2025 Auteur: Howard Calhoun | [email protected]. Dernière modifié: 2025-01-24 13:16
L'anodisation est un procédé électrolytique utilisé pour augmenter l'épaisseur de la couche d'oxydes naturels à la surface des produits. Cette technologie tire son nom du fait que le matériau traité est utilisé comme anode dans l'électrolyte. Grâce à cette opération, la résistance du matériau à la corrosion et à l'usure est augmentée et la surface est également préparée pour l'application d'apprêt et de peinture.
L'application de couches de protection supplémentaires après l'anodisation du métal est bien meilleure que le matériau d'origine. Le revêtement anodisé lui-même, selon la méthode d'application, peut être poreux, absorbant bien les colorants, ou mince et transparent, soulignant la structure du matériau d'origine et réfléchissant bien la lumière. Le film protecteur formé est un diélectrique, c'est-à-dire qu'il ne conduit pas le courant électrique.
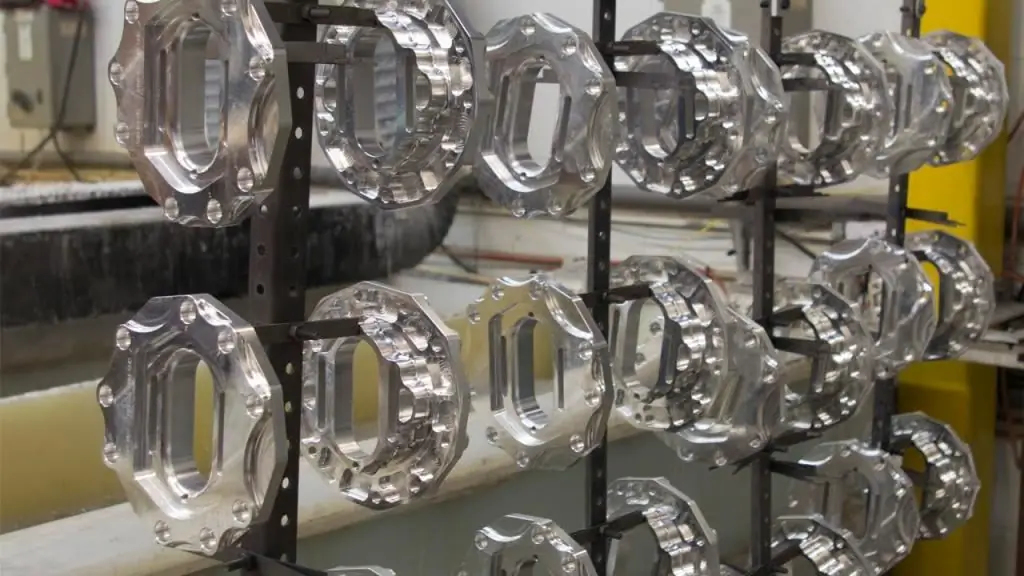
Pourquoi est-ce fait
Finition anodisée utilisée si nécessaireoffrent une protection contre la corrosion et évitent une usure accrue des pièces en contact des mécanismes et des dispositifs. Parmi les autres méthodes de protection de surface des métaux, cette technologie est l'une des moins chères et des plus fiables. L'utilisation la plus courante de l'anodisation est de protéger l'aluminium et ses alliages. Comme vous le savez, ce métal, qui possède des propriétés uniques telles qu'une combinaison de légèreté et de résistance, a une sensibilité accrue à la corrosion. Cette technologie a également été développée pour un certain nombre d'autres métaux non ferreux: titane, magnésium, zinc, zirconium et tantale.
