2025 Auteur: Howard Calhoun | [email protected]. Dernière modifié: 2025-01-24 13:16
Le chef d'entreprise, quel que soit son domaine d'activité, rêve que les bénéfices augmentent et que les coûts de production restent inchangés. Le système "5S" en production (dans la version anglaise 5S), qui repose uniquement sur l'utilisation rationnelle des réserves internes, permet d'atteindre ce résultat.
Ce système n'a pas été créé à partir de zéro. Quelque chose de similaire à la fin du XIXe siècle a été proposé par l'Américain Frederick Taylor. En Russie, cela a été fait par le scientifique, révolutionnaire, philosophe et idéologue A. A. Bogdanov, qui a publié un livre sur les principes de la gestion scientifique en 1911. Sur la base des dispositions qui y sont énoncées, l'URSS a introduit le NOT, c'est-à-dire l'organisation scientifique du travail. Mais le plus parfait était le système 5C proposé par l'ingénieur japonais Taiichi Ohno et introduit par lui à l'usine Toyota Motor en production. De quoi s'agit-il et pourquoi le système japonais est-il devenu si populaire ?
Le fait est qu'il est basé sur un principe simple qui ne nécessite pas de frais. Il consiste àle suivant - chaque employé, du nettoyeur au directeur, doit optimiser autant que possible sa part dans le flux de travail global. Cela conduit à une augmentation du profit de la production dans son ensemble et à une augmentation du revenu de tous ses employés. Aujourd'hui, le relais de l'introduction du système "5C" a été repris par des entreprises du monde entier, y compris la Russie. Dans cet article, nous allons tenter de convaincre les sceptiques que le savoir-faire japonais fonctionne vraiment, et dans absolument tous les domaines d'activité.
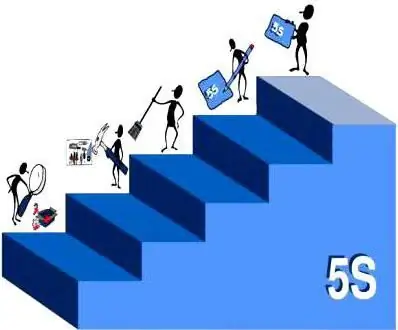
Le système "5C" en production, qu'est-ce que c'est
International 5S signifie cinq étapes ("step" en anglais step). Certains économistes et promoteurs d'une nouvelle attitude au travail expliquent le nom par les cinq postulats japonais qui sont systématiquement mis en œuvre dans le système 5S: seiri, seiton, seiso, seiketsu et shitsuke. Pour nous, nos "5C" natifs sont plus proches et plus compréhensibles - cinq étapes consécutives qui doivent être complétées pour atteindre la prospérité de notre production. C'est:
1. Trier.
2. Garder l'ordre.
3. Rester propre.
4. Normalisation.
5. Amélioration.
Comme vous pouvez le voir, le système "5C" ne nécessite rien de surnaturel en production. C'est peut-être pour cela que l'on peut encore rencontrer de la méfiance et une attitude frivole à son égard.
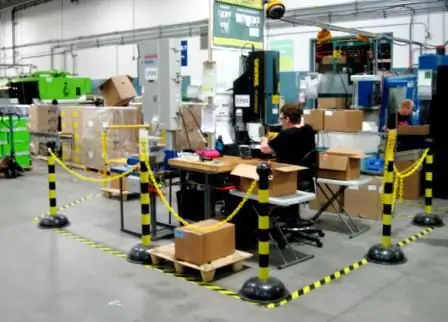
Étapes de création d'un système
Le sage japonais Taiichi Ohno, qui, grâce à l'introduction de ses méthodes à l'usine Toyota, a réussi à passer deingénieur à PDG, a remarqué combien de pertes se produisent en raison de diverses incohérences et superpositions. Par exemple, certaines petites vis n'ont pas été placées à temps sur le convoyeur et, par conséquent, toute la production s'est arrêtée. Ou inversement, les pièces étaient fournies avec une marge, elles se sont avérées superflues, et du coup, l'un des employés a dû les ramener à l'entrepôt, ce qui signifie perdre son temps en travail à vide. Taiichi Ohno a développé un concept qu'il a appelé "juste à temps". Autrement dit, exactement autant de pièces que nécessaire étaient désormais livrées au convoyeur.
