2025 Auteur: Howard Calhoun | [email protected]. Dernière modifié: 2025-01-24 13:16
Le système de gestion Kanban est une méthodologie logistique d'organisation des entreprises industrielles. La facilité de mise en œuvre, la capacité d'économiser considérablement les ressources matérielles et une augmentation du niveau global de contrôle ont contribué à sa popularité et à sa popularité.
Histoire de la création et du développement
L'origine du système Kanban est considérée comme étant le Japon, où il a été utilisé pour la première fois à l'usine automobile Toyota Motors au début des années 60. Le développement et la mise en œuvre étaient directement liés à la nécessité de minimiser les pertes financières grâce à un contrôle "instantané" des stocks et à l'exécution en temps voulu des tâches requises. A ce jour, le principal domaine d'application est la production industrielle, notamment avec des cycles de production continus (industrie automobile, transport ferroviaire, etc.). Compte tenu de la simplicité de l'algorithme intégré à la méthode considérée, ces dernières années, il s'agit de l'une des approches les plus efficaces de la gestion de projet.
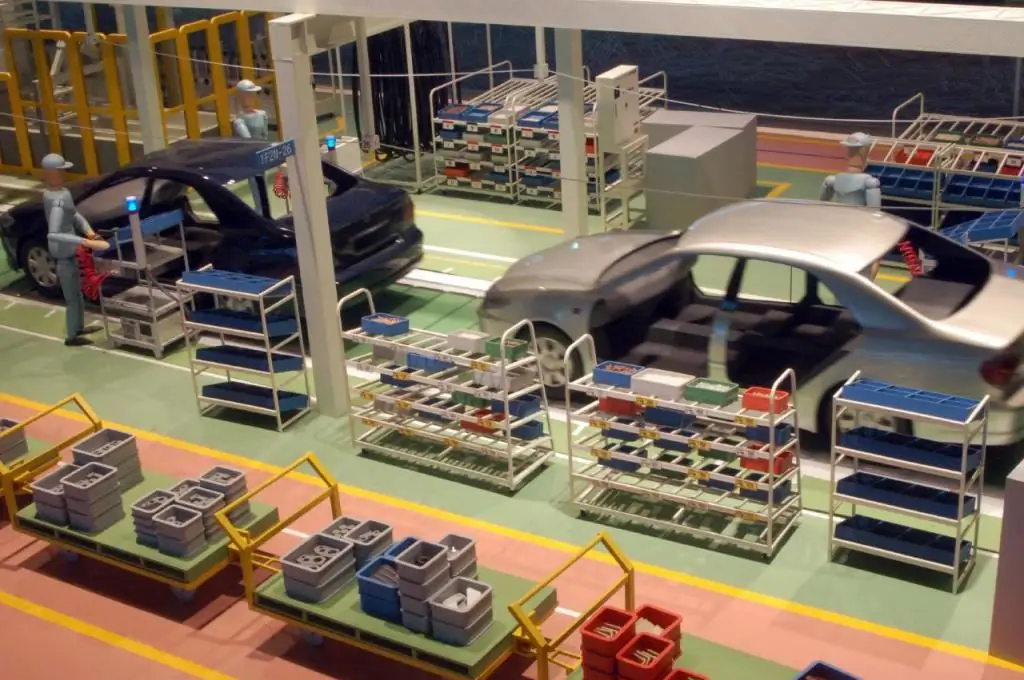
Pousser ou tirer ?
Kanban est né à la suite de l'amélioration de l'entreprise juste à temps pour réduire les déchets et améliorer la qualité des produits. En même temps, sa création et son utilisation ultérieure ont ouvert un nouveau type de gestion. Si jusqu'au milieu du XXe siècle, les efforts des chercheurs visaient principalement à améliorer les mécanismes de production push (c'est-à-dire ceux qui fonctionnent selon un plan strict), alors à partir du moment où le système Kanban a été appliqué, des entreprises de type pull sont apparues. en logistique. Dans ce cas, la direction du flux d'informations change.