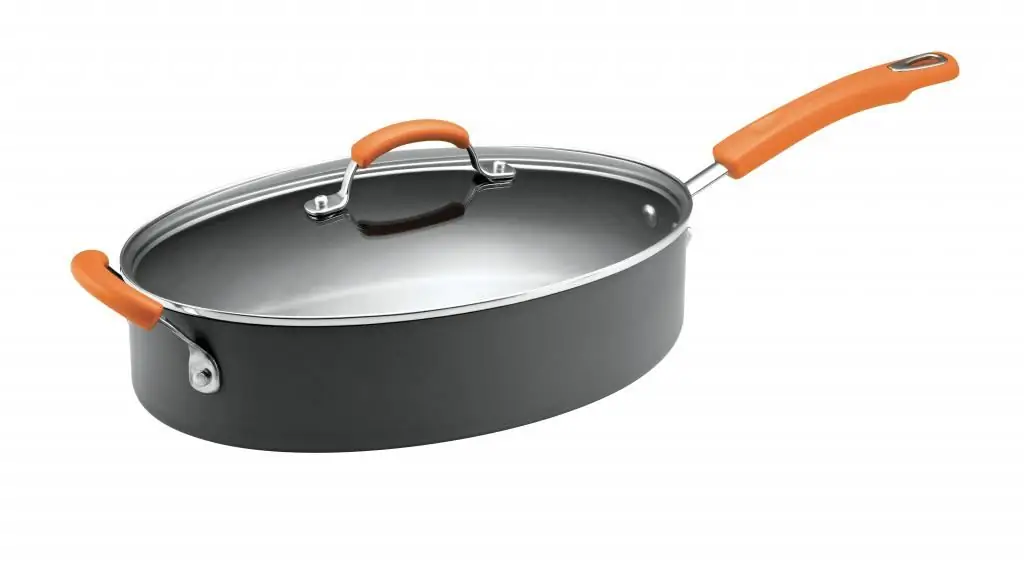
Quelques fonctionnalités
Le processus à l'étude, en plus de modifier la texture microscopique de la surface, modifie également la structure cristalline du métal à la frontière avec le film protecteur. Cependant, avec une grande épaisseur du revêtement anodisé, la couche protectrice elle-même a généralement une porosité importante. Par conséquent, afin d'obtenir une résistance à la corrosion du matériau, son étanchéité supplémentaire est nécessaire. Dans le même temps, une couche épaisse offre une résistance à l'usure accrue, bien plus que les peintures ou autres revêtements, tels que la pulvérisation. Au fur et à mesure que la résistance de la surface augmente, elle devient plus fragile, c'est-à-dire plus sensible à la fissuration due à la fissuration thermique, chimique et par impact. Les fissures dans le revêtement anodisé lors de l'estampage ne sont en aucun cas rares, et les recommandations développées ne sont pas toujours utiles ici.
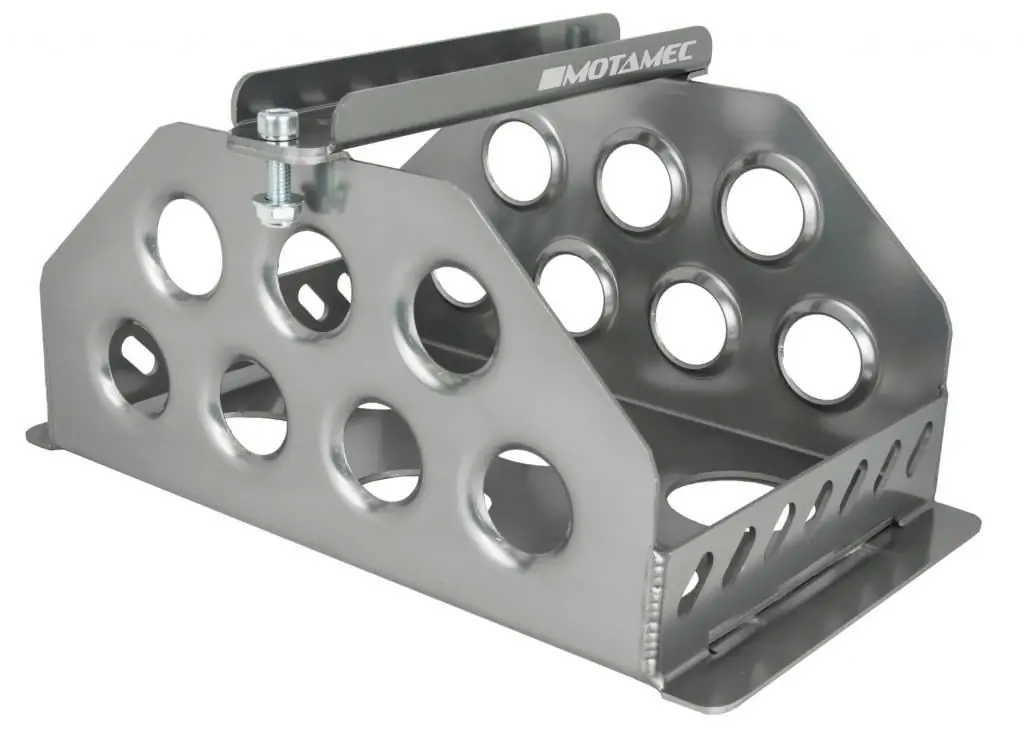
Invention
Première documentéel'utilisation enregistrée de l'anodisation a eu lieu en 1923 en Angleterre pour protéger les pièces d'hydravion de la corrosion. Initialement, l'acide chromique a été utilisé. Plus tard, l'acide oxalique a été utilisé au Japon, mais aujourd'hui, dans la plupart des cas, l'acide sulfurique classique est utilisé pour créer un revêtement anodisé dans la composition de l'électrolyte, ce qui réduit considérablement le coût du processus. La technologie est constamment améliorée et développée.