D'autres exemples pourraient être donnés. Le système « 5S » en production comprenait également le concept de « kanban », qui signifie en japonais « enseigne publicitaire ». Taiichi Ohno a proposé d'apposer sur chaque pièce ou chaque outil une étiquette dite « kanban », dans laquelle toutes les informations nécessaires sur la pièce ou l'outil étaient données. En gros, ça s'applique à tout. Par exemple, aux marchandises, aux médicaments, aux dossiers au bureau. Le troisième concept sur lequel repose le système 5S en production est le concept de "kaizen", qui signifie amélioration continue. D'autres concepts ont également été conçus, qui ne convenaient qu'aux processus de production hautement spécialisés. Dans cet article, nous ne les considérerons pas. À la suite de toutes les innovations testées dans la pratique, 5 étapes ont été formées qui sont applicables à toute production. Analysons-les en détail.
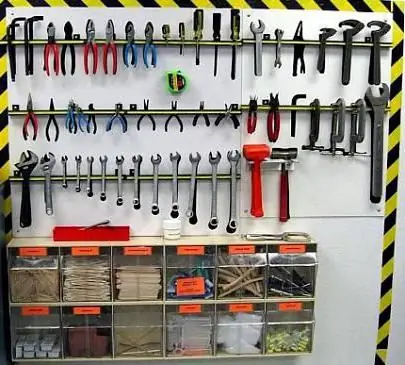
Tri
Beaucoup d'entre nous ont des éléments sur nos ordinateurs qui, enfondamentalement pas nécessaire. Par exemple, d'anciens formulaires, des dossiers inutilisés, des brouillons de calculs, une serviette sur laquelle il y avait une tasse de café. Et parmi ce chaos, il peut y avoir les fichiers ou documents nécessaires. Les principes de base du système « 5S » consistent à optimiser votre flux de travail, c'est-à-dire à vous assurer que le temps n'est pas perdu à chercher les bonnes choses parmi les décombres de l'inutile. C'est le tri. Autrement dit, sur le lieu de travail (près de la machine, sur la table, dans l'atelier - n'importe où), tous les articles sont disposés en deux piles - le nécessaire et l'inutile, qui doivent être éliminés. De plus, tout ce dont vous avez besoin est décomposé en piles suivantes: "utilisé souvent et constamment", "utilisé rarement", "presque pas utilisé". Ceci termine le tri.
Garder l'ordre
Si vous démontez simplement les éléments, cela n'aura aucun sens. Il est nécessaire de ranger ces éléments (outils, documents) dans un ordre tel que ce qui est utilisé constamment et souvent soit en vue, ou de sorte qu'il puisse être rapidement pris et remis facilement. Ce qui est rarement utilisé peut être envoyé quelque part dans une boîte, mais une étiquette kanban doit y être attachée afin qu'au bout d'un moment, elle puisse être retrouvée facilement et avec précision. Comme vous pouvez le voir, le système 5S sur le lieu de travail commence par les étapes les plus simples, mais en fait, il s'avère très efficace. Et en plus, cela améliore l'humeur et le désir de travailler.
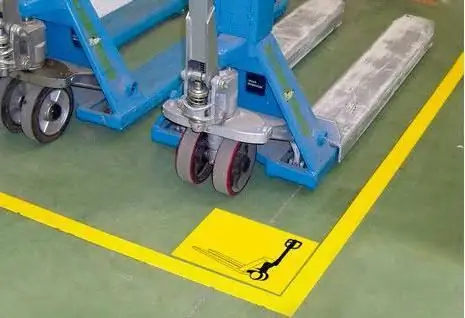
Garder propre
Cette troisième étape est la plus logique pour beaucoup. On nous apprend à être propre dès l'enfance. Sur leen production, il est également nécessaire, et non seulement les tables des employés de bureau ou les armoires des établissements de restauration, mais aussi les machines, les buanderies des nettoyeurs doivent être propres. Au Japon, les employés prennent bien soin de leurs lieux de travail, ils sont nettoyés trois fois par jour - le matin avant le travail, à midi et le soir, à la fin de la journée de travail. De plus, leurs entreprises ont introduit un marquage spécial des zones qui leur permettent de respecter l'ordre dans la production, c'est-à-dire que les zones de produits finis, de stockage de certaines pièces, etc. sont marquées de différentes couleurs.