Dans les magasins de type push, le signal de commande va de gauche à droite, "poussant" en fait le produit d'une zone à une autre selon la technologie acceptée. Pour les extracteurs, la dernière section génère une demande pour les composants nécessaires des étapes précédentes de la production.
Le système de production Kanban n'est pas un tout nouveau type de production. Au sens strict, les modèles de gestion de la production qui ont émergé au cours du dernier demi-siècle représentent des superstructures pour les entreprises industrielles classiques. Le terme le plus précis pour les capacités Kanban est "efficacité". Puisque les méthodes progressives de modernisation de la production visent à l'augmenter.
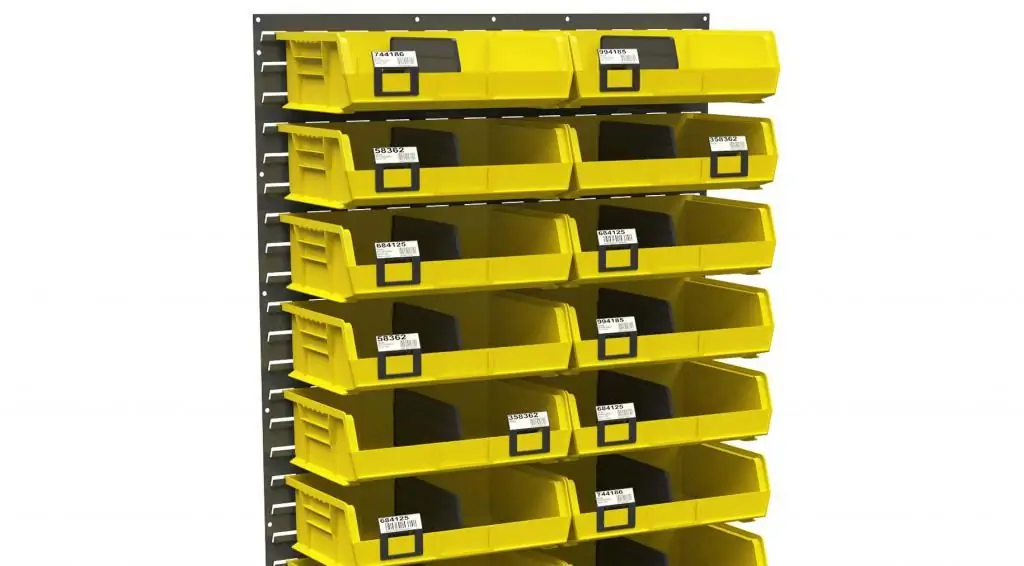
Quelle est la différence ?
L'essence du système Kanban est d'organiser la bonne exécution des tâches de production à tous les postes de travail (lieux) de la productiontraiter. Les caractéristiques distinctives sont la minimisation des stocks à toutes les étapes du cycle de vie du produit.
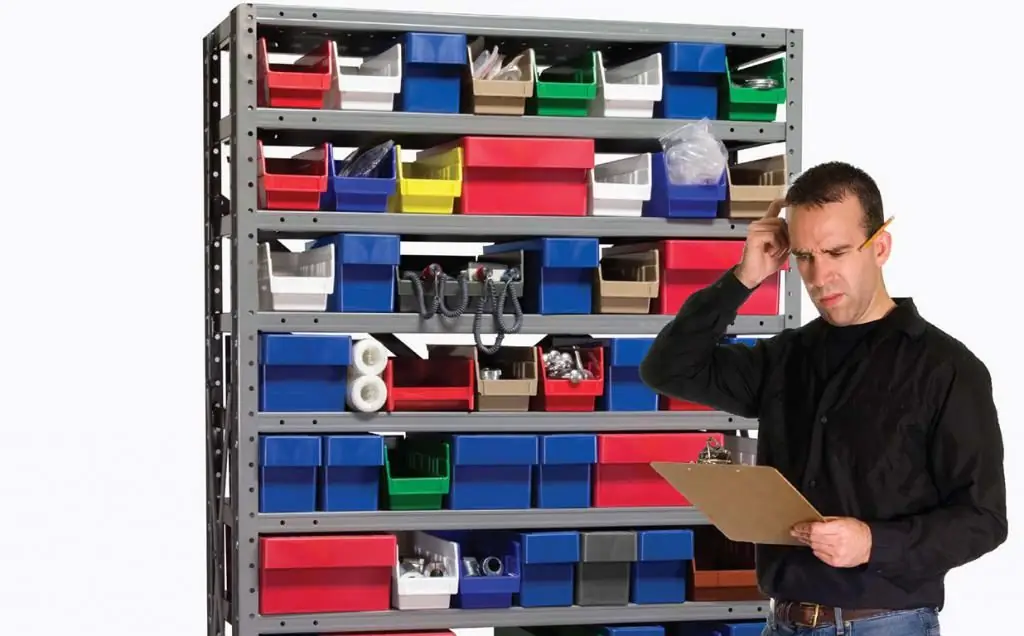
Les stocks de matériaux sont l'un des goulots d'étranglement de la production moderne. En pratique, l'une des options suivantes est très susceptible de se produire:
- inventaire insuffisant;
- réserve de stock.