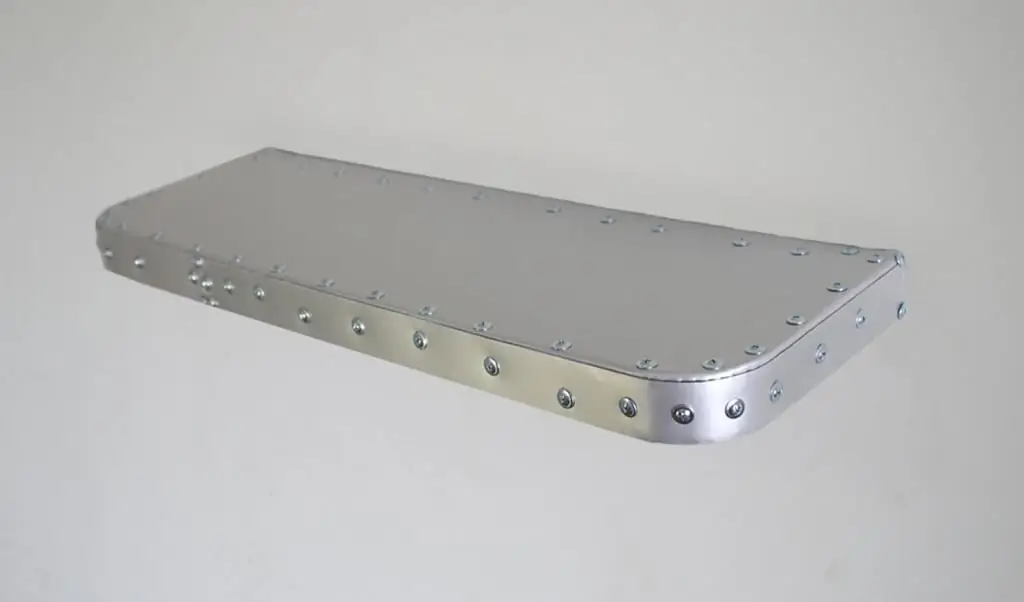
Aluminium
Anodisé pour améliorer la résistance à la corrosion et préparer la peinture. Et aussi, selon la technologie utilisée, soit pour augmenter la rugosité, soit pour créer une surface lisse. Dans le même temps, l'anodisation en elle-même n'est pas capable d'augmenter de manière significative la résistance des produits fabriqués à partir de ce métal. Lorsque l'aluminium entre en contact avec l'air ou tout autre gaz contenant de l'oxygène, le métal forme naturellement une couche d'oxyde de 2 à 3 nm d'épaisseur à sa surface et, sur les alliages, sa valeur atteint 5 à 15 nm.
L'épaisseur du revêtement en aluminium anodisé est de 15 à 20 microns, c'est-à-dire que la différence est de deux ordres de grandeur (1 micron est égal à 1000 nm). Dans le même temps, cette couche créée est répartie dans des proportions égales, relativement parlant, à l'intérieur et à l'extérieur de la surface, c'est-à-dire qu'elle augmente l'épaisseur de la pièce de la moitié de la taille de la couche de protection. Bien que l'anodisation produise un revêtement dense et uniforme, les fissures microscopiques qui y sont présentes peuvent entraîner de la corrosion. De plus, la couche protectrice de surface elle-même est sujette à la dégradation chimique.en raison de l'exposition à un environnement à forte acidité. Pour lutter contre ce phénomène, on utilise des technologies qui réduisent le nombre de microfissures et introduisent des éléments chimiques plus stables dans la composition des oxydes.
