une tonne (utilisées dans les fonderies pour la production de produits sidérurgiques) jusqu'à des unités de 400 tonnes utilisées dans la métallurgie secondaire.
Fours à arc,utilisés dans les laboratoires de recherche peuvent avoir une capacité de quelques dizaines de grammes seulement. Les températures des fours à arc électriques industriels peuvent atteindre jusqu'à 1 800 °C (3 272 °F), tandis que les installations de laboratoire peuvent dépasser 3 000 °C (5 432 °F).
Les fours à arc diffèrent des fours à induction en ce que le matériau de charge est directement exposé à un arc électrique et que le courant dans les bornes traverse le matériau chargé. Le four à arc électrique est utilisé pour la production d'acier, se compose d'un revêtement réfractaire, généralement refroidi à l'eau, de grande taille, recouvert d'un toit rétractable.
Le four est principalement divisé en trois sections:
- Coque composée de parois latérales et d'une cuve inférieure en acier.
- Le foyer est constitué d'un réfractaire qui sort la cuvette inférieure.
- Le toit à revêtement réfractaire ou refroidi à l'eau peut être réalisé en section sphérique ou en tronc de cône (section conique).
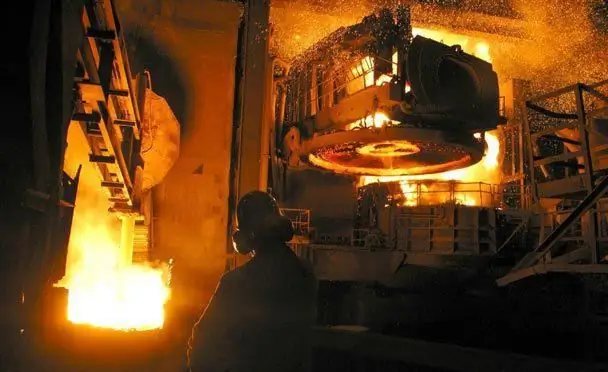
Avantages et inconvénients de la méthode
Cette méthode occupe une position de leader dans le domaine de la production d'acier. La méthode de fusion de l'acier est utilisée pour créer un métal de haute qualité qui est complètement dépourvu ou contient une petite quantité d'impuretés indésirables telles que le soufre, le phosphore et l'oxygène.
Le principal avantage de la méthode est l'utilisation de l'électricité pour le chauffage, ce qui vous permet de contrôler facilement la température de fusion et d'obtenir une vitesse de chauffage incroyable du métal. Le travail automatisé deviendraun ajout agréable à l'excellente opportunité de traitement de haute qualité de divers déchets métalliques.
Les inconvénients incluent une forte consommation d'énergie.
Conseillé:
Obtention des alcools : méthodes et matières premières
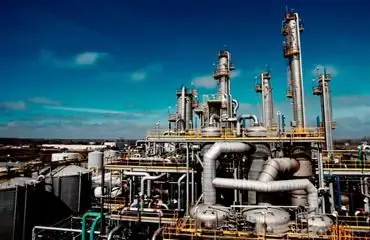
L'obtention d'alcools est un processus technologique assez compliqué. Il existe des méthodes biochimiques et chimiques pour obtenir des alcools. L'obtention d'alcool méthylique est réalisée grâce à l'utilisation de diverses technologies