Les conséquences du développement du premier scénario seront:
- interruptions du rythme de production;
- diminution de la production des employés;
- augmentation du nombre de pièces de rechange et de composants en raison d'une maintenance tardive;
- augmentation des coûts de fabrication.
Pour la seconde option, les traits caractéristiques sont:
- faible rotation;
- diminution de la production;
- augmentation des pertes sur les infrastructures de support (espace de stockage, personnel, services publics).
Le système Kanban réduit les risques des deux scénarios en raison des restrictions acceptées sur la quantité autorisée de ressources dans la chaîne de production. En conséquence, la «transparence» des processus apparaît - les interruptions dans le fonctionnement des équipements, le montant réel du mariage, le débit réel des lieux de travail sont visibles. Le résultat de l'introduction du système est une augmentation de la qualité des produits dans le contexte d'une réduction significative des coûts.
Éléments clés du système
"Kanban" est le contrôle des processus de production à l'aide de signaux de contrôle spéciaux. Notez que pour une efficacitéle fonctionnement nécessite une infrastructure développée d'interaction entre les composants structurels de la production, une technologie de fabrication sophistiquée, un travail d'équipe du personnel. Le principal élément d'information dans la chaîne de production était des cartes en plastique de différentes couleurs avec des informations différentes (le sens de "Kanban" du japonais est "carte"). Son apparence dépend du type de contrôle.
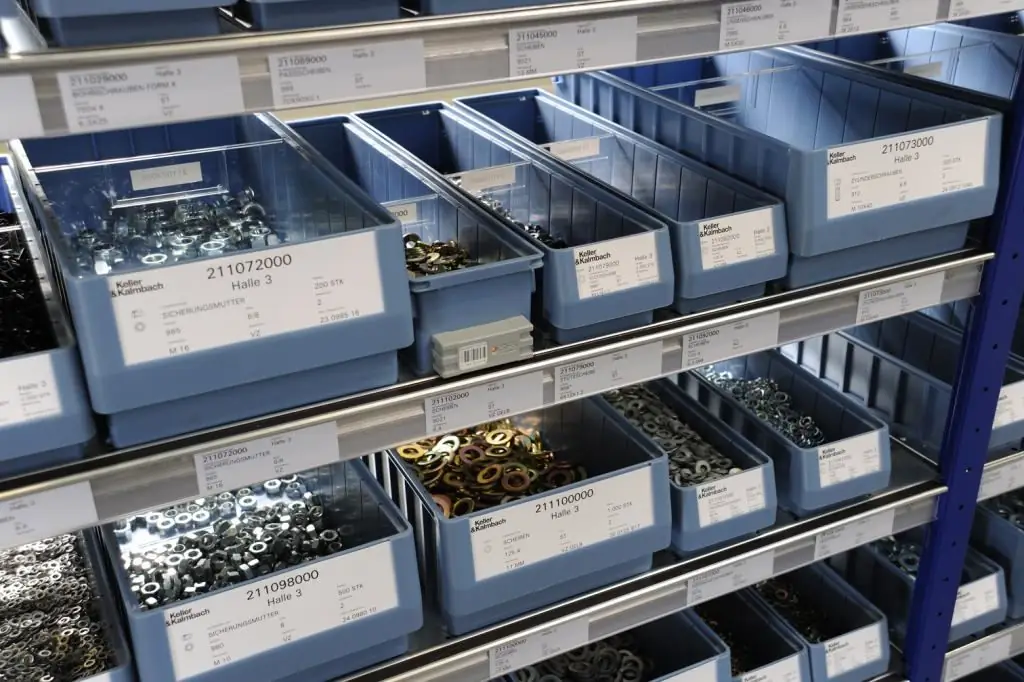
Tare Kanban
La carte de données est montée sur le conteneur. L'ordre de fabrication est déterminé par la position du conteneur lui-même sur le rack. L'algorithme de commande s'effectue comme suit: lorsque le nombre de pièces dans le premier conteneur avec la carte diminue, il est déplacé de la position de travail vers l'un des niveaux du rack (qui sert à passer des commandes et à recevoir un signal du employé du