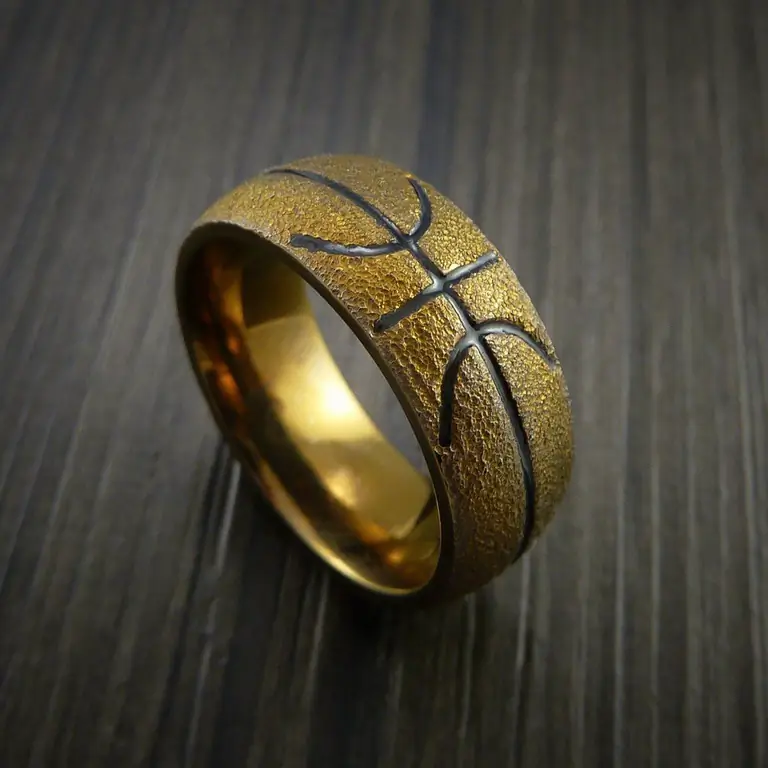
Demande
Les matériaux usinés sont largement utilisés. Par exemple, dans l'aviation, de nombreux éléments de structure contiennent des alliages d'aluminium à l'étude, la même situation est dans la construction navale. Les propriétés diélectriques du revêtement anodisé ont déterminé son utilisation dans les produits électriques. Les produits fabriqués à partir de matériaux transformés peuvent être trouvés dans divers appareils électroménagers, y compris les lecteurs, les lumières, les appareils photo, les smartphones. Dans la vie de tous les jours, un revêtement en fer anodisé est utilisé, plus précisément ses semelles, ce qui améliore considérablement ses propriétés de consommation. Lors de la cuisson, des revêtements spéciaux en téflon peuvent être utilisés pour éviter de brûler les aliments. Habituellement, ces ustensiles de cuisine sont assez chers. Cependant, une poêle à frire en aluminium non anodisé est en mesure d'apporter une solution au même problème. En même temps, à moindre coût. Dans la construction, le revêtement anodisé des profilés est utilisé pour le montage des fenêtres et d'autres besoins. De plus, les détails colorés attirent l'attention des designers et des artistes, ils sont utilisés dans divers objets culturels et artistiques du monde entier, ainsi que dans la fabrication de bijoux.
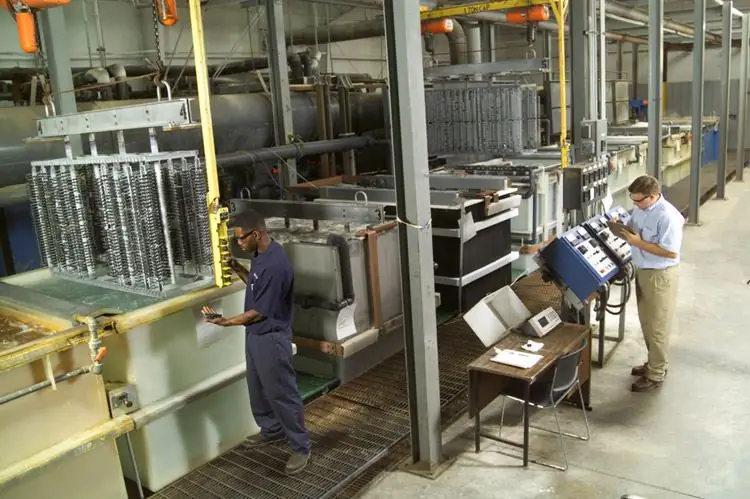
Technologie
Ateliers spéciaux de galvanoplastie etindustries considérées comme "sales" et nocives pour la santé humaine. Par conséquent, les recommandations pour le processus à domicile, annoncées dans certaines sources, doivent être prises avec une extrême prudence, malgré l'apparente simplicité des technologies décrites.
