2025 Auteur: Howard Calhoun | [email protected]. Dernière modifié: 2025-01-24 13:16
La coulée dans des moules en coquille est également appelée coulée en coquille. Et à l'étranger, cette méthode de travail s'appelle Shell.
Informations générales
Dans l'industrie industrielle d'aujourd'hui, de nombreuses méthodes de moulage différentes sont utilisées. En plus du moulage en coquille, le moulage à la cire perdue est également utilisé, ainsi que dans les moules métalliques et plusieurs autres méthodes. L'avantage global de ces méthodes de moulage, par rapport au moulage au sable, est qu'elles permettent d'obtenir des matériaux finaux plus précis en termes de forme et de dimensions. De plus, le nombre de rugosités à la surface de tels produits est réduit. Dans des cas plus rares, mais il arrive quand même que la nécessité d'un usinage ultérieur après la fusion soit éliminée. En plus de tout, l'utilisation de la coulée dans des moules en coquille et d'autres méthodes contribue au fait que ce processus peut être mécanisé autant que possible, ce qui augmente également son automatisation. Et cela, bien sûr, augmente considérablement la productivité de toute installation industrielle.
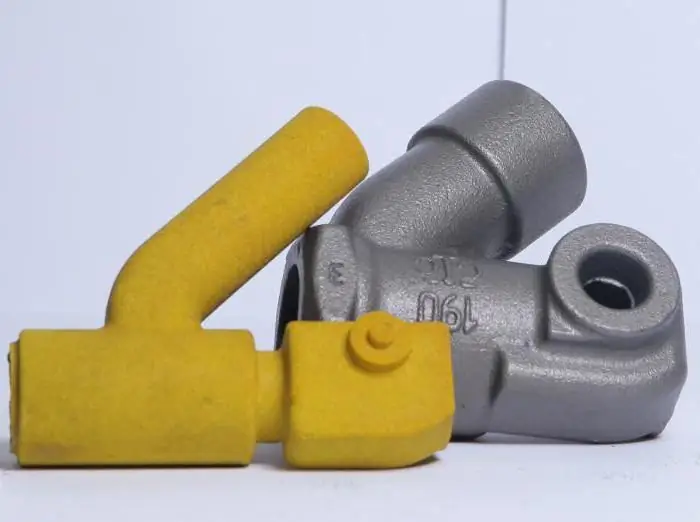
Coquillage
Si nous parlons spécifiquement de celaméthode, elle a été introduite pour la première fois dans les usines en 1953. À l'heure actuelle, la méthode est utilisée assez largement. C'est par exemple la coulée en moules carapaces qui produit la plupart des pièces du tracteur Kirovets. Toutes les pièces produites à l'aide de cette méthode sont de la plus haute qualité en acier ou en fonte. La coulée en coquille est une méthode dans laquelle le résultat final de la coulée a une forme composée de deux coquilles de sable et de résine. De plus, cette méthode de fabrication de pièces n'est utilisée que dans les cas où il est nécessaire de créer une pièce de petites ou moyennes dimensions, mais en même temps avec une grande précision. Des exemples d'applications pour cette méthode de moulage sont les pièces de moteur ou les pièces moulées à paroi mince.
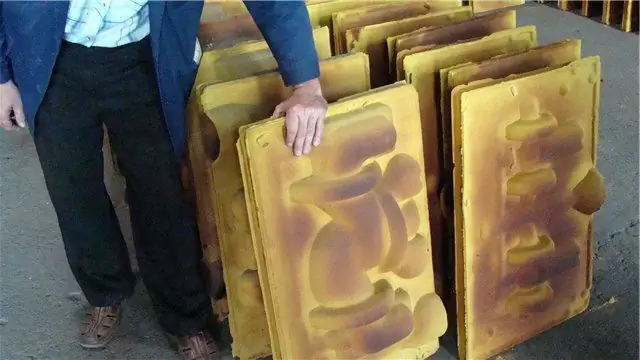
L'essence du chemin
Avec cette méthode de travail, vous pouvez obtenir diverses pièces pour ventilateurs, moteurs, pompes ou machines textiles. Cependant, la longueur maximale du produit reçu ne peut pas dépasser 1 mètre et il ne peut pas peser plus de 200 kg.