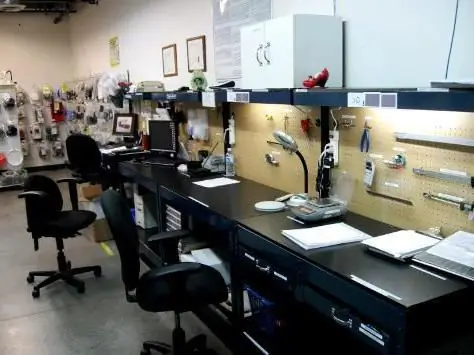
Normalisation
Les principes de normalisation ont été inventés par Taiichi Ohno. Ils sont également largement utilisés par le système 5S moderne. La gestion de la production, grâce à la standardisation, reçoit un formidable outil de contrôle de tous les processus. En conséquence, les causes des retards du calendrier sont rapidement éliminées et les erreurs qui conduisent à la sortie de produits de mauvaise qualité sont corrigées. À l'usine Toyota Motor, la standardisation ressemblait à ceci: des contremaîtres établissaient des plans de travail quotidiens, des instructions précises étaient affichées sur le lieu de travail et, à la fin de la journée de travail, des travailleurs spéciaux vérifiaient quels écarts par rapport au plan se produisaient au cours de la journée et pourquoi. C'est la règle de base de la normalisation, c'est-à-dire des instructions précises, des plans de travail et le contrôle de leur mise en œuvre. Aujourd'hui, de nombreuses entreprises, par exemple les usines ENSTO en Estonie, introduisent un système de primes pour les employés qui se conforment strictement aux dispositions du système 5C et, sur cette base, augmentent leur productivité, ce quiest une excellente incitation à adopter ce système comme mode de vie.
Amélioration
La cinquième étape, qui complète le système "5S" en production, est basée sur le concept de kaizen. Cela signifie que tous les employés, quel que soit leur poste, doivent s'efforcer d'améliorer le processus de travail dans le domaine qui leur est confié. L'essence philosophique du kaizen est que toute notre vie s'améliore chaque jour, et puisque le travail fait partie de la vie, il ne doit pas non plus rester à l'écart des améliorations.
Le champ d'activité ici est large, car la perfection n'a pas de limites. Selon les concepts des Japonais, les travailleurs eux-mêmes devraient vouloir améliorer leur processus de production, sans instructions ni coercition. Aujourd'hui, de nombreuses organisations constituent des équipes de travailleurs qui surveillent la qualité des produits, enseignent leur expérience positive aux autres et aident à atteindre l'excellence.
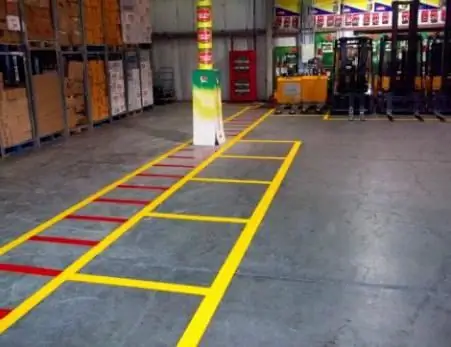
Erreurs de base
Pour que le système "5C" commence à fonctionner, il ne suffit pas de l'organiser ou d'embaucher des salariés qui obligeront leurs collègues à le mettre en place. Il est important que les gens réalisent l'utilité de cette innovation et l'acceptent comme mode de vie. L'introduction du système "5S" en Russie dans la production rencontre des difficultés précisément parce que notre mentalité russe est différente de celle des Japonais. Beaucoup de nos productions se caractérisent par les éléments suivants:
1. Les employés, surtout s'il n'y a pas d'incitations pour eux, ne cherchent pas à augmenter les bénéfices de l'entreprise. Ils demandent,pourquoi essayer de rendre le patron encore plus riche s'il a déjà tout.