Le revêtement anodisé peut être créé de plusieurs manières, mais le principe général et la séquence de travail restent classiques. En même temps, la résistance et les propriétés mécaniques du matériau obtenu dépendent en fait du métal source lui-même, des caractéristiques de la cathode, de l'intensité du courant et de la composition de l'électrolyte utilisé. Il convient de souligner qu'à la suite de la procédure, aucune substance supplémentaire n'est appliquée sur la surface et la couche protectrice est formée en transformant le matériau source lui-même. L'essence de la galvanoplastie est l'effet du courant électrique sur les réactions chimiques. L'ensemble du processus est divisé en trois étapes principales.
Première étape - préparation
À ce stade, le produit est soigneusement nettoyé. La surface est dégraissée et polie. Ensuite, il y a la soi-disant gravure. Elle est réalisée en plaçant le produit dans une solution alcaline, puis en le déplaçant dans une solution acide. Ces procédures sont complétées par un rinçage, au cours duquel il est extrêmement important d'éliminer tous les résidus chimiques, y compris les zones difficiles d'accès. Le résultat final dépend en grande partie de la qualité de la première étape.
Deuxième étape - électrochimie
À ce stade, le revêtement en aluminium anodisé est réellement créé. Pièce soigneusement préparéeaccroché sur des supports et descendu dans un bain d'électrolyte, placé entre deux cathodes. Pour l'aluminium et ses alliages, des cathodes en plomb sont utilisées. Habituellement, la composition de l'électrolyte comprend de l'acide sulfurique, mais d'autres acides peuvent être utilisés, par exemple oxalique, chromique, en fonction de la destination future de la pièce usinée. L'acide oxalique est utilisé pour créer des revêtements isolants de différentes couleurs, l'acide chromique est utilisé pour traiter des pièces qui ont une forme géométrique complexe avec des trous de petit diamètre.
Le temps nécessaire pour créer un revêtement protecteur dépend de la température de l'électrolyte et de la force du courant. Plus la température est élevée et plus le courant est faible, plus le processus est rapide. Cependant, dans ce cas, le film de surface est assez poreux et mou. Pour obtenir une surface dure et dense, des températures basses et une densité de courant élevée sont nécessaires. Pour l'électrolyte sulfate, la plage de température est de 0 à 50 degrés et l'intensité du courant spécifique est de 1 à 3 ampères par décimètre carré. Tous les paramètres de cette procédure ont été élaborés au fil des ans et sont contenus dans les instructions et normes pertinentes.
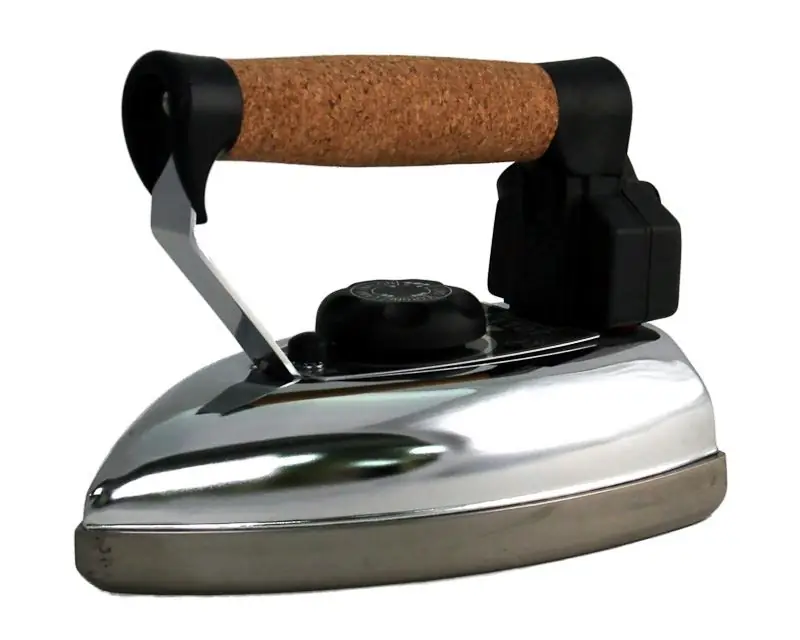
Troisième étape - consolidation
Une fois l'électrolyse terminée, le produit anodisé est fixé, c'est-à-dire que les pores du film protecteur sont fermés. Cela peut être fait en plaçant la surface traitée dans de l'eau ou dans une solution spéciale. Avant cette étape, une peinture efficace de la pièce est possible, puisque la présence de pores permettra une bonne absorption.colorant.