L'essence de la coulée dans des moules carapaces repose sur certaines propriétés des résines thermodurcissables, qui font partie des mélanges sable-résine. L'avantage d'utiliser de tels composants est que ces résines ont tendance à durcir rapidement et de façon permanente lorsqu'elles sont traitées à une température de 200 à 250 degrés Celsius.
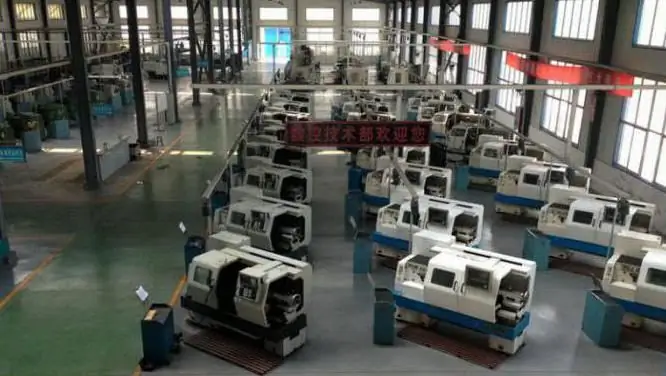
Fabriquer un moule carapace pour la coulée
Afin de fabriquer un moule pour une coulée ultérieure, il est nécessaire de disposer de sable de quartz à grain fin, qui vient avec l'ajout d'une résine thermodurcissable, qui est son élément de liaison pour obtenir un moule carapace à part entière. Ces matériaux, notamment la résine, sont choisis car ils durcissent lorsqu'ils franchissent une certaine barrière de température. Le processus de fabrication est le suivant. Tout d'abord, la résine est chauffée à 140-160 degrés Celsius. Sous l'influence d'un tel environnement, il se transforme en une masse adhésive liquide qui enveloppe complètement le moule en sable de quartz.
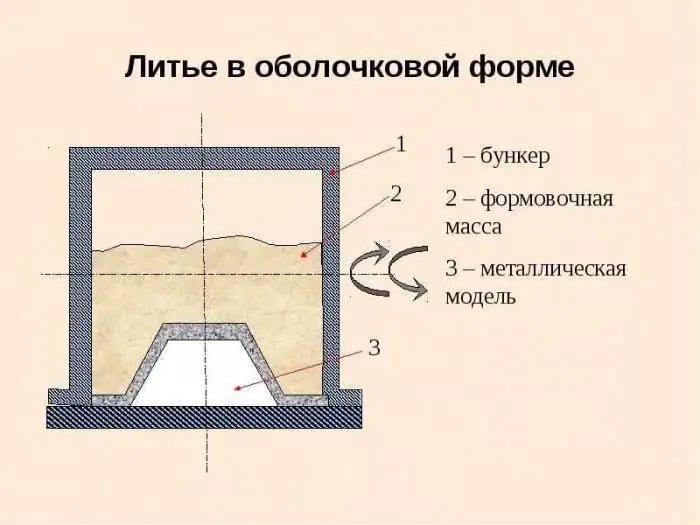
Le champ d'application de la coulée dans des moules en coquille est assez large et, par conséquent, le processus de fabrication des moules est amené à être automatique ou automatisé.
Une fois le moule entièrement recouvert de résine, la température est augmentée à 200-250 degrés Celsius. Ce seuil de température est tout à fait suffisant pour que la masse adhésive durcisse de manière irréversible et prenne une forme. De plus, lorsque le processus de coulée des pièces commence, c'est-à-dire lorsque le métal en fusion pénètre dans le moule, la température y atteint environ 600 degrés. Ce mode est suffisant pour garantir que la résine ne fond pas, mais brûle, tout en laissant des pores sur le moule lui-même, facilitant l'échappement des gaz.