2. Les dirigeants eux-mêmes ne sont pas intéressés par l'introduction du système "5S", car ils n'en voient pas l'opportunité.
3. De nombreuses directives "d'en haut" sont habituées à n'être exécutées que pour "cocher". Au Japon, il y a une attitude complètement différente vis-à-vis de leur travail. Par exemple, le même Taiichi Ohno, introduisant le système "5S", ne pensait pas au gain personnel, mais au bénéfice de l'entreprise dans laquelle il n'était qu'un ingénieur.
4. Dans de nombreuses entreprises, le système 5S est introduit de force. La production allégée, qui implique l'élimination des pertes de toutes sortes (temps de travail, matières premières, bons employés, motivation et autres indicateurs), ne fonctionne pas, car les travailleurs commencent à résister aux innovations à un niveau subconscient, ce qui réduit finalement tous les efforts à zéro.
5. Les responsables qui mettent en œuvre le système ne comprennent pas entièrement son essence, ce qui entraîne des défaillances dans les processus de production établis.
6. La normalisation se transforme souvent en bureaucratie, une bonne action est envahie d'instructions et de directives qui ne font qu'interférer avec le travail.
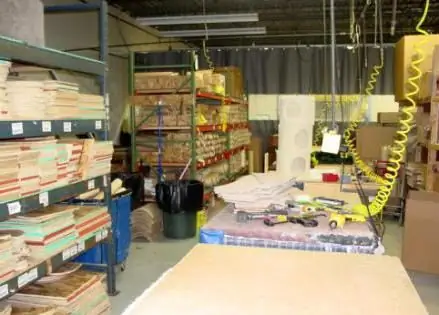
Avis
Russes qui ont introduit le système "5S" en production, les retours sur cette innovation sont très ambigus. Avantages mis en évidence:
- mieux vaut être au travail;
- ne pas distraire du travail avec de petites choses inutiles;
- flux de travail plus clair;
- la fatigue a diminué à la fin du quart de travail;
- légèrement augmentésalaire en augmentant la productivité du travail;
- les accidents du travail ont diminué.
Inconvénients:
- lors du tri, ils forcent tout à jeter;
- la standardisation a entraîné une augmentation de la bureaucratie;
- L'introduction du système "5C" n'a pas exacerbé les problèmes dans tous les domaines de l'entreprise;
- Placer le système 5S au premier plan a éclipsé des problèmes importants tels que le manque de pièces de rechange.