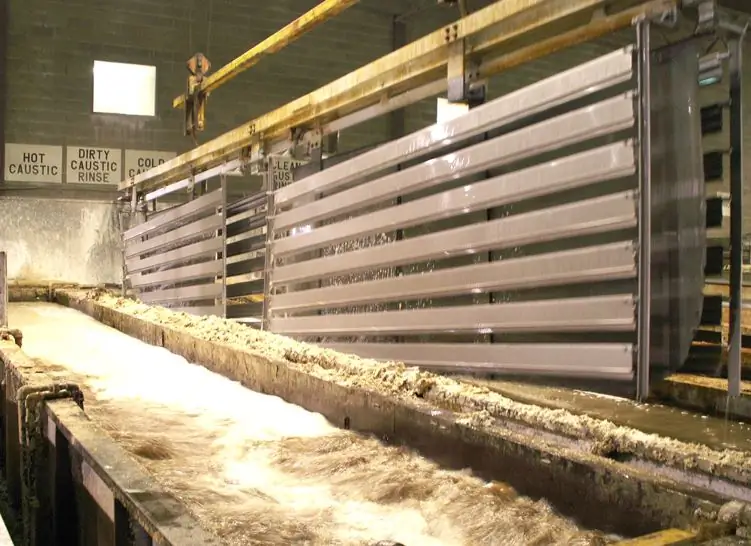
Développement de la technologie d'anodisation
Pour obtenir un film d'oxyde résistant à la surface de l'aluminium, une méthode a été développée en utilisant une composition complexe de divers électrolytes dans une certaine proportion, combinée à une augmentation progressive de la densité de courant électrique. Une sorte de "cocktail" d'acides sulfurique, tartrique, oxalique, citrique et borique est utilisé, et la force actuelle du processus augmente progressivement de cinq fois. En raison de cet effet, la structure de la cellule poreuse de la couche d'oxyde protectrice change.
Une mention spéciale doit être faite à la technologie de changement de couleur d'un objet anodisé, qui peut être fait de différentes manières. Le plus simple est de placer la pièce dans une solution avec un colorant chaud immédiatement après la procédure d'anodisation, c'est-à-dire avant la troisième étape du processus. Le processus de coloration avec l'utilisation d'additifs directement dans l'électrolyte est un peu plus compliqué. Les additifs sont généralement des sels de divers métaux ou acides organiques, vous permettant d'obtenir la gamme de couleurs la plus diversifiée - du noir absolu à presque toutes les couleurs de la palette.