service de transport) et commence à travailler avec un autre. Le transporteur récupère un conteneur vide, la présence d'une carte kanban sur laquelle indique la nécessité de commander du matériel auprès d'un magasinier ou d'un fournisseur. Le principal inconvénient de ce type de kanban est la quantité supplémentaire d'emballages pour chaque type de pièce utilisée.
Carte Kanban
Carte multicolore avec des informations sur la production, la couleur détermine les paramètres spatiaux des fournitures nécessaires. En pratique, la carte est divisée en plusieurs segments qui affichent des informations sur l'expéditeur et le destinataire.
Il existe différents schémas d'utilisation de la palette de couleurs des cartes. Du monochrome (blanc, noir) au multicolore. Le nombre de couleurs et leur choix dépendent decomplexité des procédés de fabrication. S'il est nécessaire d'utiliser des signaux entre différentes zones fonctionnelles de travail, le schéma suivant peut être proposé:
- couleur bleue - "production kanban" (connexion entre la zone de travail et la zone d'approvisionnement);
- couleur rouge - "warehouse kanban" (connexion entre l'entrepôt et la zone de ramassage);
- couleur verte - "cross-shop kanban" (communication entre différents magasins ou complexes).
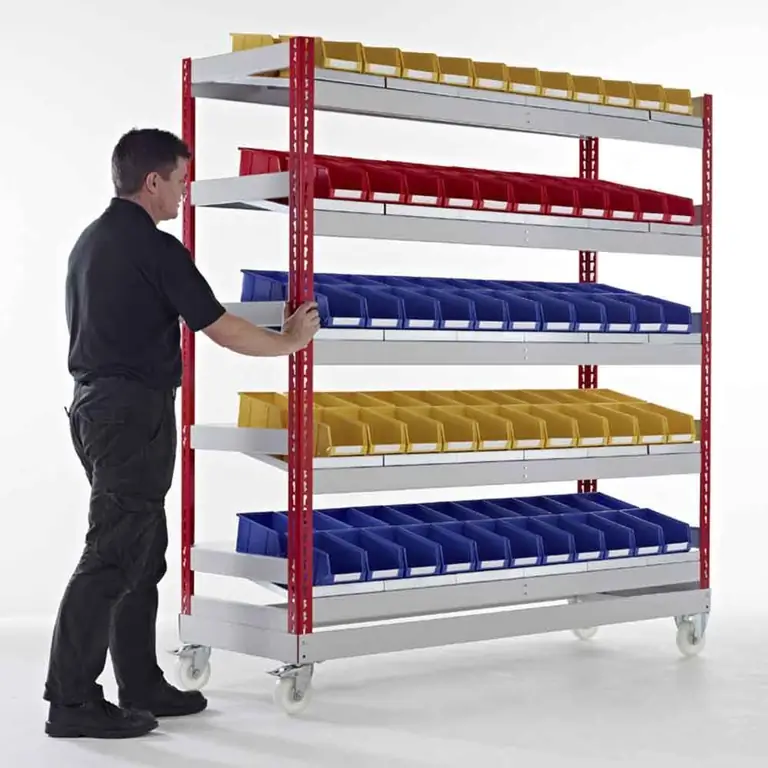
Pour et contre
Le système Kanban présente un certain nombre d'avantages par rapport aux méthodes traditionnelles de gestion de la production. Ceci est confirmé par les commentaires des employés. Il réduit les délais, réduit les temps d'arrêt des équipements, optimise les stocks, réduit les rebuts, élimine les WIP, améliore l'utilisation de l'espace, augmente la productivité et augmente la flexibilité globale de l'usine. Dans le même temps, les limites de la méthode sont inévitables - il est nécessaire de créer une chaîne d'approvisionnement fiable des stocks, il n'y a aucune possibilité de planification à long terme des tâches de production. Selon les responsables, la synchronisation des actions des employés de divers services est très exigeante.