Conseillé:
Gestion centralisée : système, structure et fonctions. Principes du modèle de gestion, avantages et inconvénients du système
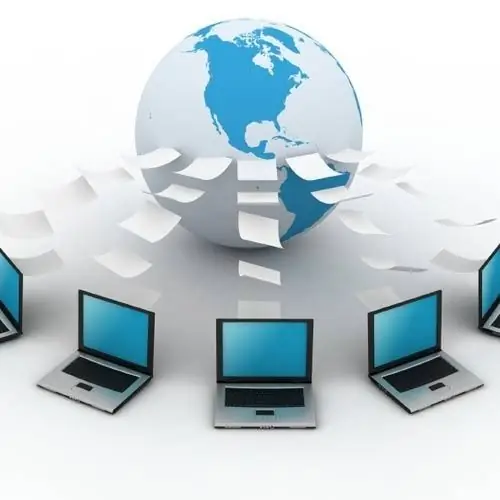
Quel modèle de gestion est le meilleur : centralisé ou décentralisé ? Si quelqu'un en réponse pointe l'un d'entre eux, il est mal versé dans la gestion. Parce qu'il n'y a pas de mauvais et de bons modèles en management. Tout dépend du contexte et de son analyse compétente, qui permet de choisir la meilleure façon de gérer l'entreprise ici et maintenant. La gestion centralisée en est un excellent exemple
Système de gestion hôtelière : aperçu des meilleurs programmes, fonctionnalités, description, avis
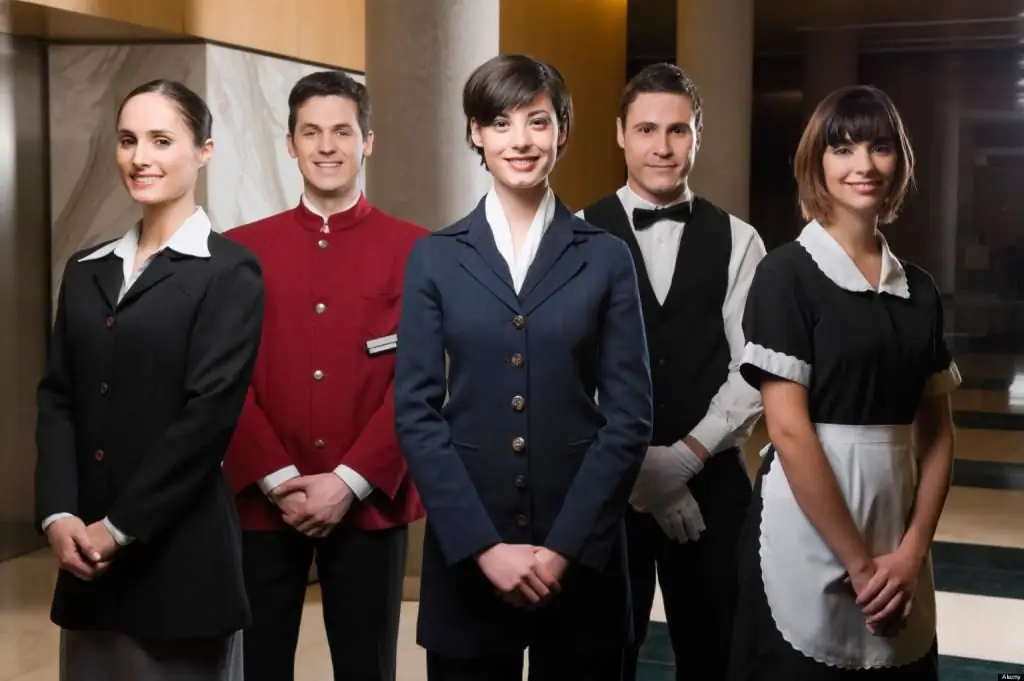
Le système de gestion hôtelière aidera à organiser correctement la maintenance de la documentation de l'établissement, à éliminer les erreurs. Description des meilleurs programmes et de leurs possibilités. Comment choisir un programme en fonction des caractéristiques de votre hôtel
Principes de construction d'un système fiscal. Système fiscal de la Fédération de Russie
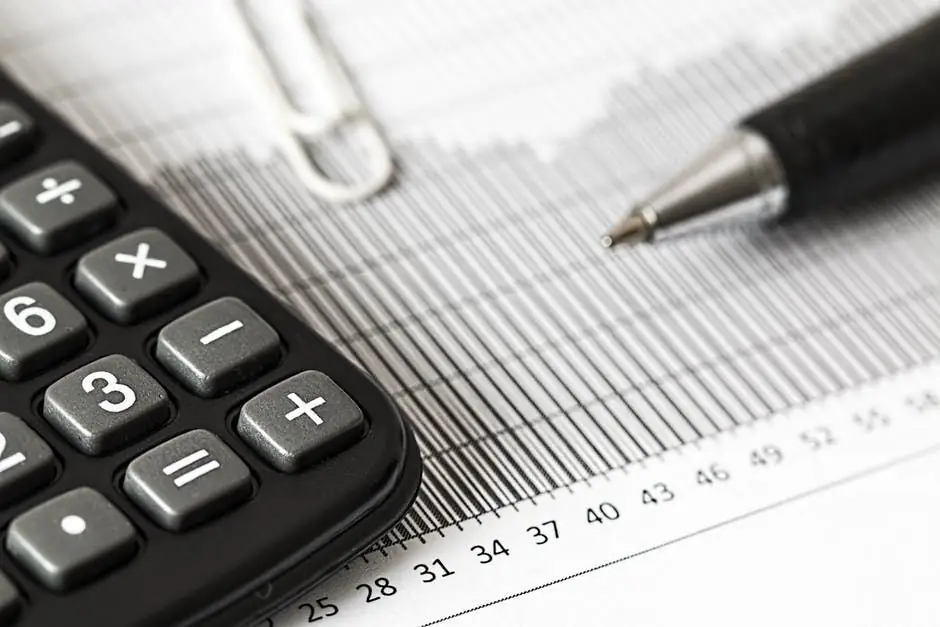