Conseillé:
1/300 taux de refinancement. Où et comment est-il appliqué
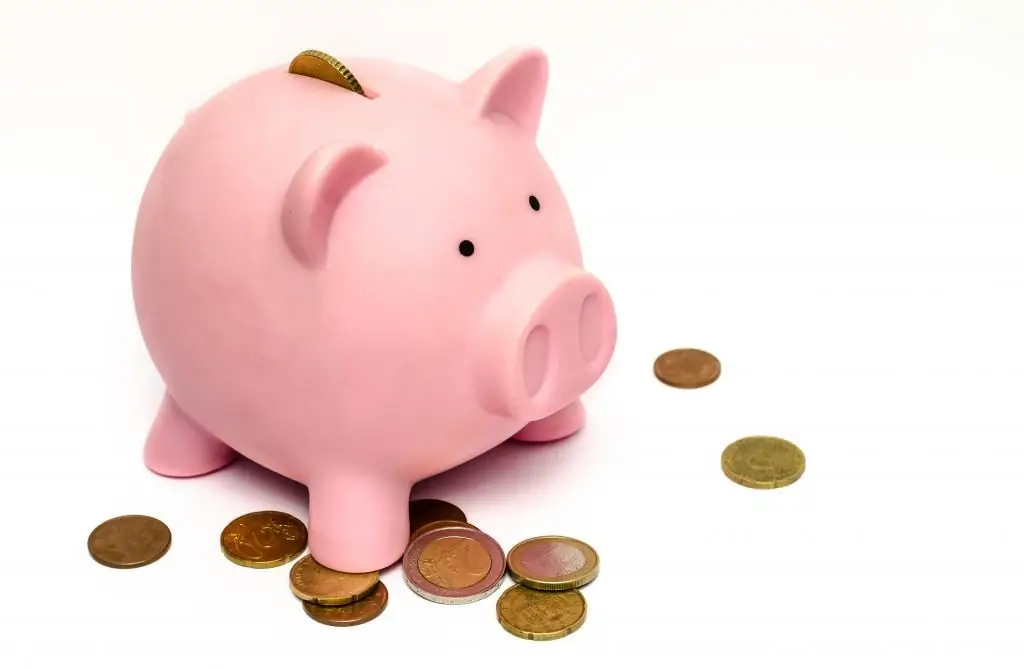
Les relations contractuelles entre les contreparties incluent la condition d'indemnisation des sanctions et amendes conformément aux exigences de l'article 395 du Code civil de la Fédération de Russie. Lorsqu'une personne voit le mot "pénalité" dans une facture de services publics ou dans le texte d'un contrat de prêt, elle souhaite déterminer si c'est beaucoup - 1/300 du taux de refinancement
Tender - qu'est-ce que c'est ? Le sens du mot et comment il est appliqué dans la pratique
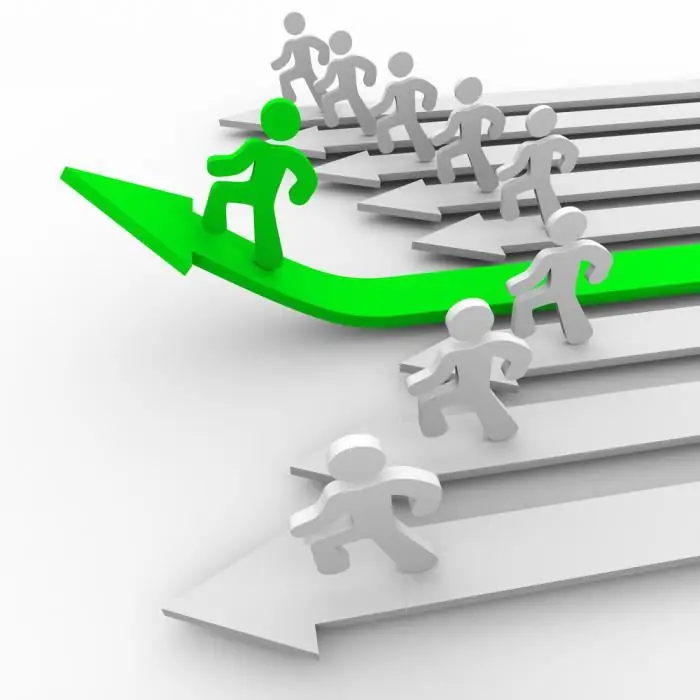
Aujourd'hui, presque tous les produits du marché sont achetés sur appel d'offres. Un appel d'offres est en fait un concours, en fonction des résultats duquel l'entreprise cliente sélectionne un fournisseur ou un entrepreneur prêt à offrir les conditions de coopération les plus favorables : prix bas, solutions originales ou professionnalisme inégalé
De quoi est composé le lait ? Comment est fabriqué le lait en poudre ?
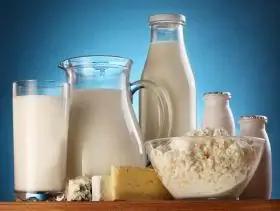
Tout le monde est sûrement préoccupé par la question de savoir de quoi est fait le lait. Dans cet article, nous allons essayer d'y trouver des réponses et d'en apprendre beaucoup sur ce produit familier depuis l'enfance
À partir de quoi et comment est fabriqué le saucisson ?