En conclusion, le système Kanban n'est pas seulement une méthode d'amélioration des processus, c'est une philosophie de production qui, avec une utilisation systématique et constante, permet d'atteindre des performances élevées de l'entreprise.
Conseillé:
Classification des fonctions de gestion : définition du concept, de l'essence et des fonctions
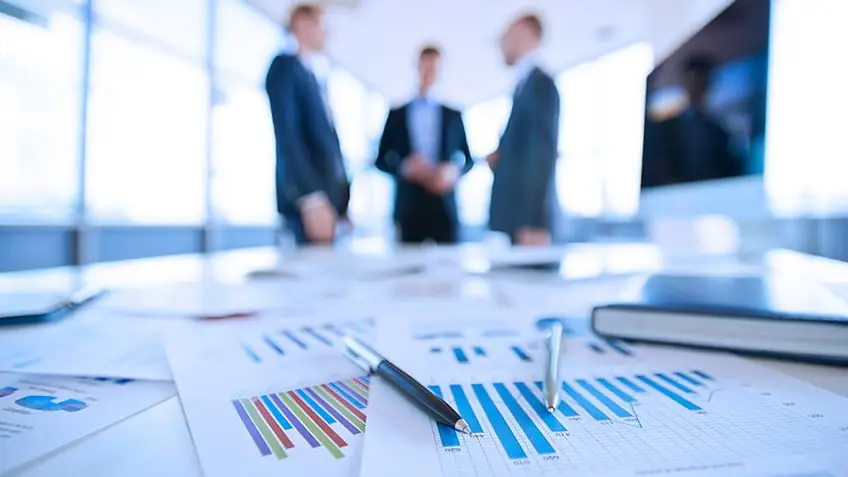
La gestion est un processus complexe et multiforme. Pourquoi est-il nécessaire et quelle est son essence ? Parlons du concept et de la classification des fonctions de contrôle, considérons les approches de ce problème et caractérisons les principales fonctions
Gestion centralisée : système, structure et fonctions. Principes du modèle de gestion, avantages et inconvénients du système
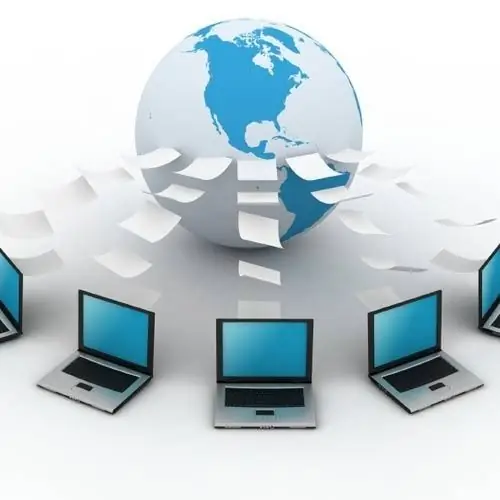
Quel modèle de gestion est le meilleur : centralisé ou décentralisé ? Si quelqu'un en réponse pointe l'un d'entre eux, il est mal versé dans la gestion. Parce qu'il n'y a pas de mauvais et de bons modèles en management. Tout dépend du contexte et de son analyse compétente, qui permet de choisir la meilleure façon de gérer l'entreprise ici et maintenant. La gestion centralisée en est un excellent exemple