Avantages et inconvénients du moulage en carapace
Comme tout autre processus de fabrication, celui-ci a ses avantages et ses inconvénients. Si nous comparons cette méthode de moulage, par exemple, avec le moulage enmoules à sable ordinaires, il y a plusieurs avantages:
- La première différence plutôt significative est la classe de précision, qui est de 7 à 9. De plus, l'état de surface de la pièce obtenue est amélioré jusqu'à 3-6. De plus, les tolérances sont réduites, ce qui est autorisé pour l'usinage ultérieur de la pièce résultante après la coulée.
- L'un des grands avantages est une réduction significative des coûts de main-d'œuvre pour la fabrication de pièces moulées.
- Cette méthode de moulage réduit la consommation de matériaux de moulage, ainsi que la quantité de métal en raison du fait que la taille des canaux de grille est réduite.
- A considérablement réduit le montant de la production de mariage.
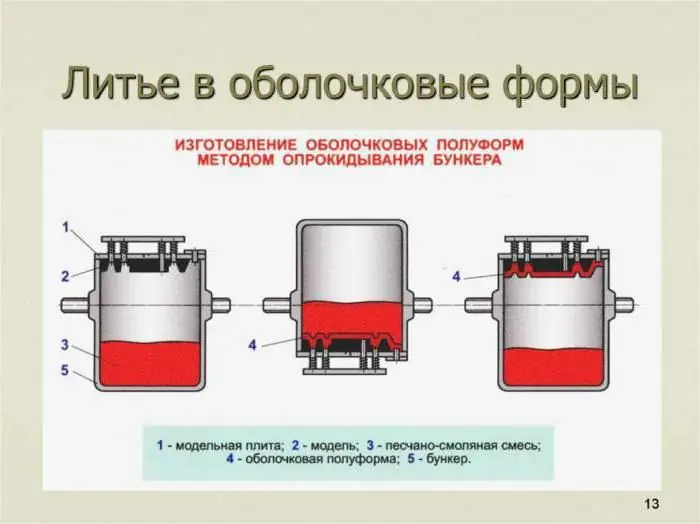
Cependant, il y a quelques inconvénients à couler dans des moules carapaces. Ceux-ci incluent:
- Durée de vie du moule - 1 moulage.
- Le coût du moulage du sable est assez élevé.
- Pourcentage élevé de gaz nocifs.
Processus de formation de corpus
Le processus de formation du corps se déroule en six étapes:
- La première étape consiste à verser le mélange sur un modèle en métal chaud, ainsi qu'à le conserver pendant plusieurs dizaines de secondes jusqu'à ce qu'une fine croûte solide se forme autour de la pièce. Le plus souvent, les modèles sont en fonte et leur chauffage est effectué jusqu'à 230-315 degrés.
- Après cela, il est nécessaire d'effectuer une opération pour éliminer l'excès de sable de moulage. L'épaisseur de la croûte devrait éventuellement être de 10 à 20mm. Cela dépend du temps de séjour du mélange sur le modèle, ainsi que de la température.
- Après cela, il est nécessaire de transférer la plaque modèle avec le moule dans le four, où ils resteront jusqu'à la fin du processus de durcissement. Au terme de cette procédure, la résistance de la coque doit être comprise entre 2,4 et 3,1 MPa.
- Après avoir été retirée du four, la coque durcie est déplacée de la plaque. Un poussoir spécial est utilisé pour cette procédure.
- Après cela, deux modèles ou plus sont attachés ensemble à l'aide d'une sorte de pince ou par collage. Ces moules peuvent être utilisés pour la coulée dans des moules carapaces ou simplement stockés. Durée de conservation presque illimitée.
- Avant de commencer le processus de coulée dans le moule fini, de la grenaille y est versée, ce qui aide à empêcher ou à détruire le moule lors de la coulée ultérieure.