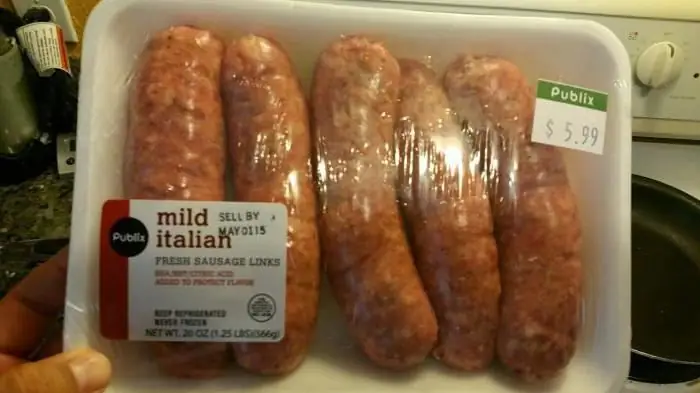
Combien de personnes aimeraient savoir comment la saucisse est réellement fabriquée. Après tout, ce produit est en fait très populaire et en demande. Il existe diverses rumeurs sur la fabrication des saucisses dans les entreprises modernes
Aluminium anodisé. Revêtement spécial pour le matériel
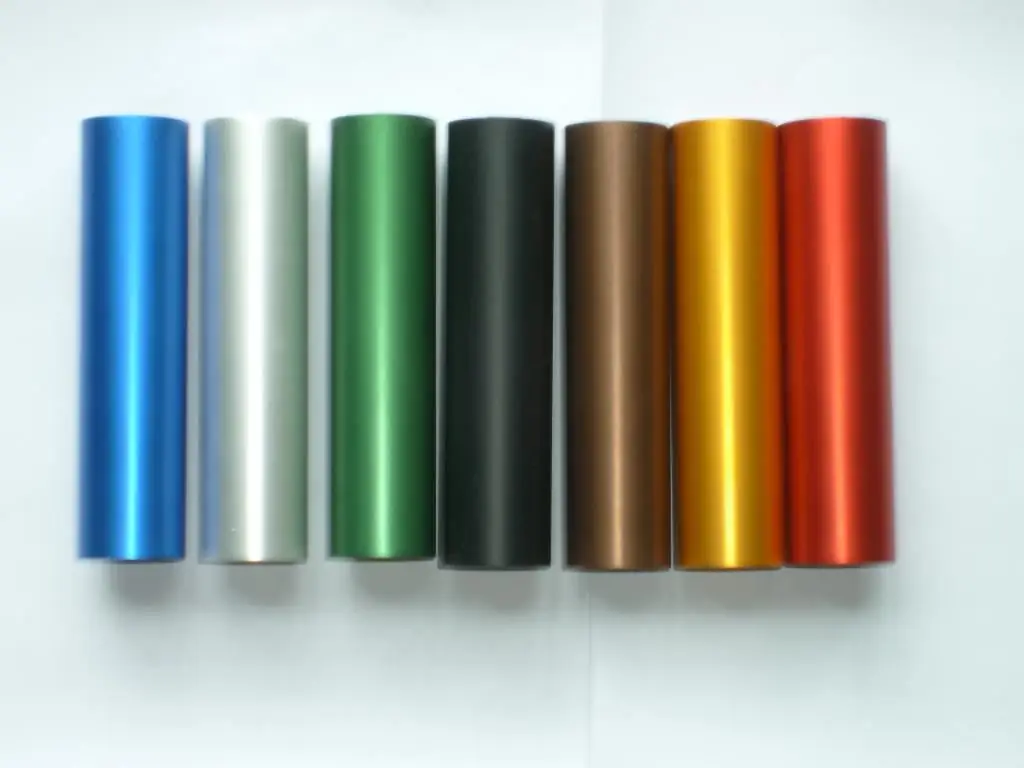
L'aluminium lui-même est un matériau très léger qui peut être bien usiné. Cependant, lors de l'interaction avec l'oxygène, cette substance s'oxyde assez rapidement, c'est pourquoi il est impossible de l'utiliser pour la vaisselle, par exemple. Cependant, l'aluminium anodisé a résolu presque tous les problèmes