Métiers du système "homme - système de signes". Liste et description des métiers
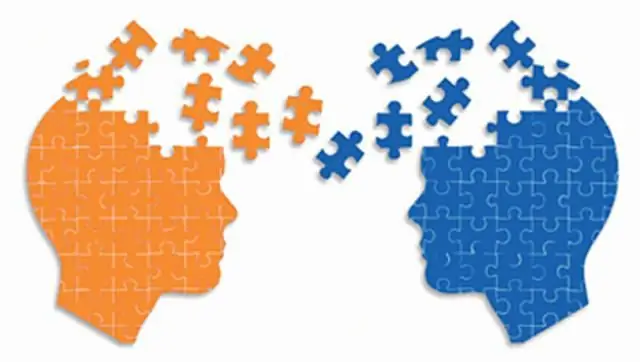
Lors du choix d'un futur métier, il est préférable de se concentrer sur le classificateur du professeur Klimov. Sur cette base, toutes les spécialités sont divisées en certains systèmes. Une place importante parmi eux est occupée par les professions du système "homme - système de signes"
95 essence. Le coût de 95 essence. Essence 95 ou 92
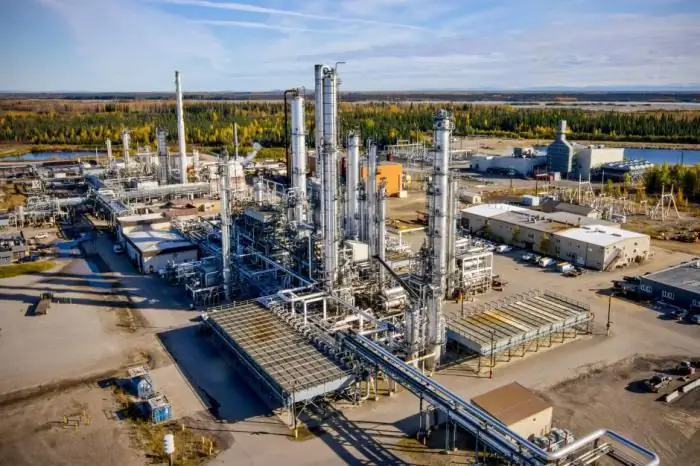
Il semblerait qu'il y ait quelque chose d'intéressant dans une substance comme l'essence ? Mais aujourd'hui, vous apprendrez tous ces faits intéressants qui vous étaient auparavant inconnus. Alors, essence 95 - quelle est la particularité de ce liquide?
Système de missiles anti-aériens. Système de missiles anti-aériens "Igla". Système de missiles anti-aériens "Osa"
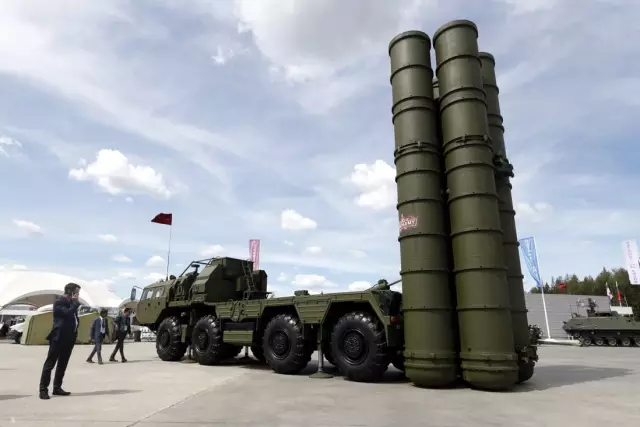
La nécessité de créer des systèmes de missiles anti-aériens spécialisés était mûre pendant la Seconde Guerre mondiale, mais les scientifiques et les armuriers de différents pays n'ont commencé à aborder la question en détail que dans les années 50. Le fait est que jusque-là, il n'y avait tout simplement aucun moyen de contrôler les missiles intercepteurs