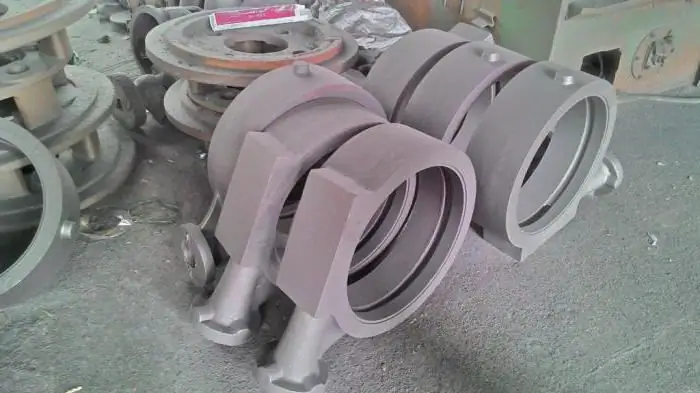
Détails du casting
Il vaut la peine de commencer par le fait que les tolérances typiques autorisées dans la fabrication d'outils peuvent être de 0,5 mm. La rugosité de surface est autorisée dans la plage de 0,3 à 0,4 microns. Ces limites sont justifiées par le fait que du sable fin est utilisé. A noter également: l'utilisation de résine contribue grandement au fait que la surface est très lisse.
Volumes de production
Pour être engagé dans la production de tels moules et pièces, il est nécessaire d'assister à l'installation d'un modèle de moule. Le temps nécessaire à l'installation est inférieur à une semaine. Une fois l'installation terminée, la quantité de sortie peutatteindre de 5 à 50 pièces par heure. De tels volumes de production par heure sont bien réels, cependant, pour cela, il est nécessaire de préparer le processus de coulée en conséquence. Les principaux matériaux qui seront nécessaires pour la coulée sont la fonte, l'aluminium, le cuivre, ainsi que les alliages de ces types de métaux. Un autre matériau nécessaire sera un alliage qui utilise de l'aluminium et du magnésium.
Conseillé:
Contrôle des opérations de trésorerie de la banque. Vue d'ensemble des systèmes de contrôle des opérations en espèces
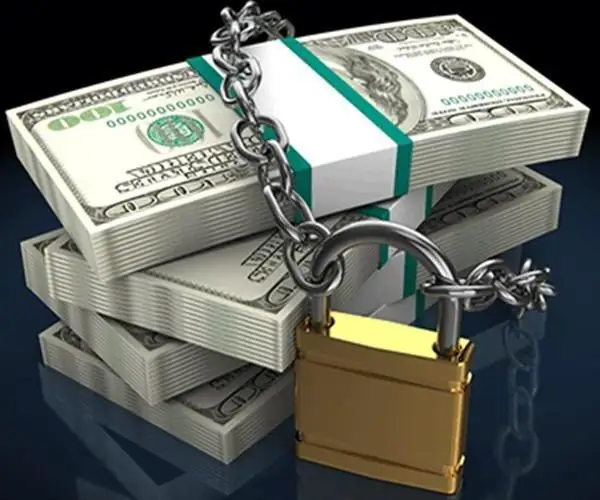
Étant donné que divers types de fraudes se produisent souvent dans le domaine de la comptabilité des caisses enregistreuses, le contrôle des transactions en espèces devient chaque année de plus en plus compliqué, plus strict et modernisé. Cet article traite du rôle de la caisse dans l'entreprise, des règles de conduite, ainsi que des méthodes et systèmes de suivi des opérations
Opérations REPO. Opérations REPO avec des titres