Dans le système fiscal, chacun de ses éléments - le payeur (personne morale ou physique) est tenu de payer un loyer ou un impôt. Cet article examinera les principes de construction d'un système fiscal ou certains exemples qui devraient être appliqués par rapport aux contribuables et à l'État
Système fiscal simplifié. Système de pari et fonctionnalités
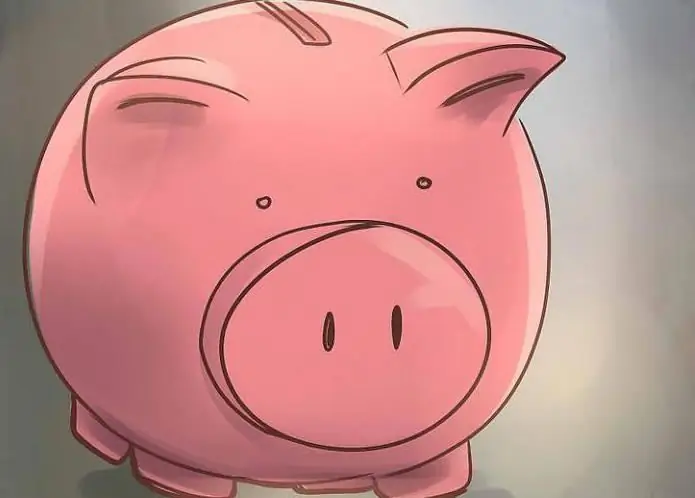
Le système de taux dans le cadre du système d'imposition simplifié pour les entrepreneurs individuels. Comment calculer le montant de l'impôt et quelles dépenses ne sont pas prises en compte dans le calcul du système "revenus moins dépenses"
Système de missiles anti-aériens. Système de missiles anti-aériens "Igla". Système de missiles anti-aériens "Osa"
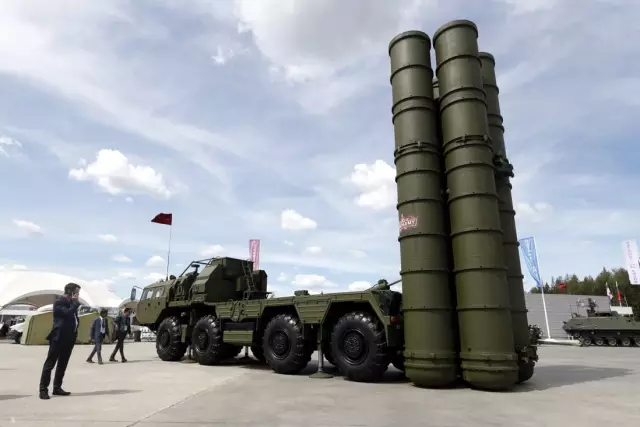
La nécessité de créer des systèmes de missiles anti-aériens spécialisés était mûre pendant la Seconde Guerre mondiale, mais les scientifiques et les armuriers de différents pays n'ont commencé à aborder la question en détail que dans les années 50. Le fait est que jusque-là, il n'y avait tout simplement aucun moyen de contrôler les missiles intercepteurs