Science des matières premières : méthodes de buts et d'objectifs
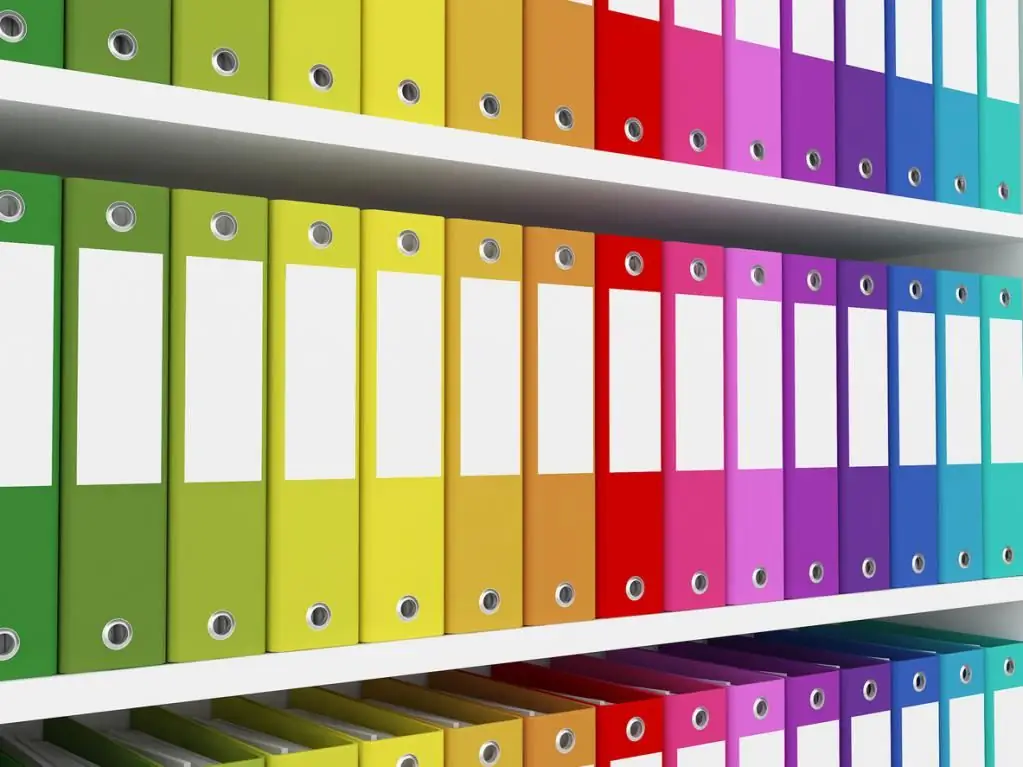
Grâce aux méthodes modernes de recherche sur les matières premières, ses principales tâches sont résolues. Les méthodes de recherche sur les produits aident à rechercher des moyens d'améliorer la qualité des produits, à effectuer un examen, à choisir les modes de fonctionnement, d'emballage et de transport optimaux. En d'autres termes, faire tout ce qui requiert la science marchande en tant que science et outil économique
Production de mousse polyuréthane : technologie, matières premières, équipements
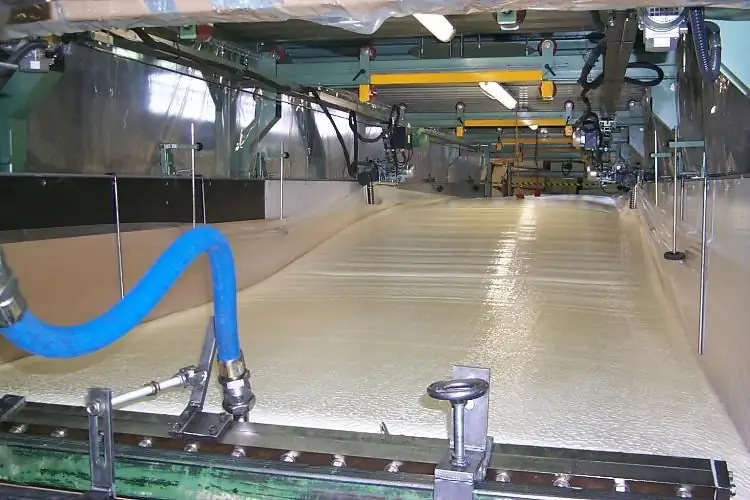
La mousse de montage des moyens habituels de scellement des ouvertures de fenêtre est depuis longtemps devenue un matériau de construction à part entière, largement utilisé dans une variété de types de travaux. La variété des applications de ce produit détermine également la nécessité d'une approche différenciée des technologies de sa fabrication. Cependant, les différences dans les méthodes de production de la mousse de polyuréthane sont plutôt de nature cosmétique, sans affecter les processus technologiques de base
Production de tuyaux en PVC : technologie, matières premières et équipement
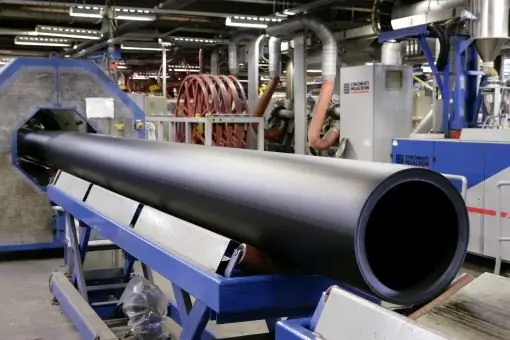
Les produits tubulaires à base de chlorure de polyvinyle (PVC) sont largement utilisés aujourd'hui dans une variété de domaines et d'industries, du secteur privé aux grandes entreprises pétrolières et gazières. Mais le processus de consolidation sur le marché a été progressif, car les propriétés physiques et techniques du matériau polymère sont inférieures à celles de ses homologues métalliques traditionnels sur un certain nombre de critères. Cependant, la production moderne de tuyaux en PVC, grâce à l'introduction de technologies avancées, a considérablement augmenté les performances des produits
440 acier - acier inoxydable. Acier 440 : caractéristiques
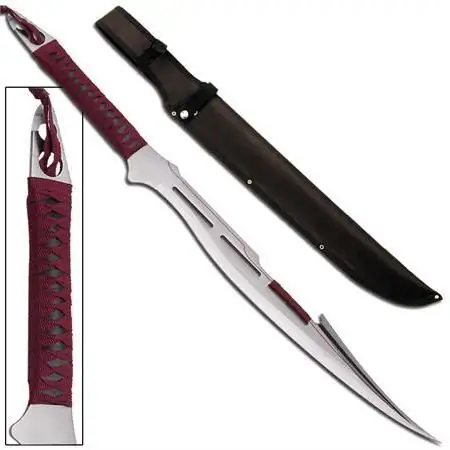
Beaucoup de gens connaissent l'acier 440. Il s'est imposé comme un matériau dur fiable, anticorrosion et éprouvé dans le temps, qui est le plus souvent utilisé pour la fabrication de couteaux à diverses fins. Quel est le secret de cet alliage ? Quelles sont ses caractéristiques chimiques, physiques et ses applications ?