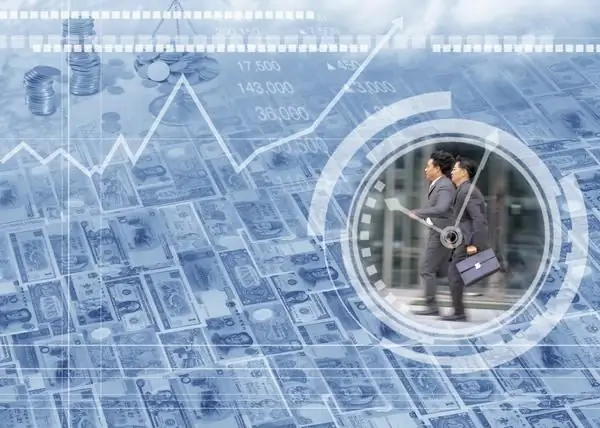
REPO sont des procédures au cours desquelles s'effectue la vente de tous objets de valeur, accompagnée de leur rachat après un délai déterminé à un prix fixé au moment de l'opération. L'achat inversé est obligatoire, représentant la dernière (deuxième) étape de la transaction
Opérations de trésorerie et de crédit des banques. Types d'opérations bancaires
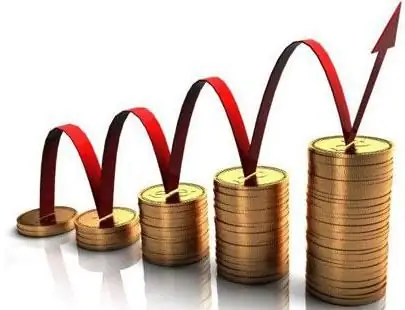
Les principales opérations qu'effectue une banque commerciale sont le crédit et la trésorerie. Quelles sont leurs spécificités ? Selon quelles règles sont-elles réalisées ?
Une opération de conversion est Types d'opérations de conversion. Opérations de conversion
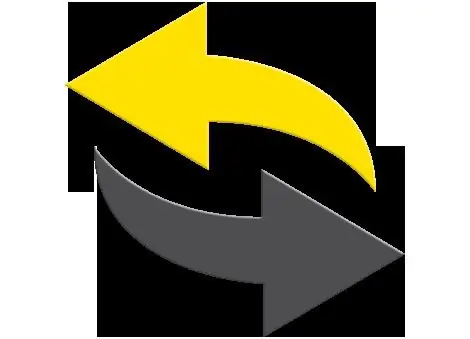
Une opération de conversion est une opération effectuée par les participants au marché des changes pour échanger la monnaie d'un État contre l'unité monétaire d'un autre. Dans le même temps, leurs volumes sont convenus à l'avance, tout comme le cours avec des règlements après un certain temps. Si l'on considère le concept d'un point de vue juridique, on peut conclure qu'une opération de conversion est une opération d'achat et de vente de devises
Types d'opérations bancaires. Services de règlement et de trésorerie. Opérations des banques avec des titres
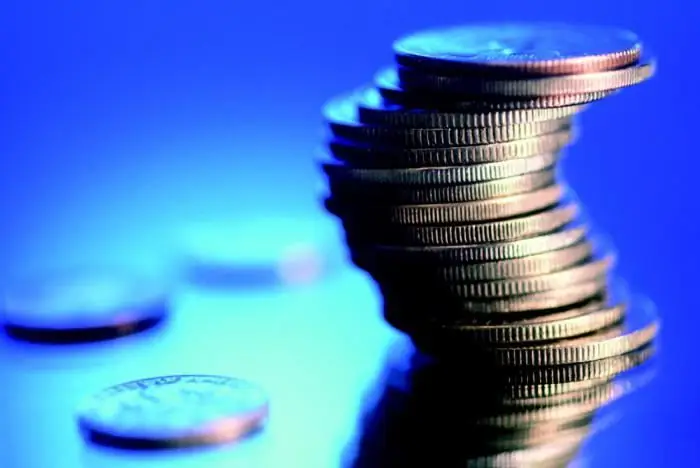
Avant de savoir quels types de transactions bancaires existent, vous devez comprendre certaines des définitions les plus importantes. Par exemple, quelle est l'institution en question elle-même ? Dans la terminologie économique moderne, la banque agit comme une unité financière et de crédit qui effectue toutes sortes d'opérations avec de l'argent et des titres